Using ANSYS for Composite Material Design Assignments: A Step-by-Step Approach
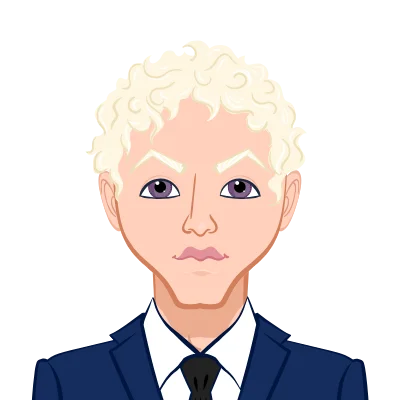
Composite materials play a pivotal role in the realm of mechanical engineering, serving as the backbone for a myriad of innovative solutions and cutting-edge applications. Unlike traditional materials, composites are engineered by combining two or more distinct materials to harness the collective strengths of each, resulting in a material that outperforms its individual components. This amalgamation grants engineers unparalleled flexibility in tailoring material properties, making composites ideal for applications where a combination of strength, durability, and lightweight characteristics is imperative.
The significance of composite materials in mechanical engineering lies in their ability to revolutionize the design and manufacturing processes across various industries. Aerospace, automotive, marine, and sporting goods are just a few sectors benefiting from the unique properties of composites. Their high strength-to-weight ratio, corrosion resistance, and versatility make composites the material of choice for applications demanding optimal performance without compromising on structural integrity.
In the intricate landscape of mechanical engineering, the role of simulation and design tools is paramount, and this is where ANSYS emerges as a formidable ally. ANSYS, a leading finite element analysis (FEA) software, plays a crucial role in simulating and designing composite materials with unmatched precision and efficiency. The software empowers engineers to virtually explore and analyze the behavior of composite structures under diverse conditions, aiding in the optimization of designs before they materialize in the physical realm.
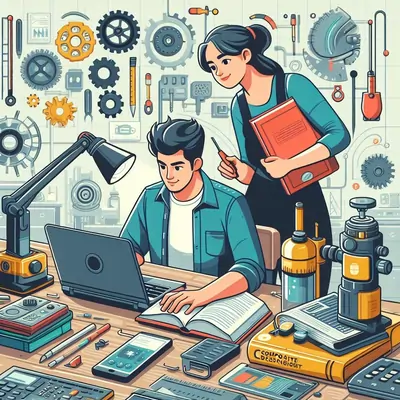
ANSYS facilitates a comprehensive understanding of how composite materials respond to various loads, temperatures, and environmental factors. Engineers can delve into the intricacies of material behavior, ensuring that the designed structures not only meet but exceed performance expectations. The software's robust simulation capabilities allow for the evaluation of different composite layups, providing insights into the most effective combinations of materials and orientations.
Moreover, ANSYS excels in predicting failure modes, fatigue life, and durability of composite structures, enabling engineers to identify potential weak points and refine designs accordingly. This predictive capability is invaluable, as it empowers mechanical engineers to iterate through design alternatives rapidly, ultimately leading to more robust and efficient composite structures.
The seamless integration of ANSYS into the composite material design workflow expedites the development process, reduces prototyping costs, and enhances overall product quality. Engineers can explore a myriad of design options, assess their viability through simulation, and fine-tune the parameters to achieve optimal performance. This iterative process not only accelerates time-to-market but also instills confidence in the reliability of the final product.
In conclusion, the synergy between composite materials and ANSYS is transformative for the field of mechanical engineering. The ability to harness the benefits of composite materials through advanced simulation and design tools like ANSYS not only expands the horizons of engineering possibilities but also contributes to the creation of lighter, stronger, and more efficient structures that define the forefront of technological innovation. As industries continue to push the boundaries of what is achievable, the integration of composite materials and ANSYS remains a cornerstone in shaping the future of mechanical engineering. If individuals require assistance with their ANSYS assignment, exploring the potential of composite materials within this framework can provide valuable insights and practical applications for academic and professional pursuits alike.
