Applying CATIA in Thermodynamics: A Practical Approach for Students
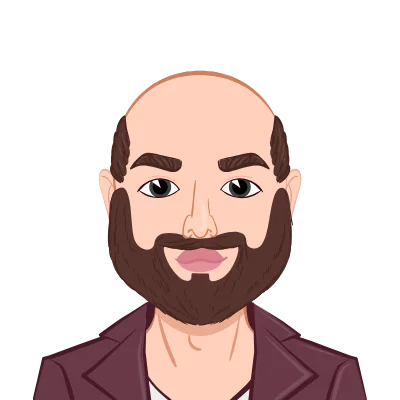
In the dynamic realm of mechanical engineering, the integration of cutting-edge technologies is paramount to meet the challenges posed by complex problem-solving and innovative design. Among the myriad tools available, Computer-Aided Design (CAD) emerges as a cornerstone, revolutionizing the way engineers conceptualize, design, and analyze mechanical systems. One such powerful CAD tool that has gained prominence is CATIA (Computer-Aided Three-Dimensional Interactive Application). Its significance is particularly pronounced when applied to the intricacies of thermodynamics—a branch of physics and engineering that delves into the principles governing energy transfer and transformation within mechanical systems.
The application of CAD tools in the realm of mechanical engineering, and more specifically in thermodynamics, marks a paradigm shift in traditional problem-solving methodologies. CAD tools like CATIA empower engineers and students alike with a virtual environment where they can model, simulate, and analyze complex thermodynamic systems with unprecedented precision. The conventional approach to thermodynamics often involves theoretical calculations and manual analysis, which can be time-consuming and prone to errors. CATIA, however, introduces a transformative dimension by offering a virtual platform where engineers can visualize thermodynamic processes in three dimensions, allowing for a more intuitive understanding of the systems at play.
CATIA's relevance in solving problems related to thermodynamics lies in its ability to bridge the gap between theoretical concepts and practical applications. By providing a comprehensive set of tools for 3D modeling, simulation, and analysis, CATIA enables engineers to simulate thermodynamic processes with a level of accuracy that was previously unattainable. This not only aids in validating theoretical assumptions but also allows for the exploration of diverse scenarios, optimizing designs and ensuring efficiency in energy systems. For students, the integration of CATIA in thermodynamics education offers a unique opportunity to grasp abstract concepts through hands-on experience, fostering a deeper understanding of the subject matter.
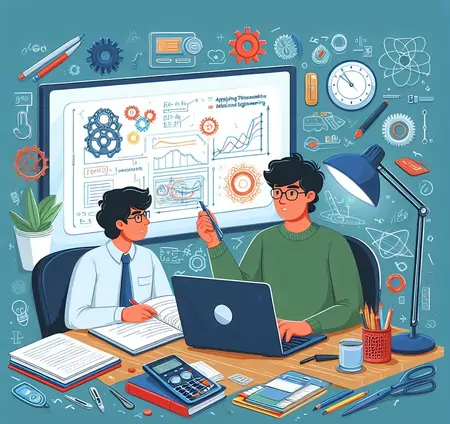
Moreover, CATIA's real-time simulation capabilities empower engineers to observe and analyze the behavior of thermodynamic systems under various conditions. This is invaluable in predicting performance outcomes, identifying potential issues, and refining designs before they manifest in the physical realm. The ability to virtually prototype and test thermodynamic concepts in a risk-free environment accelerates the innovation cycle, enabling engineers to iterate through design improvements rapidly.
In the context of renewable energy systems and sustainable engineering practices, CATIA's role becomes even more pronounced. Thermodynamics plays a crucial role in optimizing energy conversion processes, and CATIA facilitates the design and analysis of components such as turbines, heat exchangers, and compressors. By streamlining the development of energy-efficient systems, CATIA contributes directly to the advancement of environmentally conscious engineering solutions.
