Exploring Fluid Dynamics in CATIA: A Student's Resource
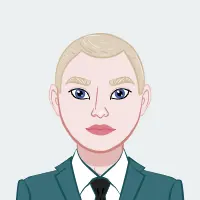
Fluid dynamics plays a pivotal role in the realm of mechanical engineering, serving as a fundamental branch that investigates the behavior of fluids, encompassing both liquids and gases, in motion. The significance of understanding fluid dynamics lies in its widespread applications across various industries, where it influences the design, analysis, and optimization of countless engineering systems. Mechanical engineers delve into fluid dynamics to comprehend phenomena such as fluid flow patterns, pressure distributions, and turbulence, crucial for the optimal functioning of devices ranging from aircraft wings to industrial pipelines. As fluid dynamics governs the behavior of substances in motion, its mastery becomes indispensable for engineers seeking to enhance the efficiency, safety, and performance of diverse mechanical systems. If you need assistance with your CATIA assignment, consider this exploration of the significance of fluid dynamics in mechanical engineering as a valuable resource, providing insights into its applications and assisting you in mastering the challenges of your CATIA assignments.
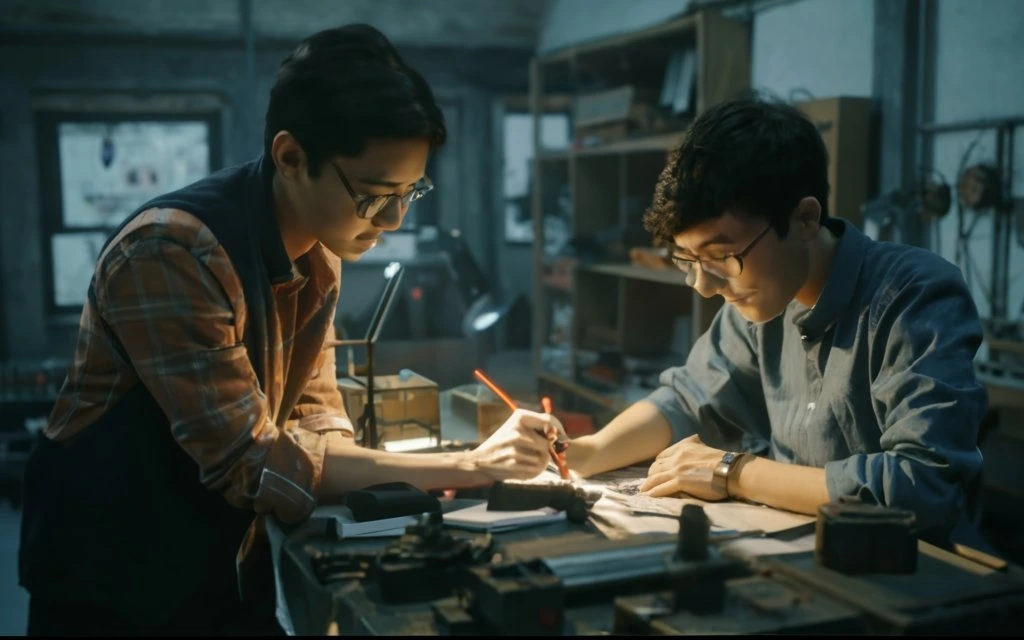
In this intricate landscape of fluid dynamics, Computer-Aided Design (CAD) tools emerge as indispensable assets for mechanical engineers, providing them with the capability to simulate and analyze fluid dynamics with precision and efficiency. Among these tools, CATIA (Computer-Aided Three-Dimensional Interactive Application) stands out as a versatile and powerful software suite that plays a pivotal role in revolutionizing the way fluid dynamics is studied and applied in mechanical engineering. CATIA offers a comprehensive environment for engineers to create, modify, and analyze 3D models of products, and its fluid dynamics simulation capabilities elevate it to a crucial tool for understanding and predicting the behavior of fluids within a given system.
The role of CATIA in simulating fluid dynamics lies in its advanced computational capabilities, enabling engineers to model complex fluid flow scenarios with remarkable accuracy. Engineers can simulate various fluid dynamics phenomena, such as laminar and turbulent flows, heat transfer, and pressure distribution, providing valuable insights into how fluids interact with mechanical components. CATIA facilitates a virtual environment where engineers can observe and analyze the impact of design changes on fluid behavior without the need for physical prototypes, thus streamlining the product development process.
Moreover, CATIA's analytical tools empower engineers to optimize designs by iteratively testing different configurations and parameters. This not only accelerates the engineering design cycle but also enhances the reliability and performance of mechanical systems. By leveraging CATIA for fluid dynamics analysis, engineers gain a deeper understanding of how fluids influence the structural integrity and functionality of their designs, leading to more informed decision-making throughout the product development lifecycle.
