Heat Exchanger Design and Analysis Assignment: Thermodynamics in Practice
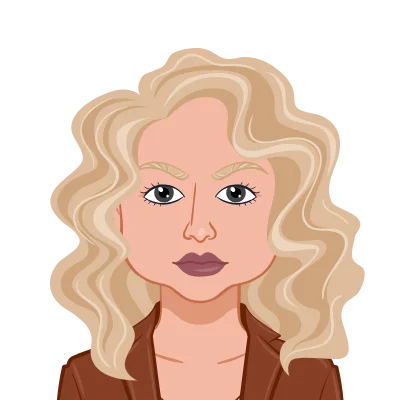
In the intricate tapestry of mechanical engineering, the domain of thermodynamics emerges as a cornerstone, weaving theory and application seamlessly together. At the heart of this discipline lies a captivating and challenging subject – the design and analysis of heat exchangers. In the ever-evolving landscape of industrial processes, where efficiency and energy conservation are paramount, a profound understanding of heat exchanger principles is not just academic but a practical necessity. The journey into the world of "Heat Exchanger Design and Analysis Assignment: Thermodynamics in Practice" beckons us to explore the nuanced interplay between theoretical knowledge and its real-world applications.
To embark on this exploration, it is crucial to grasp the essence of heat exchangers themselves. These devices, omnipresent in various mechanical systems, act as conduits for the transfer of thermal energy between two or more fluids. The significance of this process cannot be overstated, as it underpins the efficiency and performance of a myriad of industrial applications, from power generation to chemical processing. The assignment at hand, focusing on heat exchanger design and analysis, takes us deep into the intricate workings of these devices, where thermodynamics principles come alive in a practical, tangible form.
Diving into the fundamentals, we encounter a diverse array of heat exchangers, each tailored for specific applications. From the classic shell-and-tube designs to the modern plate and fined-tube configurations, each type brings its unique advantages and challenges to the table. This diversity, a testament to the versatility of mechanical engineering, prompts students to not only understand the theoretical underpinnings but also to appreciate the nuanced selection of heat exchangers based on the demands of a particular system.
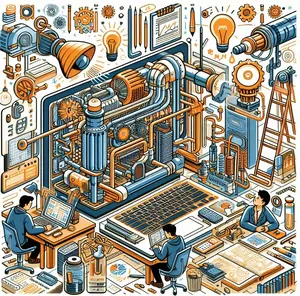
Moving beyond the typologies, an exploration of the key components and working principles of heat exchangers is essential. The intricacies of heat transfer coefficients, fouling factors, and overall heat transfer equations become the building blocks for any aspiring mechanical engineer. As we navigate through these foundational concepts, we begin to see how the theoretical aspects of thermodynamics manifest in the physical design of heat exchangers, shaping the landscape of energy-efficient systems.
With this groundwork in place, the assignment naturally progresses to the design phase, where engineers must synthesize theory and application. Thermal considerations take center stage, demanding an intricate dance of calculations and decisions. The determination of heat exchanger size, material selection, and an understanding of fluid properties become the guiding lights in this creative process. It is here that the true essence of thermodynamics in practice is unveiled – the art of optimizing heat transfer for maximum efficiency.
Fluid flow and pressure drop considerations further deepen the analysis, emphasizing the need for engineers to master the dynamics of fluid behavior. This stage of the assignment pushes students to not only consider the theoretical aspects of fluid flow but to apply this knowledge to create heat exchanger designs that minimize pressure drops and enhance overall performance.
As the assignment transitions from design to analysis, the focus shifts to evaluating the performance of the heat exchanger under various operating conditions, aiming to solve your Thermodynamics assignment. This phase is a testament to the practicality of the theoretical knowledge acquired earlier. Performance metrics such as effectiveness, temperature profiles, and log mean temperature difference (LMTD) become the benchmarks for assessing the efficiency of the heat exchanger design. Real-world case studies further illuminate the practical implications of these analyses, grounding the theoretical knowledge in the context of actual industrial applications.
In conclusion, the journey into the realm of "Heat Exchanger Design and Analysis Assignment: Thermodynamics in Practice" encapsulates the essence of mechanical engineering education – the seamless integration of theoretical understanding and hands-on application. As students and educators alike embark on this intellectual voyage, they contribute to the ongoing narrative of innovation and excellence in the dynamic world of mechanical engineering. The allure of heat exchangers, intricately designed and meticulously analyzed, serves as a beacon guiding the next generation of mechanical engineers toward a future where efficiency, sustainability, and ingenuity converge.