Understanding Composite Materials:
Composite materials, in the realm of engineering, refer to materials created by combining two or more distinct constituents with different physical or chemical properties. The resulting composite exhibits a synergy that exploits the strengths of each component while mitigating their individual weaknesses. This strategic combination grants engineer’s unparalleled flexibility in tailoring material properties to meet specific performance criteria. The significance of composite materials in engineering applications lies in their ability to address multifaceted challenges where conventional materials fall short. They are designed to offer a balanced amalgamation of attributes such as high strength, low weight, corrosion resistance, and durability. This makes composites particularly valuable in sectors where a delicate equilibrium between structural integrity and lightweight characteristics is paramount.
In the domain of mechanical engineering, the application of composite materials is widespread, revolutionizing the design and manufacturing processes across various industries. One of the primary advantages of composite materials is their exceptional strength-to-weight ratio. This characteristic is especially crucial in aerospace applications, where reducing weight without compromising structural integrity is a constant pursuit. Aircraft components, such as wings and fuselage sections, benefit significantly from the use of composite materials, contributing to fuel efficiency and overall performance.
Types of composite materials commonly employed in mechanical engineering encompass a diverse range, each tailored to specific requirements. Fiber-reinforced composites, such as carbon fiber reinforced polymers (CFRP) and glass fiber reinforced polymers (GFRP), are extensively used. CFRP, known for its high strength and low weight, finds applications in aircraft components, sports equipment, and automotive structures. GFRP, while less rigid than CFRP, offers excellent impact resistance and is often used in applications such as boat hulls and automotive panels.
Another class of composites is particulate composites, where small particles of one material are dispersed in a matrix of another. Metal matrix composites (MMC), where metallic particles are embedded in a metal matrix, are employed in applications requiring enhanced thermal conductivity, such as heat sinks in electronic devices. Ceramic matrix composites (CMC), combining ceramic fibers with a ceramic matrix, excel in high-temperature environments, making them suitable for components in gas turbines and aerospace applications.
In summary, composite materials stand as a testament to the ingenuity of engineering, providing tailored solutions to a myriad of challenges. Their significance in mechanical engineering is profound, offering a versatile toolkit to engineers seeking to push the boundaries of what is achievable in terms of performance, efficiency, and durability. The ongoing evolution and diversification of composite materials continue to shape the landscape of mechanical engineering, driving innovation and redefining the possibilities in various industrial sectors.
Introduction to ANSYS:
ANSYS is a leading simulation software widely acclaimed for its robust capabilities in engineering simulation and analysis. Developed by ANSYS Inc., the software caters to a diverse range of industries and disciplines, providing engineers and designers with a powerful toolset for virtual prototyping, product development, and performance optimization. ANSYS employs finite element analysis (FEA) and computational fluid dynamics (CFD) techniques, enabling users to simulate and analyze the behavior of structures, materials, and fluid dynamics in virtual environments.
The software's capabilities extend across various domains, including structural mechanics, thermal analysis, electromagnetics, and fluid dynamics. Engineers leverage ANSYS to predict and understand how designs will behave under real-world conditions, allowing for informed decision-making throughout the product development lifecycle. Its user-friendly interface and extensive library of material models make it accessible to both seasoned professionals and those new to simulation, fostering innovation and accelerating the design process.
In the specific context of composite material design, ANSYS plays a pivotal role in advancing engineering practices. The software allows engineers to simulate the complex behavior of composite structures with a high degree of accuracy. ANSYS provides tools to model and analyze the intricate interactions between different layers of composite materials, considering factors such as fiber orientation, stacking sequence, and resin properties. This level of detail is crucial for predicting the performance of composite structures under various loading conditions, including tension, compression, and shear.
One of the key strengths of ANSYS in composite material design lies in its ability to perform advanced analyses, such as failure prediction, fatigue analysis, and optimization. Engineers can explore different layup configurations, material combinations, and manufacturing processes virtually before physically constructing prototypes. This not only saves time and resources but also enhances the overall quality of the final product by identifying potential issues early in the design phase.