In conclusion, the integration of CAD tools, particularly CATIA, in the field of mechanical engineering opens new frontiers in the understanding and application of thermodynamics. Its ability to provide a virtual playground for engineers and students to explore, simulate, and optimize thermodynamic systems enhances the problem-solving capabilities of the industry and contributes to the evolution of sustainable and efficient mechanical designs. As we navigate the complexities of modern engineering challenges, CATIA stands as a beacon, illuminating a path toward innovation and excellence in the realm of thermodynamics. If you require assistance with your CATIA assignment, it's crucial to leverage the capabilities of this powerful tool to further advance your understanding and application of thermodynamic principles.
CATIA Overview
CATIA, which stands for Computer-Aided Three-Dimensional Interactive Application, is an advanced and comprehensive Computer-Aided Design (CAD) software suite developed by Dassault Systèmes. Recognized as a pioneer in the CAD industry, CATIA has established itself as an indispensable tool for engineers across various disciplines, offering a versatile platform that extends far beyond conventional design software. Its multifaceted features and capabilities make it a powerhouse for mechanical engineers, and its application in the context of thermodynamics sets it apart as an exceptional tool for tackling complex challenges.
At its core, CATIA is renowned for its robust 3D modeling capabilities. The software provides a highly intuitive and interactive environment where engineers can create intricate and realistic 3D models of mechanical components and systems. This includes the ability to design complex shapes, analyze geometric relationships, and simulate the behavior of components under different conditions. The parametric modeling feature allows for the easy modification of designs, ensuring adaptability to changing project requirements—a crucial aspect for engineers dealing with the dynamic nature of thermodynamic systems.
One of CATIA's standout features is its advanced simulation and analysis capabilities. Engineers can use CATIA to perform detailed simulations of thermodynamic processes, including heat transfer, fluid dynamics, and energy conversion. The software's integrated analysis tools facilitate the exploration of various scenarios, enabling engineers to optimize designs for efficiency and performance. This simulation-driven design approach is particularly beneficial in the field of thermodynamics, where understanding the dynamic behavior of systems is essential for effective problem-solving and innovation.
CATIA's collaborative and integrated design environment is another key factor that distinguishes it in the realm of mechanical engineering. The software allows multiple engineers to work concurrently on different aspects of a project, fostering seamless collaboration and accelerating the design process. This collaborative approach is instrumental in addressing the multifaceted challenges posed by thermodynamics, where interdisciplinary collaboration is often required to achieve holistic solutions.
Moreover, CATIA's ability to integrate with other engineering disciplines, such as structural analysis and kinematics, enhances its utility in the broader context of mechanical engineering. In thermodynamics, where interactions between mechanical, thermal, and fluid systems are prevalent, this interdisciplinary integration proves invaluable for engineers striving to create comprehensive and optimized designs.
In summary, CATIA's comprehensive 3D modeling, simulation, and collaborative capabilities position it as a formidable tool for engineers in the field of thermodynamics. Its adaptability, real-time simulation, and integration with various engineering disciplines make it a go-to solution for addressing the intricacies of designing and analyzing thermodynamic systems. As engineers navigate the complexities of energy transfer and transformation, CATIA stands as a versatile ally, empowering them to innovate, optimize, and excel in the realm of mechanical engineering.
Integration of CATIA and Thermodynamics
CATIA's seamless integration into the study and application of thermodynamics is a testament to its diverse features and functionalities that cater specifically to the complex requirements of this field. One of the key strengths of CATIA lies in its ability to facilitate detailed 3D modeling, allowing engineers and students to create virtual representations of thermodynamic systems. This feature becomes particularly valuable when dealing with intricate components such as heat exchangers, turbines, and compressors, enabling a visual and tangible understanding of the spatial relationships and interactions within these systems.
CATIA's parametric modeling capabilities enhance its applicability in thermodynamics by enabling engineers to create design variants easily. This adaptability is crucial when exploring different configurations of thermodynamic systems or optimizing designs for efficiency. The ability to modify parameters and instantly observe their impact on the overall system facilitates a more intuitive and iterative design process, essential for solving complex thermodynamics problems.