In conclusion, fluid dynamics stands as a cornerstone in the field of mechanical engineering, shaping the understanding and design of systems where fluid behavior is a critical factor. CATIA, with its advanced simulation and analysis capabilities, emerges as an invaluable companion for engineers navigating the complexities of fluid dynamics. As technology continues to evolve, the synergy between fluid dynamics principles and cutting-edge CAD tools like CATIA remains pivotal, empowering engineers to push the boundaries of innovation and efficiency in the dynamic world of mechanical engineering.
Understanding Fluid Dynamics:
Fluid dynamics, at its core, is a branch of fluid mechanics that explores the motion and behavior of fluids, encompassing both liquids and gases. For those unfamiliar with the concept, understanding the fundamental principles is crucial. At its most basic level, fluid dynamics delves into how fluids respond to various forces and conditions, unraveling the complexities of fluid motion in a wide array of scenarios.
One key term in fluid dynamics is "flow," which refers to the movement of fluids. Understanding the different types of flows is essential; "steady flow" implies a consistent fluid velocity at a given point, while "unsteady flow" involves variations in velocity over time. The concept of "viscosity" is paramount, representing the fluid's resistance to deformation or flow. High viscosity, as seen in honey, results in slower flow, while low viscosity, as in water, allows for more rapid movement.
Principles like "Bernoulli's Equation" play a pivotal role in fluid dynamics, describing the relationship between fluid velocity, pressure, and potential energy. This equation is foundational for comprehending the dynamics of airflow around objects, explaining phenomena like lift in aviation. Another crucial principle is "Pascal's Law," stating that changes in pressure applied to a fluid are transmitted undiminished in all directions. This principle is central to hydraulic systems, where fluid pressure can be harnessed to transmit force and perform mechanical work.
Fluid dynamics introduces the concept of "Reynolds number," a dimensionless quantity that characterizes the flow patterns of a fluid. It determines whether the flow is laminar (smooth and predictable) or turbulent (chaotic and irregular). Engineers use this parameter to assess the stability of fluid flow in various applications, from pipelines to aircraft wings.
The study of "boundary layers" is vital, addressing the thin layer of fluid adjacent to a surface. Understanding how this layer behaves is crucial for predicting friction, heat transfer, and drag in fluid systems. Additionally, the "Navier-Stokes equations" represent the fundamental equations of motion for fluid dynamics, describing how the velocity field of a fluid evolves over time.
In essence, fluid dynamics is a captivating field that unveils the intricacies of how fluids move and behave. By grasping key terms like viscosity, principles such as Bernoulli's Equation, and concepts like Reynolds number, individuals can embark on a journey to comprehend the fascinating world of fluid dynamics, where the principles learned find applications in fields as diverse as aerospace engineering, environmental science, and beyond.
Importance of CATIA in Mechanical Engineering:
CATIA, an acronym for Computer-Aided Three-Dimensional Interactive Application, stands as a powerhouse in the realm of mechanical engineering, holding immense significance for professionals and students alike. Developed by Dassault Systèmes, CATIA is renowned for its comprehensive suite of design and simulation tools, offering a robust platform for engineers to conceptualize, design, and analyze complex 3D models. Its versatility extends across various engineering disciplines, making it an indispensable tool for product development.
In the context of mechanical engineering, CATIA excels in providing a unified environment for designing and simulating mechanical components and systems. Its parametric modeling capabilities enable engineers to create detailed and customizable 3D models, facilitating a seamless transition from conceptualization to the final product. The software's ability to handle intricate assemblies with ease makes it particularly advantageous in designing complex mechanical systems, such as aircraft, automobiles, and industrial machinery.
One of CATIA's standout features is its integration of simulation tools, and it plays a pivotal role in fluid dynamics simulations. The software's fluid dynamics simulation capabilities are instrumental for engineers seeking to understand and optimize the behavior of fluids within mechanical systems. CATIA allows users to set up and run sophisticated fluid dynamics simulations, enabling the analysis of factors like fluid flow patterns, pressure distributions, and heat transfer. Its user-friendly interface empowers both novice and experienced engineers to delve into the intricacies of fluid dynamics without a steep learning curve.
CATIA's simulation features go beyond basic analysis, offering a virtual testing ground for engineers to assess the performance of their designs under various conditions. This proves invaluable in optimizing products for efficiency, reliability, and safety. The software's ability to simulate real-world scenarios aids in predicting how fluid dynamics will impact the structural integrity and functionality of mechanical systems, allowing engineers to make informed decisions throughout the design process.
Furthermore, CATIA facilitates collaboration among team members by providing a centralized platform for design and simulation data. This collaborative approach enhances efficiency in multidisciplinary projects, allowing mechanical engineers to seamlessly integrate fluid dynamics simulations with overall system design.