Moreover, ANSYS facilitates the exploration of a wide range of composite materials, including but not limited to carbon fiber, glass fiber, and hybrid composites. Engineers can assess the performance of these materials in specific applications, considering factors like thermal conductivity, impact resistance, and overall structural integrity.
In conclusion, ANSYS stands as a cornerstone in the field of simulation and analysis, empowering engineers to push the boundaries of innovation in composite material design. Its comprehensive suite of tools and capabilities allows for in-depth exploration and optimization of composite structures, fostering a more efficient and informed design process. As industries continue to embrace composite materials for their unique properties, the relevance of ANSYS remains paramount in ensuring the successful integration of these materials into real-world engineering applications.
Setting Up Your ANSYS Project:
Setting up a new project in ANSYS for composite material design involves a systematic process to ensure accurate and meaningful simulation results. The initial steps in creating a project lay the foundation for the subsequent analysis.
Firstly, users should launch the ANSYS Workbench, the graphical user interface for managing and launching ANSYS applications. Within Workbench, the project schematic provides a visual representation of the simulation workflow. To initiate a new project, users typically start by selecting the type of analysis they wish to perform. In the context of composite material design, this might involve choosing a structural analysis system, such as "Static Structural" or "Modal."
Once the analysis system is selected, users proceed to define the geometry of the composite structure. Importing CAD models or creating geometry within ANSYS can be accomplished in this step. It is crucial to accurately represent the composite layup, specifying the number of layers, fiber orientations, and material properties for each layer. ANSYS provides tools for creating and manipulating this composite geometry to ensure a realistic representation.
After defining the geometry, users move on to meshing, a critical aspect of the simulation process. Meshing involves dividing the geometry into finite elements, and for composite material simulations, it's essential to generate a mesh that accurately captures the variations in material properties and orientations. Users must pay attention to element size and quality to ensure the mesh accurately represents the complex behavior of composite materials.
The next step involves assigning material properties to the composite layers. ANSYS allows users to choose from a variety of material models suitable for composite materials, considering factors like elastic modulus, Poisson's ratio, and failure criteria. Assigning accurate material properties is crucial for obtaining reliable simulation results.
Boundary conditions and constraints are then applied to simulate real-world loading conditions. Users define how the composite structure interacts with its environment, specifying things like fixed supports, applied forces, and constraints. This step is essential for capturing the actual operating conditions and performance expectations of the composite material in the given application.
Finally, users set up the solution settings, specifying parameters such as solver options, convergence criteria, and output requests. Running the simulation within ANSYS then generates results that can be post-processed to extract valuable information about the structural behavior, stress distribution, and other critical factors.
In summary, setting up a new project in ANSYS for composite material design involves defining geometry, meshing, assigning material properties, applying boundary conditions, and configuring solution settings. The accuracy and reliability of the simulation heavily depend on meticulous inputs and parameters, making it imperative for users to have a thorough understanding of the composite material and its intended application.
Material Selection and Properties:
Choosing appropriate material models for composite materials in ANSYS is a crucial step in ensuring accurate and reliable simulation results. ANSYS provides a variety of material models, and selecting the right one requires a deep understanding of the behavior of composite materials under different conditions.
The first consideration is typically the type of composite material being used. Common types include carbon fiber-reinforced polymers (CFRP), glass fiber-reinforced polymers (GFRP), and hybrid composites. Each material has unique mechanical properties, and ANSYS offers specific material models tailored to simulate the behavior of these composites accurately.
In the case of CFRP, which is renowned for its high strength and stiffness, an appropriate material model might involve selecting a linear or non-linear elastic model. Users can further refine the model by specifying parameters like Young's modulus, Poisson's ratio, and ultimate strength based on experimental data or manufacturer specifications.
For GFRP, which exhibits different mechanical characteristics than CFRP, a different set of material models may be appropriate. ANSYS provides options for orthotropic material models, allowing users to define different material properties in different directions. This is crucial for capturing the anisotropic nature of composite materials, where the mechanical properties vary with fiber orientation.