Furthermore, CATIA's simulation and analysis tools provide a sophisticated environment for studying thermodynamic processes. The software allows engineers to simulate heat transfer, fluid dynamics, and other thermodynamic phenomena, offering a comprehensive understanding of system behavior. Engineers can employ CATIA to analyze the thermal performance of components, study fluid flow patterns, and assess energy conversion efficiency—all critical aspects of thermodynamics. The real-time feedback provided by these simulations empowers users to make informed decisions and refine designs for optimal performance.
CATIA's integration with computational fluid dynamics (CFD) modules enhances its capabilities in solving thermodynamics problems. Engineers can use CFD simulations within CATIA to analyze heat transfer, airflow, and pressure distribution, providing detailed insights into the thermodynamic behavior of components. This level of analysis is invaluable in optimizing the performance of thermal systems and ensuring that designs meet specified criteria.
Collaboration is another area where CATIA shines in the context of thermodynamics. Its collaborative design environment allows multiple team members to work simultaneously on different aspects of a project. This feature is especially beneficial for interdisciplinary projects involving thermodynamics, where input from mechanical, thermal, and fluid dynamics experts is essential. The seamless collaboration within CATIA fosters efficient communication and ensures that all facets of thermodynamics are considered during the design process.
In conclusion, CATIA's integration into the study and application of thermodynamics is marked by its 3D modeling capabilities, parametric design features, simulation tools, and collaborative environment. These features collectively empower engineers and students to delve deeply into the complexities of thermodynamic systems, offering a holistic platform for modeling, analyzing, and optimizing designs. As a result, CATIA emerges as an invaluable tool for those seeking to solve real-world thermodynamics problems and push the boundaries of innovation in mechanical engineering.
Practical Examples
Let's consider a practical example to illustrate the application of CATIA in solving thermodynamics problems—a simplified case of modeling and analyzing a heat exchanger system. This step-by-step walkthrough will demonstrate how CATIA's features aid in the design and analysis of a crucial thermodynamic component.
- Initial 3D Modeling:
- Assembly and Component Relations:
- Applying Material Properties:
- Simulation Setup:
- Running the Analysis:
- Optimization Iterations:
Begin by creating a 3D model of the heat exchanger in CATIA's design environment. Use the software's parametric modeling tools to define the geometry, dimensions, and materials. Incorporate features like tubes, fins, and the overall casing, ensuring accuracy in representation.
Leverage CATIA's assembly capabilities to bring together individual components of the heat exchanger. Establish relationships between parts, such as defining how tubes connect to the casing or how fins are positioned within the assembly. CATIA's associativity ensures that any changes made to one part automatically update related components.
Assign material properties to different parts of the heat exchanger using CATIA's material assignment tools. This step is crucial for accurate simulation and analysis, as it ensures that the software considers the varying thermal conductivities and other material characteristics of different components.
Access CATIA's simulation tools to set up a thermal analysis of the heat exchanger. Define boundary conditions, such as inlet and outlet temperatures and fluid flow rates. CATIA's simulation modules, including thermal and fluid dynamics analyses, enable engineers to simulate the heat transfer within the system.
Execute the simulation within CATIA to observe the heat exchange patterns, temperature distributions, and fluid flow paths. CATIA's real-time analysis capabilities provide visual feedback, allowing engineers to identify potential issues or areas for optimization.
Based on the simulation results, iterate through the design to optimize the heat exchanger for improved performance. Adjust parameters such as fin density, tube arrangements, or overall dimensions, and observe the impact on the system's thermodynamic efficiency.
This practical example showcases how CATIA facilitates a comprehensive approach to modeling and analyzing thermodynamic systems. The software's parametric design, assembly features, material assignment, and simulation tools collectively empower engineers to not only create accurate representations of components but also gain insights into their thermal behavior. The integration of CATIA into the thermodynamics workflow accelerates the design process, fosters innovation, and ensures that engineers can make informed decisions for optimizing system performance.
Benefits for Students
Incorporating CATIA into thermodynamics studies provides students with a myriad of benefits that extend beyond traditional theoretical learning, offering a dynamic and hands-on approach to understanding complex engineering concepts. One of the primary advantages lies in the enhancement of students' understanding of thermodynamics through practical application. CATIA's 3D modeling capabilities enable students to visualize abstract thermodynamic principles, transforming theoretical concepts into tangible and interactive models. This visual representation fosters a deeper comprehension of the relationships between components, fluid flow, and heat transfer within thermodynamic systems.
