Multiphysics Simulations in ANSYS: Combining Different Physical Models!
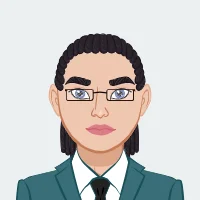
In the dynamic realm of mechanical engineering, the application of multiphysics simulations stands as a transformative force, pushing the boundaries of traditional analysis methodologies. Multiphysics simulations involve the concurrent study and solution of multiple interconnected physical phenomena within a single model. In the intricate landscape of mechanical systems, where diverse forces and interactions coexist, this approach offers unparalleled insights into the complex behavior of structures, fluids, and thermal processes. Whether you require help with your Ansys assignment or are exploring the capabilities of multiphysics simulations in mechanical engineering, embracing this approach can provide valuable insights and solutions to complex engineering problems.
The significance of multiphysics simulations in mechanical engineering cannot be overstated. Traditionally, engineers often approached problems in isolation, focusing on a singular aspect of a system, be it structural mechanics, fluid dynamics, or heat transfer. However, real-world scenarios rarely adhere to such compartmentalization. Mechanical systems, ranging from automotive components to industrial machinery, are subject to a myriad of interconnected physical phenomena. The ability to analyze and understand the interplay between these phenomena is paramount for engineers striving to design robust and efficient systems.
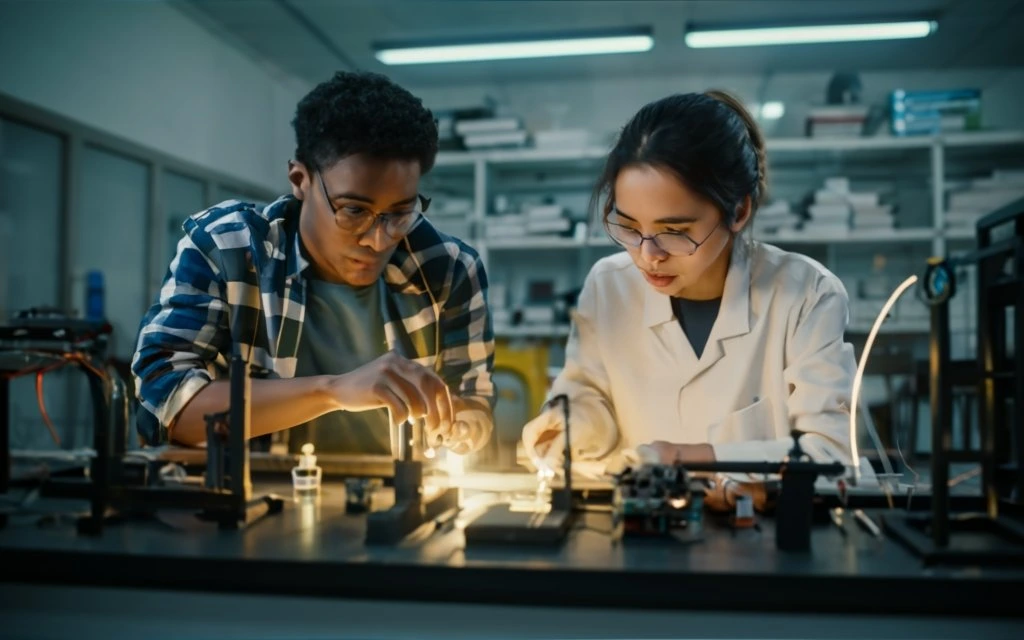
By combining different physical models, multiphysics simulations enable a more comprehensive analysis that mirrors the complexity of actual operating conditions. Take, for instance, the design of a heat exchanger in an industrial setting. Traditional analysis might assess the structural integrity of the exchanger's components separately from its thermal efficiency. However, in reality, the thermal performance is intimately linked to the structural behavior. Multiphysics simulations allow engineers to study the thermal and structural aspects concurrently, providing a holistic understanding of the system's performance under diverse operating conditions.
The power of multiphysics simulations becomes particularly evident when using advanced simulation software such as ANSYS. ANSYS, a renowned finite element analysis tool, offers a robust platform for integrating various physical models seamlessly. Its capabilities span structural mechanics, fluid dynamics, electromagnetics, and thermal analysis. This versatility empowers engineers to tackle multifaceted engineering challenges without the need for separate simulations for each aspect.