In scenarios involving complex hybrid composites, ANSYS allows users to create custom material models by combining the characteristics of individual materials. This flexibility is particularly advantageous when dealing with innovative material combinations or proprietary composites.
The importance of accurate material properties in simulation cannot be overstated. Composite materials are prized for their ability to deliver specific combinations of strength, stiffness, and lightweight properties, and the simulation's effectiveness hinges on replicating these material behaviors. Inaccurate material properties can lead to erroneous predictions, potentially resulting in suboptimal designs or, in worst cases, structural failures.
Accurate material properties enable the simulation to reflect real-world conditions, allowing engineers to make informed decisions about a composite structure's performance. This is especially critical in applications where safety, reliability, and efficiency are paramount, such as aerospace or automotive engineering. Simulation results heavily influence design iterations, and precise material models ensure that the virtual prototypes closely match the physical behavior of the actual composite components.
Furthermore, accurate material properties are essential for predicting failure modes, fatigue life, and other critical aspects of composite behavior. Engineers can use the simulation results to identify potential weak points in the design, enabling them to make informed decisions to enhance the structure's overall reliability and longevity.
In conclusion, the choice of appropriate material models in ANSYS for composite materials is a nuanced process that demands a deep understanding of the specific composite being simulated. Accurate material properties are the linchpin of effective simulations, influencing design decisions and ensuring that the virtual prototypes align closely with the real-world behavior of composite materials. This accuracy is indispensable for advancing engineering designs, optimizing performance, and ensuring the safety and reliability of composite structures in diverse applications.
Creating the Composite Model:
Creating a composite material model in ANSYS involves a systematic and meticulous process, critical for accurate simulations in mechanical engineering. The initial step is to open ANSYS Workbench, select the appropriate analysis system, and define the geometry of the composite structure. Whether importing or creating within ANSYS, ensure that the model reflects the real-world composite layup, specifying the number of layers, fiber orientations, and stacking sequence. Mesh generation follows, requiring careful consideration of element size and quality, with a preference for hexahedral elements to enhance accuracy.
Assigning material properties is a pivotal step. Choose the material model based on the composite type, such as orthotropic for fiber-reinforced composites. Incorporate parameters like Young's modulus, Poisson's ratio, and shear modulus for each material direction. It is crucial to use accurate material data obtained from testing or reliable sources to ensure the fidelity of the simulation.
Layer stacking is essential for representing the anisotropic nature of composites. Organize layers in the Details view of the geometry, specifying materials and fiber orientations. Consistency with the physical layup is key for meaningful results. Proper boundary conditions must be applied to simulate real-world loading conditions. Constraints and forces need careful consideration, aligning with the expected behavior of the composite structure under specific scenarios.
With the geometry, material properties, and boundary conditions set, the next step is the solution setup. Configure solver options, convergence criteria, and output requests. Regular convergence checks during the simulation are crucial. Refining the mesh or adjusting solution settings based on the convergence results improves accuracy, particularly in critical regions.
Upon completing the setup, initiate the simulation run and monitor its progress. Post-processing results reveal crucial insights into stress distribution, deformation, and potential failure modes. Conduct sensitivity analyses by varying material properties or layup configurations to understand their impact on results.
Considerations and best practices are integral to this process. Material testing for validation, when possible, enhances confidence in the chosen material models. Regularly documenting the material model, layer stacking, and simulation setup aids transparency and collaboration. Additionally, sensitivity analyses provide insights into the model's robustness.
In summary, the step-by-step process of creating a composite material model in ANSYS demands a holistic understanding of the material and meticulous attention to detail. Accurate representation of the composite's physical characteristics, thoughtful meshing, and precise material properties contribute to the reliability of simulations. Continuous refinement based on convergence checks and sensitivity analyses enhances the model's accuracy, making it a powerful tool for optimizing designs in mechanical engineering.