Understanding the Basics:
Understanding the basics of heat exchanger design and analysis is foundational for any student venturing into the intricate realm of mechanical engineering. At its core, a heat exchanger is a device designed to transfer thermal energy between two or more fluids, ensuring the efficient operation of diverse industrial processes. The significance of heat exchangers lies in their role as conduits for heat transfer, a fundamental process in various applications ranging from power generation to chemical manufacturing.
To comprehend the intricacies of heat exchangers, it is imperative to delve into the different types that cater to specific needs. The classic shell-and-tube heat exchangers, known for their robustness and versatility, coexist with modern counterparts like plate and fined-tube configurations, each offering unique advantages. Understanding the distinctions between these types lays the groundwork for students to navigate the diversity of heat exchangers and make informed decisions based on the requirements of a given system.
Moving beyond typologies, an exploration of the key components and working principles of heat exchangers becomes paramount. Concepts such as heat transfer coefficients, fouling factors, and overall heat transfer equations form the bedrock of this understanding. Heat exchanger components, such as tubes, shells, and baffles, come to life as students grasp their roles in facilitating efficient heat exchange. This phase of learning not only fosters a theoretical comprehension of heat exchanger dynamics but also underscores the practical considerations that engineers face in the design and implementation of these devices.
As students' progress in their studies, the complexities of thermal design come to the forefront. Thermal design involves determining the size of the heat exchanger, selecting appropriate materials, and considering fluid properties. This phase of the educational journey requires students to apply theoretical knowledge to real-world scenarios, emphasizing the delicate balance between maximizing heat transfer and minimizing energy losses. The intricacies of thermal design are where the theoretical underpinnings of thermodynamics come alive, as students grapple with the challenges posed by varying operating conditions and system requirements.
The subsequent step in comprehending the basics involves fluid flow and pressure drop considerations. Here, students delve into the realm of fluid dynamics, understanding how fluid behavior impacts the overall performance of a heat exchanger. The analysis of pressure drops, and the optimization of fluid flow patterns become integral elements in designing heat exchangers that not only facilitate efficient heat transfer but also operate with minimal energy consumption.
In summary, understanding the basics of heat exchanger design and analysis constitutes a fundamental pillar in the education of mechanical engineers. From grasping the diversity of heat exchanger types to navigating the intricacies of key components and working principles, students embark on a journey that blends theoretical knowledge with practical application. As they delve into thermal design and fluid dynamics, they lay the groundwork for mastering the art of optimizing heat transfer—an indispensable skill in the dynamic and evolving landscape of mechanical engineering.
Types of Heat Exchangers:
In the diverse landscape of heat exchanger applications, various types of these devices have been engineered to cater to specific thermal requirements across different industries. One prominent category is the shell-and-tube heat exchanger, renowned for its versatility and widespread use. Comprising a shell (or casing) housing a bundle of tubes, this design facilitates efficient heat transfer through the exchange of fluids—typically one flowing through the tubes and the other surrounding the outside of the tubes within the shell. The robust construction of shell-and-tube heat exchangers makes them suitable for a myriad of applications, from heating and cooling processes in chemical plants to refrigeration systems in HVAC applications.
Plate heat exchangers represent another significant category, characterized by their compact and space-efficient designs. In this configuration, thin plates with intricate patterns facilitate heat exchange between two fluids. The advantage of plate heat exchangers lies in their high thermal efficiency and suitability for applications with space constraints, such as in the food and beverage industry or automotive cooling systems.
Finned-tube heat exchangers, on the other hand, incorporate extended surfaces, or fins, on the tubes to enhance heat transfer. These fins increase the surface area available for heat exchange, making them particularly effective in applications where compactness and efficiency are critical, such as air conditioning systems or automotive radiators.
Beyond these common types, there are specialized heat exchangers designed for specific purposes. For instance, regenerative heat exchangers operate by cyclically storing and releasing thermal energy, making them suitable for applications requiring high temperature differentials. Additionally, air-cooled heat exchangers are employed in situations where water availability is limited or impractical, using ambient air to dissipate heat.