Case studies abound wherein the application of multiphysics simulations has yielded groundbreaking results. Consider the development of an automotive component like a brake disc. Multiphysics simulations enable engineers to assess not only the structural integrity of the disc under various mechanical loads but also its thermal behavior during intense braking conditions. This integrated approach ensures that the final design not only withstands mechanical stress but also efficiently dissipates heat, preventing potential failure under extreme operational scenarios.
The benefits of multiphysics simulations extend beyond the realms of enhanced accuracy and efficiency. They provide engineers with a deeper understanding of the intricate relationships between different physical phenomena, facilitating the discovery of unforeseen opportunities for optimization. The approach also contributes to significant time and cost savings by streamlining the design and testing processes, ultimately leading to more robust and reliable engineering solutions.
In conclusion, multiphysics simulations in mechanical engineering represent a paradigm shift, ushering in an era of comprehensive analysis and design. The amalgamation of different physical models through advanced simulation tools like ANSYS empowers engineers to explore the intricate interdependencies within mechanical systems. As we delve into the subsequent sections, we will unravel the nuances of multiphysics simulations, exploring their applications, benefits, and the challenges they present in the pursuit of engineering excellence.
Understanding Multiphysics Simulations:
Multiphysics simulations represent a sophisticated approach in engineering analysis, involving the simultaneous consideration and solution of multiple interconnected physical phenomena. This methodology recognizes the intricate interplay of various scientific principles, allowing for a more holistic understanding of complex real-world scenarios. At the core of multiphysics simulations lies the integration of different physics domains, such as fluid dynamics, structural mechanics, and heat transfer, among others.
Fluid dynamics, a key aspect of multiphysics simulations, deals with the behavior of fluids (liquids and gases) and their interactions with solid structures. For instance, in aeronautical engineering, understanding how airflow influences the structural integrity of an aircraft wing is crucial. Multiphysics simulations enable the coupling of fluid dynamics and structural mechanics to analyze the impact of aerodynamic forces on the structural components, offering engineers a comprehensive view of the system's performance.
Structural mechanics, another pivotal domain, focuses on the study of how materials respond to various forces. In combination with other physics models, structural mechanics simulations can provide insights into the dynamic behavior of structures under different environmental conditions. This is particularly valuable in civil engineering, where structures must withstand diverse loads, such as wind, seismic activity, and thermal expansion.
Heat transfer, a fundamental aspect of many engineering systems, involves the study of the exchange of thermal energy between different components. By combining heat transfer models with other physics simulations, engineers can explore scenarios like the thermal behavior of electronic devices or the impact of temperature changes on material properties. This multiphysics approach ensures a more accurate representation of real-world conditions, leading to enhanced system design and performance predictions.
The beauty of multiphysics simulations lies in their ability to model the intricate coupling between these diverse physical phenomena. For instance, consider a scenario where fluid dynamics, structural mechanics, and heat transfer are interconnected. In the automotive industry, multiphysics simulations can be employed to analyze the cooling system of an internal combustion engine. The simulation would involve understanding how coolant flows through the engine (fluid dynamics), its interaction with engine components (structural mechanics), and the heat dissipation process (heat transfer). This holistic approach enables engineers to optimize the cooling system for maximum efficiency and reliability.
In conclusion, multiphysics simulations in ANSYS provide a powerful tool for engineers and researchers to unravel the complexities of real-world problems by integrating diverse physical models. The simultaneous consideration of fluid dynamics, structural mechanics, heat transfer, and other physics domains allows for a comprehensive analysis that mirrors the intricacies of actual systems. As technology advances, the application of multiphysics simulations continues to expand, offering unparalleled insights into the behavior of complex engineering systems and paving the way for innovative solutions in the field of mechanical engineering.
ANSYS for Multiphysics Simulations:
ANSYS, a widely acclaimed software suite, stands out as a premier choice for multiphysics simulations in the realm of mechanical engineering. Its popularity stems from a robust set of capabilities that allows engineers and researchers to seamlessly integrate and analyze diverse physical models within a unified framework. The comprehensive nature of ANSYS enables engineers to tackle complex problems by combining different aspects of physics, providing a more realistic representation of real-world scenarios.
One key strength of ANSYS lies in its ability to handle a wide array of physical phenomena. Whether dealing with fluid dynamics, structural mechanics, heat transfer, electromagnetic fields, or other intricate interactions, ANSYS provides a versatile platform. This versatility allows engineers to create coupled simulations, where multiple physics domains are integrated to study the interactions between them. For instance, simulating the thermal effects on a structural component immersed in a fluid can be efficiently achieved through ANSYS' multiphysics capabilities.