Meshing and Boundary Conditions:
Meshing plays a pivotal role in simulating composite materials within ANSYS, significantly influencing the accuracy and reliability of the simulation results. Composite materials often exhibit intricate and heterogeneous structures, and an appropriately refined mesh is essential to capture these complexities. The mesh serves as a discretized representation of the composite, dividing it into smaller elements for analysis. For composite materials, achieving an optimal mesh involves balancing element size and density, particularly in regions with varying material properties or abrupt changes in fiber orientations.
The importance of meshing lies in its impact on the fidelity of stress and strain distribution throughout the composite structure. An inadequate mesh may lead to inaccuracies in predicting material responses, especially in areas with high stress concentrations or where material properties change abruptly. Consequently, mesh refinement is crucial to capture localized phenomena such as stress concentrations around holes or interfaces between different composite layers. Additionally, an optimized mesh ensures that the simulation converges more efficiently, providing reliable insights into the behavior of the composite material under various loading conditions.
When setting up boundary conditions for a composite material simulation, it is essential to mirror real-world scenarios to obtain meaningful results. Properly defined boundary conditions mimic the external influences and constraints that the composite structure would experience in its operational environment. This involves restraining degrees of freedom at fixed supports, applying realistic loads, and incorporating any constraints that replicate the actual physical connections.
Guidelines for setting up boundary conditions include a comprehensive understanding of the loading conditions specific to the application. Ensure that applied forces and constraints align with the expected behavior of the composite structure. For instance, if simulating an aerospace component, consider the aerodynamic forces and thermal loads it would encounter in-flight. For automotive applications, factors like impact and vibration become crucial.
In the case of composite materials, which are often used in lightweight structures, the boundary conditions should account for the material's unique characteristics, such as anisotropy and orthotropy. Applying loads and constraints in alignment with the composite's fiber orientations is essential for accurately predicting its response to external forces.
Moreover, it is recommended to conduct sensitivity analyses on boundary conditions to assess how variations may influence the simulation results. This iterative process ensures that the chosen boundary conditions are not only realistic but also robust, providing a comprehensive understanding of the composite material's performance under different scenarios.
In summary, meshing and boundary conditions are integral components in simulating composite materials effectively. A well-refined mesh captures the intricacies of the composite structure, while realistic boundary conditions mirror actual operating conditions, ensuring that simulation results align closely with real-world behavior. These considerations are fundamental for engineers seeking to gain accurate insights into the performance of composite materials in diverse engineering applications.
Running the Simulation:
Running a simulation in ANSYS involves a series of steps that culminate in obtaining valuable insights into the behavior of the simulated system, in this case, a composite material structure. After setting up the geometry, mesh, material properties, and boundary conditions, users proceed to the solution phase. Clicking "Solve" initiates the simulation, and ANSYS utilizes its powerful solvers to numerically analyze the behavior of the composite structure under the specified conditions.
During the simulation run, common challenges may arise, necessitating troubleshooting to ensure the accuracy and convergence of results. One prevalent challenge is insufficient convergence, indicated by the solution failing to stabilize or diverging. To address this, users can refine the mesh in critical regions, adjust convergence criteria, or consider changing solver settings. Monitoring convergence plots and examining convergence metrics help identify problematic areas.
Another challenge involves excessive computational time, particularly in simulations with intricate geometries or extensive meshes. In such cases, users can employ parallel processing to distribute the computational load across multiple processors, optimizing simulation efficiency. Additionally, refining the mesh selectively in areas of interest can help strike a balance between accuracy and computational time.
Convergence issues may also arise when dealing with non-linearities, such as large deformations or material nonlinearities in composite simulations. Adjusting the solution method, employing adaptive meshing, or exploring more advanced solver options like arc-length control can enhance convergence in nonlinear analyses.
Insufficient memory allocation is a common issue, especially with large models. Users can address this by optimizing mesh density, employing remote solving on high-performance computing resources, or upgrading hardware configurations.
Furthermore, result interpretation is critical. Post-processing tools in ANSYS allow users to visualize and extract key information from the simulation results. Common challenges here include misinterpretation of graphical outputs or difficulty in extracting specific data. ANSYS provides robust post-processing capabilities, and users should familiarize themselves with these tools and consult documentation or forums for troubleshooting advice.