Understanding the distinctions between these types of heat exchangers is paramount for mechanical engineering students. It equips them to select the most suitable design for a given application, considering factors such as fluid properties, operating conditions, and space constraints. The ability to navigate the diverse landscape of heat exchanger types enhances the engineer's toolkit, allowing for optimal solutions to the complex heat transfer challenges inherent in various industrial processes.
Key Components and Working Principles:
The efficiency and functionality of heat exchangers hinge on a nuanced understanding of their key components and underlying working principles. At the core of these devices are tubes, shells, baffles, and headers, collectively forming the structural framework that facilitates the exchange of thermal energy between fluids. Tubes, often arranged in bundles within a shell, act as conduits for one of the fluids involved in the heat exchange process. The shell encapsulates the tube bundle, creating a containment structure and guiding the flow of the second fluid. Baffles, strategically placed within the shell, enhance heat transfer by promoting turbulence and preventing undesirable fluid bypass. Headers, serving as inlet and outlet points, facilitate the entry and exit of fluids from the heat exchanger, allowing for a controlled flow.
The working principles governing heat exchangers are deeply rooted in fundamental concepts of thermodynamics and fluid mechanics. Heat transfer coefficients, essential parameters in the design, quantify the effectiveness of heat exchange between the fluids. Understanding fouling factors is critical, as they account for the gradual accumulation of deposits on heat exchanger surfaces, affecting performance over time. The overall heat transfer equation, incorporating factors like the log mean temperature difference (LMTD), provides a comprehensive tool for engineers to assess and optimize heat exchanger efficiency.
In practice, the success of a heat exchanger hinges on the intricate dance between these components and principles. Fluid properties, flow rates, and temperature differentials play pivotal roles in determining the device's overall performance. Engineers must navigate the delicate balance between maximizing heat transfer rates and minimizing pressure drops, ensuring that the design aligns with the specific requirements of the intended application. As mechanical engineering students delve into the realm of heat exchangers, a profound grasp of these key components and working principles becomes the foundation upon which they build their capacity to design, analyze, and innovate in the ever-evolving landscape of thermal engineering.
Heat Exchanger Design:
Heat exchanger design stands at the crossroads of theoretical knowledge and practical application, representing a critical juncture where the principles of thermodynamics and fluid mechanics converge to shape the efficiency and performance of diverse industrial processes. At its essence, a heat exchanger serves as a nexus for the exchange of thermal energy between two or more fluids, a fundamental process that underpins countless applications in the realms of power generation, chemical processing, HVAC systems, and more. The intricacies of designing a heat exchanger go beyond the theoretical foundations, demanding a holistic understanding of thermal dynamics, fluid flow, and material properties.
Thermal design, the initial phase in the process, involves a meticulous balance of considerations to optimize the performance of the heat exchanger. Engineers must grapple with determining the size of the heat exchanger, selecting materials that withstand operational conditions, and navigating the labyrinth of fluid properties. This phase requires a synthesis of theoretical knowledge and practical application, as the engineer strives to create a design that not only maximizes heat transfer efficiency but also aligns with the specific requirements of the intended application. The art of thermal design is where the theoretical underpinnings of thermodynamics come alive, guiding engineers in the quest for an optimal balance between heat transfer rates and energy conservation.
Fluid flow and pressure drop analysis constitute the subsequent layer of complexity in the heat exchanger design process. Understanding fluid dynamics is paramount as engineers navigate the intricate patterns of fluid flow within the exchanger. The challenge lies not only in achieving efficient heat transfer but also in minimizing pressure drops to enhance overall performance. This demands a keen awareness of how fluid behavior impacts the heat exchanger's effectiveness, compelling engineers to optimize flow patterns and configurations for peak efficiency.
The iterative nature of heat exchanger design becomes apparent as engineers refine their initial designs based on performance metrics and real-world considerations. Effectiveness, temperature profiles, and the log mean temperature difference (LMTD) emerge as critical benchmarks for evaluating the efficiency of the heat exchanger. Case studies highlighting real-world applications provide invaluable insights, illustrating how theoretical design considerations manifest in actual industrial scenarios.
In conclusion, heat exchanger design represents a dynamic and multidimensional challenge for mechanical engineers. It encapsulates the essence of their role in translating theoretical principles into tangible solutions for complex thermal problems. As students and practitioners delve into this realm, they not only deepen their understanding of thermodynamics in practice but also contribute to the continuous evolution of efficient and sustainable engineering solutions in the ever-changing landscape of mechanical engineering.