The software's meshing capabilities further contribute to its popularity in multiphysics simulations. ANSYS offers advanced meshing algorithms that enable engineers to generate high-quality meshes for complex geometries. This is crucial when dealing with simulations involving multiple physical models, as an accurate representation of the geometry is fundamental to the reliability of the results. The adaptability of ANSYS in handling intricate geometries ensures that simulations closely mimic real-world conditions.
Accuracy is paramount in engineering simulations, and ANSYS excels in this aspect. The software employs sophisticated numerical methods and solvers to ensure precise results. Engineers can trust ANSYS to deliver accurate predictions, facilitating better decision-making in the design and analysis phases. This accuracy is particularly valuable in multiphysics simulations, where the interaction of different physical models necessitates precise calculations to capture the nuances of complex systems.
Efficiency is another hallmark of ANSYS that contributes to its widespread adoption for multiphysics simulations. The software optimizes computational resources through parallel processing, allowing users to harness the power of high-performance computing for faster simulations. This efficiency is especially crucial in the context of multiphysics, where simulations involving multiple physics domains can be computationally demanding. ANSYS' ability to streamline these simulations ensures that engineers can obtain results in a timely manner, accelerating the overall product development cycle.
Furthermore, ANSYS provides a user-friendly interface, making it accessible to both seasoned engineers and students alike. The intuitive interface simplifies the setup of multiphysics simulations, reducing the learning curve for users who may be dealing with complex coupled systems for the first time. This accessibility enhances the adoption of ANSYS across educational institutions and industries, fostering a community of users with diverse levels of expertise.
In conclusion, ANSYS stands as a preeminent choice for multiphysics simulations due to its versatility, meshing capabilities, accuracy, efficiency, and user-friendly interface. By seamlessly integrating diverse physical models, ANSYS empowers engineers and researchers to tackle complex engineering challenges, providing a comprehensive and reliable platform for the analysis of interconnected physical phenomena. As the field of mechanical engineering continues to advance, ANSYS remains at the forefront, facilitating the exploration and understanding of intricate multiphysics systems.
Benefits of Multiphysics Simulations:
Multiphysics simulations have emerged as a powerful tool in the realm of mechanical engineering assignments, offering a myriad of advantages that significantly contribute to the field's advancement. One of the primary benefits is the heightened accuracy achieved through the integration of multiple physical models. Traditional simulations often rely on isolated analyses, neglecting the intricate interactions between different aspects of a system. Multiphysics simulations, however, enable engineers to capture the synergies between diverse phenomena, resulting in more realistic and precise predictions of system behavior.
A key advantage lies in the enhanced understanding of system behavior facilitated by multiphysics simulations. By simultaneously considering various physical aspects, engineers gain a holistic view of how different components interact within a system. This comprehensive insight is invaluable for accurately predicting and optimizing complex engineering systems where the interplay of multiple factors is crucial. Whether it's fluid-structure interaction, thermal-electrical coupling, or other coupled phenomena, multiphysics simulations provide a nuanced understanding that goes beyond the limitations of single-physics analyses.
Time and cost savings stand out as another compelling benefit of employing multiphysics simulations. In traditional approaches, separate simulations for each physical model are time-consuming and can lead to a fragmented understanding of the overall system. Multiphysics simulations streamline this process by integrating all relevant physics into a unified analysis, reducing the need for sequential, disjointed simulations. This not only expedites the engineering design and optimization processes but also translates into substantial cost reductions, making it a practical and efficient choice for engineers working within constraints of time and budget.
Furthermore, multiphysics simulations facilitate innovation and optimization by uncovering unforeseen interactions and dependencies within a system. Engineers can explore a wider design space, identifying optimal configurations and refining their designs based on a comprehensive understanding of the coupled physical phenomena. This iterative process of refinement is pivotal in achieving high-performance engineering solutions.
In conclusion, the benefits of multiphysics simulations in mechanical engineering assignments are multifaceted. From heightened accuracy and a deeper understanding of system behavior to substantial time and cost savings, the adoption of multiphysics simulations represents a paradigm shift in how engineers approach complex problems. As technology advances, the integration of diverse physical models through tools like ANSYS continues to empower engineers, enabling them to tackle intricate challenges with unprecedented precision and efficiency.
Challenges and Considerations:
Multiphysics simulations in ANSYS offer a powerful means of analyzing complex mechanical engineering problems by concurrently solving multiple physical phenomena. However, this approach is not without its challenges, and practitioners must navigate issues such as increased computational requirements and potential convergence issues.