In conclusion, running a simulation in ANSYS involves initiating the solver, monitoring convergence, and interpreting results. Common challenges, such as convergence issues, excessive computational time, and memory constraints, can be addressed through careful adjustment of simulation settings, mesh refinement, and utilization of advanced solver options. Troubleshooting these challenges is an integral part of the simulation process, ensuring that engineers obtain accurate and reliable insights into the behavior of composite materials.
Analyzing Results:
Interpreting and analyzing results obtained from an ANSYS simulation is a crucial phase that unveils insights into the structural behavior of a composite material. ANSYS provides powerful post-processing tools for visualizing and extracting meaningful data. Key aspects to consider include stress distribution, deformation, and potential failure modes. Color contour plots and deformation animations help visualize stress concentrations and identify critical areas where the composite may experience high loads or strains.
When analyzing stress results, it's essential to examine not only the magnitude of stresses but also their distribution across different layers and orientations within the composite. This aids in understanding how the material responds to specific loading conditions and provides valuable information for optimizing the design.
Deformation plots reveal how the composite structure physically responds to applied loads. These visualizations help identify areas of excessive deformation or deformation gradients, guiding engineers in refining the design to meet performance criteria. Additionally, animations of the deformation process provide a dynamic understanding of the structural response.
The significance of these results in the context of composite material design assignments is profound. Engineers can use stress and deformation data to validate design assumptions, refine material models, and optimize composite layups for enhanced structural performance. By identifying areas of high stress or deformation, engineers can iteratively improve the design, adjusting factors such as material orientation, layer stacking, or thickness to meet safety and performance standards.
Moreover, analyzing failure criteria, such as von Mises stress or strain-based criteria, is crucial for predicting potential failure modes. Engineers can use this information to implement design changes that enhance the composite's resilience against factors like fatigue, impact, or thermal cycling. The insights gained from ANSYS simulations empower designers to make informed decisions, ensuring that the final composite structure not only meets but exceeds the performance expectations outlined in the design assignment.
In summary, interpreting ANSYS simulation results provides engineers with a comprehensive understanding of how composite materials behave under various conditions. The significance lies in the actionable insights derived from stress, deformation, and failure analyses, enabling iterative design improvements and ultimately contributing to the successful realization of optimized and reliable composite structures in diverse engineering applications.
Conclusion:
In the blog "Using ANSYS for Composite Material Design Assignments: A Step-by-Step Approach," we explored the intricate process of employing ANSYS, a leading simulation software, for the effective design and analysis of composite materials in mechanical engineering. The key points highlighted the significance of composite materials in engineering applications, their types commonly used in mechanical engineering, the overview of ANSYS software, and its relevance in simulating and designing composite materials. The blog delved into guiding readers through the process of setting up a new project in ANSYS for composite material design, emphasizing the crucial steps involving geometry definition, mesh generation, material property assignment, layer stacking, boundary conditions, solution setup, and simulation runs. The importance of accurate material models for composite materials in ANSYS was underscored, along with considerations for choosing appropriate models tailored to the specific type of composite. Furthermore, the blog stressed the critical role of accurate material properties in simulations, influencing design decisions and ensuring the reliability of virtual prototypes. Additionally, the walkthrough on creating a composite material model in ANSYS elucidated steps such as defining geometry, mesh generation, material assignment, layer stacking, boundary conditions, and solution setup. Specific considerations and best practices, including material testing, convergence checks, sensitivity analysis, and documentation, were discussed to enhance the reliability of the simulation results. The blog concluded by encouraging readers to apply the step-by-step approach outlined in their own composite material design assignments, emphasizing the software's capability to expedite the design process, reduce prototyping costs, and enhance overall product quality. By leveraging ANSYS, engineers can simulate and analyze composite structures with a high degree of accuracy, leading to informed design decisions and optimized performance. The stepwise guide serves as a valuable resource for individuals seeking to integrate simulation tools effectively into their workflow, providing a solid foundation for tackling the intricacies of composite material design in diverse engineering applications.