Thermal Design Considerations:
Thermal design considerations in the realm of heat exchangers delve into the intricate science of optimizing the transfer of thermal energy while navigating a myriad of factors that impact performance and efficiency. At the core of this phase lies the determination of the size of the heat exchanger, a pivotal decision that directly influences its effectiveness. Engineers must meticulously calculate the required surface area for heat exchange, factoring in considerations such as the type of heat exchanger, fluid properties, and the desired temperature differentials. Material selection becomes another critical aspect, as the chosen materials must withstand the operating conditions, ensuring durability and longevity. The thermal conductivity and corrosion resistance of materials play a crucial role, guiding engineers in selecting the most appropriate alloys or composites for specific applications.
Fluid properties, including temperature, viscosity, and heat capacity, are integral considerations in thermal design. Engineers must navigate these properties to ensure optimal heat transfer rates and efficiency. Understanding the intricacies of how different fluids interact within the heat exchanger—whether it involves phase changes, as in boiling or condensation processes, or the complexities of multiphase flow—adds layers of complexity to the thermal design process.
Moreover, the thermal design phase demands a keen awareness of fluid-side and tube-side heat transfer coefficients. These coefficients quantify the efficiency of heat exchange between the fluids and the tube surfaces, requiring engineers to strike a delicate balance between maximizing these coefficients for enhanced heat transfer and considering practical limitations.
As engineers grapple with these considerations, the challenge lies in achieving a thermal design that not only meets the specific requirements of the intended application but also optimizes energy conservation. This intricate dance between theoretical calculations and real-world constraints showcases the essence of thermal design in heat exchanger engineering—a discipline where the principles of thermodynamics come alive, guiding engineers in the pursuit of efficiency, sustainability, and innovation. In navigating the complexities of thermal design, mechanical engineers pave the way for advancements that impact diverse industries, from power generation to manufacturing, contributing to the continual evolution of heat exchanger technology.
Fluid Flow and Pressure Drop Analysis:
Fluid flow and pressure drop analysis constitute a critical facet of heat exchanger design, where the intricate dynamics of fluid behavior profoundly impact overall performance. Engineers, tasked with optimizing heat transfer efficiency, delve into the complexities of fluid flow patterns within the heat exchanger to ensure the controlled and efficient exchange of thermal energy. This analysis is particularly vital in applications where minimizing pressure drops is crucial for operational success. Fluid dynamics principles guide engineers in comprehending how different flow regimes, such as laminar or turbulent, influence heat transfer. The challenge lies in striking a delicate balance—maximizing heat transfer rates while minimizing the energy expended to overcome fluid friction.
Pressure drops, a measure of the energy lost as the fluid moves through the heat exchanger, becomes a key parameter in this phase. Engineers meticulously analyze the entire fluid path, from the entry point through the tubes and headers to the exit, evaluating pressure losses at each stage. This analysis encompasses considerations of pipe diameters, lengths, bends, and restrictions, all of which contribute to the resistance encountered by the fluid. The goal is to optimize flow configurations to minimize pressure drops, ensuring that the heat exchanger operates efficiently with minimal energy consumption.
Furthermore, the understanding of Reynolds numbers, flow velocities, and the impact of fluid properties on pressure drop allows engineers to fine-tune designs for specific applications. In situations where space is a premium or where pumping costs need to be minimized, the ability to mitigate pressure drops becomes a crucial design parameter. This phase of analysis not only requires a theoretical understanding of fluid mechanics but also demands practical considerations that align with the constraints of the intended application.
In essence, fluid flow and pressure drop analysis embody the bridge between theoretical knowledge and practical implementation in heat exchanger design. As engineers navigate the intricacies of fluid behavior within these systems, they not only optimize thermal efficiency but also contribute to the overarching goals of sustainability and energy conservation in the dynamic landscape of mechanical engineering.
Heat Exchanger Analysis:
Heat exchanger analysis represents the culmination of theoretical knowledge and practical application in the dynamic field of mechanical engineering. As an essential phase in the lifecycle of a heat exchanger, analysis aims to scrutinize and optimize the device's performance under varying operating conditions. This critical evaluation ensures that the heat exchanger not only meets design specifications but also excels in real-world applications, contributing to the efficiency and sustainability of diverse industrial processes. The analysis phase goes beyond the theoretical framework, demanding a hands-on approach to validate and fine-tune the initial design in response to the complexities of actual operating environments.