The foremost challenge lies in the heightened demand for computational resources. Combining different physical models requires solving a system of coupled equations, significantly increasing the complexity of simulations. As a result, the computational demands escalate, necessitating robust hardware configurations and longer processing times. This challenge is particularly pronounced when dealing with intricate systems or when aiming for high-fidelity simulations.
Addressing the computational challenge involves a combination of technological and methodological strategies. Investing in high-performance computing (HPC) infrastructure can enhance simulation efficiency by distributing the computational load across multiple processors. Additionally, employing parallel processing techniques and optimizing solver settings within ANSYS can contribute to more streamlined simulations, mitigating the impact of increased computational requirements.
Convergence issues present another hurdle in multiphysics simulations. The simultaneous solution of diverse physical models can lead to difficulties in achieving convergence, where the solution stabilizes and reaches a steady state. Nonlinearities, coupled physics interactions, and poorly conditioned models can contribute to convergence challenges, leading to simulation divergence or slow convergence rates.
To address convergence issues effectively, a meticulous approach to model setup and solver settings is imperative. Careful consideration of boundary conditions, mesh quality, and material properties can enhance convergence behavior. Additionally, adopting advanced solver techniques, such as adaptive mesh refinement or utilizing more robust solvers within ANSYS, can contribute to overcoming convergence challenges. It is crucial for engineers and students engaged in multiphysics simulations to continually monitor convergence behavior, diagnose convergence failures, and adjust simulation parameters accordingly.
Furthermore, iterative refinement of the simulation setup, including adjusting solution tolerances and convergence criteria, can significantly improve convergence rates. ANSYS provides a range of diagnostic tools and convergence monitoring features that aid users in identifying and rectifying convergence issues during the simulation process.
In conclusion, while multiphysics simulations in ANSYS offer a comprehensive approach to mechanical engineering problems, practitioners must navigate challenges such as increased computational demands and convergence issues. By leveraging advanced computational resources, employing optimization strategies, and maintaining a meticulous approach to model setup, engineers can effectively address these challenges, unlocking the full potential of multiphysics simulations for insightful and accurate analyses in mechanical engineering assignments.
Conclusion:
In conclusion, the exploration of Multiphysics Simulations in ANSYS unveils a transformative landscape in the realm of mechanical engineering. This blog delved into the essence of multiphysics simulations, elucidating their pivotal role in comprehensively addressing the intricate challenges posed by diverse physical phenomena. By concurrently solving multiple physics-based equations, ANSYS emerges as a potent tool, offering unparalleled capabilities in rendering precise and efficient simulations.
The significance of this approach becomes manifest in its ability to encapsulate a holistic understanding of complex systems. As highlighted, the simultaneous integration of fluid dynamics, structural mechanics, heat transfer, and other physical models within ANSYS fosters a multidimensional comprehension of real-world scenarios. This not only enhances the accuracy of analyses but also affords engineers and researchers a deeper insight into the intricate interplay of various factors influencing mechanical systems.
Real-world case studies underscored the practical applications of multiphysics simulations in ANSYS, showcasing instances where this approach has proven instrumental in surmounting challenges. From optimizing designs to predicting system behaviors with a higher degree of fidelity, the versatility of ANSYS in handling diverse physical models is instrumental in advancing mechanical engineering research. These case studies stand as testimonies to the efficacy of multiphysics simulations in solving complex engineering problems.
The benefits reaped from embracing multiphysics simulations are manifold. Improved accuracy, a nuanced understanding of system dynamics, and the potential for significant time and cost savings underscore the transformative impact of this methodology. As the demand for more sophisticated and precise engineering solutions continues to rise, mastering the art of multiphysics simulations becomes imperative for aspiring mechanical engineers and researchers.
However, with innovation comes challenges. This blog acknowledged the computational demands and potential convergence issues associated with multiphysics simulations. By recognizing these hurdles, engineers can proactively address them, fostering a more seamless integration of this powerful tool into their workflow.
In essence, the exploration of Multiphysics Simulations in ANSYS is not merely an academic pursuit; it is a gateway to unlocking new dimensions in mechanical engineering research and problem-solving. As we navigate the complex landscape of modern engineering challenges, the integration of diverse physical models through ANSYS stands as a beacon, guiding us toward more robust, accurate, and efficient solutions. Embracing multiphysics simulations is not just an advancement; it is a paradigm shift, heralding a new era in the way we approach and solve mechanical engineering problems.