Moreover, the use of CATIA in thermodynamics studies sharpens students' problem-solving skills by immersing them in real-world scenarios. As students engage in the step-by-step process of modeling, simulating, and analyzing thermodynamic systems, they develop a practical and intuitive problem-solving approach. CATIA's parametric design features encourage experimentation, allowing students to explore the impact of design variations on system performance. This iterative process not only hones their analytical skills but also instills a mindset of continuous improvement—a vital attribute in the engineering field.
CATIA's integration of simulation tools introduces students to a virtual laboratory where they can test their theoretical knowledge in a risk-free environment. By running simulations that mimic real-world conditions, students gain valuable insights into the behavior of thermodynamic systems. This not only reinforces theoretical concepts but also provides a bridge between classroom learning and real-world applications. As students witness the consequences of design choices on thermal performance, they develop a nuanced understanding of the complexities involved in engineering design, preparing them for the challenges they may encounter in their future careers.
Furthermore, incorporating CATIA into thermodynamics studies equips students with practical skills highly relevant to the demands of the modern engineering industry. Many engineering firms utilize CAD tools extensively, and proficiency in CATIA enhances students' employability. As students become adept at using CATIA for thermodynamic analysis and design, they gain a competitive edge in the job market. This hands-on experience also prepares them for collaborative work environments, where interdisciplinary collaboration is common, and effective communication through visual models is essential.
In conclusion, the integration of CATIA into thermodynamics studies offers students a transformative learning experience. It goes beyond traditional theoretical approaches, providing a practical and interactive platform that enhances understanding, sharpens problem-solving skills, and prepares students for the real-world challenges of the engineering profession. Through the application of CATIA, students not only grasp the intricacies of thermodynamics but also develop the skills and mindset necessary for success in their future engineering endeavors.
Conclusion
In summary, the blog post delves into the pivotal role of integrating CATIA, a powerful Computer-Aided Design (CAD) tool, into thermodynamics studies, offering a transformative approach to learning for students in the field of mechanical engineering. The exploration begins with an acknowledgment of CATIA's standing as a comprehensive 3D modeling and simulation software suite, emphasizing its relevance and capabilities in solving problems inherent to thermodynamics. The discussion then progresses to highlight the practical application of CATIA through a step-by-step walkthrough, showcasing how the software can be employed for modeling and analyzing a heat exchanger system. The significance of CATIA lies in its ability to seamlessly integrate into thermodynamics studies, providing a dynamic platform where students can bridge the gap between theoretical concepts and practical applications.
CATIA's 3D modeling capabilities emerge as a cornerstone, allowing students to create realistic representations of thermodynamic systems. The software's parametric design features enable the easy modification of designs, promoting an iterative and adaptable approach crucial for addressing the complexities of thermodynamics. The discussion further underscores CATIA's simulation and analysis tools, emphasizing their role in providing a virtual laboratory where students can experiment with different scenarios, observe system behavior, and optimize designs for efficiency.
The blog post emphasizes the benefits students can derive from incorporating CATIA into their thermodynamics studies. It illuminates how the software enhances students' understanding of theoretical concepts by providing a visual and interactive learning experience. Additionally, CATIA sharpens students' problem-solving skills through practical application and iterative design processes. The virtual simulations within CATIA not only reinforce classroom learning but also prepare students for real-world applications, where the consequences of design choices are critical.
In conclusion, the blog post reiterates the significance of integrating CATIA into thermodynamics studies as a means to empower students with practical skills highly relevant to the modern engineering industry. Encouraging students to explore and apply these tools, the post underscores the competitive edge gained through proficiency in CATIA and emphasizes the software's role in fostering collaborative and interdisciplinary skills. The call to action urges students to embrace CATIA as a valuable ally in their learning journey, leveraging its capabilities to enhance their understanding, refine problem-solving skills, and prepare for the real-world challenges of a fulfilling career in mechanical engineering.