Performance metrics take center stage in heat exchanger analysis, offering a quantitative lens through which engineers assess the effectiveness of the thermal exchange process. Metrics such as effectiveness, temperature profiles, and the log mean temperature difference (LMTD) become pivotal benchmarks. Effectiveness, often expressed as a ratio of actual heat transfer to the maximum possible heat transfer, provides insights into the efficiency of the heat exchanger design. Temperature profiles, mapping the variation of temperatures across the exchanger, offer a visual representation of the thermal behavior within the system. The LMTD, a key parameter in heat exchanger theory, quantifies the average temperature difference between the hot and cold fluids, guiding engineers in refining their designs for optimal performance.
Real-world case studies further enrich the analysis, offering a bridge between theoretical concepts and practical implementation. These studies provide a contextual understanding of how heat exchangers function in actual industrial settings, showcasing their impact on energy conservation, process efficiency, and overall system performance. Examining diverse applications, from power generation plants to chemical processing facilities, allows engineers to extrapolate insights and adapt their designs to the unique challenges posed by different industries.
The iterative nature of heat exchanger analysis becomes apparent as engineers revisit and refine their designs based on observed performance and case study learnings. Adjustments may be made to fluid flow rates, temperature differentials, or even material selections to enhance overall efficiency. This phase not only validates the theoretical assumptions made during the design but also provides a platform for continuous improvement, aligning the heat exchanger with the dynamic demands of its operational context.
In conclusion, heat exchanger analysis represents the nexus of theoretical knowledge, practical application, and real-world relevance in the realm of mechanical engineering. As engineers embark on this phase, they engage in a comprehensive exploration of the device's performance metrics and draw inspiration from case studies that illustrate the tangible impact of their designs. By embracing the challenges posed by diverse operating conditions, engineers refine and optimize heat exchangers, contributing to the advancement of energy-efficient and sustainable solutions that define the forefront of mechanical engineering innovation.
Performance Metrics:
Performance metrics in the context of heat exchanger analysis are the quantitative measures that engineers employ to evaluate the effectiveness and efficiency of these thermal devices. These metrics serve as key indicators, providing insights into how well a heat exchanger is performing its primary function of transferring thermal energy between fluids. One fundamental metric is effectiveness, denoting the ratio of actual heat transfer to the maximum possible heat transfer. High effectiveness signifies that the heat exchanger operates close to its optimal efficiency, ensuring that a significant portion of the available thermal energy is successfully transferred between the fluids.
Temperature profiles play a crucial role as performance metrics, offering a detailed visualization of how temperatures vary across the heat exchanger. These profiles help engineers identify regions of efficient heat transfer and pinpoint areas where improvements may be necessary. Additionally, the log mean temperature difference (LMTD) stands out as a pivotal metric in heat exchanger analysis. The LMTD quantifies the average temperature difference between the hot and cold fluids, providing a comprehensive parameter for assessing the overall efficiency of the heat exchange process. Engineers leverage the LMTD to refine their designs, aiming for configurations that maximize the temperature differential and, consequently, enhance heat transfer rates.
Beyond these fundamental metrics, engineers also consider factors such as pressure drop and fouling. Pressure drops, indicative of the energy losses incurred as fluids traverse the heat exchanger, influences the overall efficiency of the device. Minimizing pressure drop is crucial to ensure that the heat exchanger operates with minimal energy consumption. Fouling factors, accounting for the gradual accumulation of deposits on heat exchanger surfaces, are essential performance metrics, as fouling can significantly degrade efficiency over time. Engineers monitor these factors to assess the longevity and sustainability of the heat exchanger's performance.
In essence, performance metrics in heat exchanger analysis serve as the quantitative tools that guide engineers in refining and optimizing these thermal devices. By meticulously evaluating effectiveness, temperature profiles, LMTD, pressure drop, and fouling factors, engineers ensure that their designs align with the efficiency and sustainability goals of the broader mechanical engineering landscape. These metrics not only validate theoretical design assumptions but also provide a foundation for continuous improvement and innovation in the quest for energy-efficient solutions.
Case Studies and Real-World Applications:
The integration of case studies and real-world applications is a cornerstone of comprehensive heat exchanger analysis, offering engineers invaluable insights into the practical implications and challenges encountered in actual industrial scenarios. By examining these tangible examples, mechanical engineers gain a nuanced understanding of how heat exchangers perform in diverse settings, enriching their theoretical knowledge with practical considerations. Case studies serve as intricate narratives, illustrating the complex interplay between design decisions and operational outcomes.
One compelling aspect of incorporating case studies is the opportunity to explore heat exchanger applications in industries such as power generation, chemical processing, and HVAC systems. Power generation plants, for instance, rely on heat exchangers for efficient steam generation, showcasing the critical role these devices play in optimizing energy conversion processes. Chemical processing facilities leverage heat exchangers in various unit operations, from condensing vaporized products to heating and cooling reaction mixtures. HVAC systems utilize heat exchangers for climate control, emphasizing the adaptability of these devices in enhancing both comfort and energy efficiency in buildings.
Real-world applications bring to light the challenges and considerations that may not be apparent in theoretical models. Factors such as varying operating conditions, fluid properties, and environmental constraints become tangible variables that engineers must navigate to achieve optimal performance. This hands-on approach allows engineers to refine their designs based on observed outcomes and adapt to the ever-changing demands of industrial settings.
Moreover, case studies serve as a platform for continuous learning and improvement. Engineers can draw parallels between different applications, identifying commonalities and variations that inform the development of versatile and robust heat exchanger designs. By dissecting the successes and challenges faced in these real-world applications, engineers enhance their problem-solving skills and develop a holistic perspective that transcends theoretical constraints.
In essence, the integration of case studies and real-world applications in heat exchanger analysis empowers engineers to bridge the gap between theory and practice. This approach not only validates theoretical models but also fosters a culture of innovation and adaptability, ensuring that heat exchanger designs remain at the forefront of efficiency and sustainability in the ever-evolving landscape of mechanical engineering.
Conclusion:
In conclusion, the exploration of "Heat Exchanger Design and Analysis Assignment: Thermodynamics in Practice" unveils the multifaceted nature of mechanical engineering, where theoretical knowledge converges with real-world applications to shape the efficiency and sustainability of industrial processes. Heat exchangers, as pivotal components in diverse applications, encapsulate the intricate dance between thermodynamics principles and practical considerations. The journey from understanding the basics and exploring types of heat exchangers to delving into key components and working principles represents a progressive immersion into the complexities of this critical thermal engineering domain.
Thermal design considerations underscore the importance of meticulous planning and optimization, where engineers balance the intricacies of fluid properties, materials, and system requirements. Fluid flow and pressure drop analysis add further layers of complexity, demanding a profound understanding of fluid dynamics and the ability to fine-tune designs for optimal performance. The integration of performance metrics provides a quantitative lens through which engineers evaluate the effectiveness of their designs, emphasizing the significance of factors such as temperature profiles, LMTD, and pressure drop in achieving energy-efficient solutions.
Crucially, the inclusion of case studies and real-world applications elevates the educational journey by grounding theoretical knowledge in practical contexts. Power generation plants, chemical processing facilities, and HVAC systems serve as dynamic canvases where heat exchangers play pivotal roles, highlighting the adaptability and versatility of these devices. The challenges and successes observed in these industrial settings provide engineers with a wealth of experiences, fostering a culture of continuous learning and improvement.
In the dynamic landscape of mechanical engineering, the heat exchanger analysis phase represents the convergence of theory and practice. Engineers navigate a maze of considerations, from optimizing thermal performance to mitigating pressure drops and addressing real-world challenges. The iterative nature of this process ensures that designs evolve, adapting to the demands of diverse applications and contributing to the ongoing quest for energy-efficient and sustainable solutions.
As the exploration of heat exchanger design and analysis concludes, the overarching takeaway is the realization that mechanical engineering is not just a theoretical pursuit but a dynamic and evolving discipline. By embracing the complexities of thermodynamics in practice, engineers pave the way for innovation, excellence, and advancements that shape the future of energy-efficient technologies. The journey into the intricacies of heat exchangers serves as a microcosm of the broader quest within mechanical engineering—to seamlessly integrate theoretical knowledge with practical application, driving progress and ensuring a sustainable and efficient future for industrial processes.