In summary, CATIA's significance in mechanical engineering lies in its holistic approach to product development, offering a robust set of design and simulation tools. Its fluid dynamics simulation features empower engineers to explore and optimize the behavior of fluids within mechanical systems, contributing to the creation of innovative and high-performance products in industries ranging from aerospace to automotive and beyond.
Fluid Dynamics Simulation in CATIA:
Setting up a fluid dynamics simulation in CATIA involves a systematic process that harnesses the software's advanced capabilities to model and analyze the behavior of fluids within a given system. The journey begins with the creation of a 3D model of the system using CATIA's parametric modeling tools. Engineers define the geometry of the fluid domain, including boundaries, inlets, outlets, and any solid surfaces interacting with the fluid. The software's intuitive interface facilitates the generation of a comprehensive representation of the physical system under consideration.
Once the geometry is established, the next step involves meshing, a crucial aspect of fluid dynamics simulation. CATIA employs sophisticated meshing algorithms to divide the fluid domain into discrete elements, enabling the software to numerically solve the governing equations of fluid flow. Mesh refinement is performed to ensure accurate representation of fluid behavior, particularly in regions with high gradients or complex flow patterns.
Following meshing, engineers define the fluid properties and boundary conditions. CATIA allows users to specify parameters such as viscosity, density, and thermal conductivity, as well as define how the fluid interacts with solid surfaces. Boundary conditions, including inflow velocities, temperatures, and pressure conditions, are set to replicate real-world scenarios accurately.
CATIA's solver then utilizes the finite volume method to numerically solve the Navier-Stokes equations, capturing the dynamics of fluid flow, heat transfer, and pressure distribution within the defined system. Engineers can monitor and analyze simulation results in real-time, gaining insights into flow patterns, turbulence, and other critical parameters.
CATIA's fluid dynamics capabilities extend to addressing a diverse range of engineering problems. Engineers can use CATIA for aerodynamic simulations, evaluating the airflow around aircraft wings, automotive components, or any object moving through a fluid medium. The software is instrumental in heat transfer analysis, helping engineers optimize thermal management in electronic devices, industrial processes, and more. Fluid-structure interaction problems, where fluid flow influences the structural behavior of components, can also be studied using CATIA's simulation capabilities.
Furthermore, CATIA proves invaluable in simulating multiphase flows, such as liquid-gas interactions or free surface flows. This is particularly relevant in industries like oil and gas, where the behavior of multiphase fluids in pipelines and reservoirs must be thoroughly understood for effective design and operation.
In essence, CATIA's fluid dynamics simulation process is a comprehensive and versatile toolset for addressing a wide spectrum of engineering challenges. From aerodynamics to heat transfer and multiphase flows, the software empowers engineers to gain a deeper understanding of fluid behavior and make informed design decisions across diverse industries.
Real-world Applications:
Fluid dynamics simulations in CATIA find extensive real-world applications across various mechanical engineering projects, contributing to the design, optimization, and performance assessment of critical systems. In the aerospace industry, CATIA's fluid dynamics capabilities play a pivotal role in aerodynamic analyses. For instance, engineers employ CATIA simulations to study the airflow around aircraft components like wings, fuselage, and control surfaces. This enables them to optimize aerodynamic efficiency, minimize drag, and enhance fuel efficiency, contributing to the overall performance and safety of aircraft.
In the automotive sector, fluid dynamics simulations in CATIA are employed for vehicle design and aerodynamic optimization. Engineers use simulations to analyze the airflow around cars, trucks, and other vehicles, ensuring optimal aerodynamic performance to reduce fuel consumption and enhance stability. By simulating various design configurations, CATIA aids in achieving the delicate balance between aerodynamic efficiency and aesthetic design, a critical factor in the competitive automotive market.
The energy industry leverages CATIA's fluid dynamics simulations to optimize the performance of power generation systems. For example, in the design of gas turbines for power plants, engineers use CATIA to simulate the combustion process, heat transfer, and fluid flow within the turbine. This enables them to enhance energy efficiency, reduce emissions, and improve the overall reliability of the power generation system.
In the realm of consumer electronics, CATIA's fluid dynamics simulations contribute to the thermal management of devices. Engineers simulate heat dissipation and airflow patterns within electronic components to prevent overheating, ensuring the reliability and longevity of products such as laptops, smartphones, and servers.
One notable case study involves the automotive industry, where CATIA simulations were employed to optimize the aerodynamics of a Formula 1 car. By analyzing the airflow around the vehicle in various scenarios, engineers were able to refine the car's design to maximize downforce and minimize drag. The result was a Formula 1 car that exhibited superior performance on the racetrack, showcasing the impact of CATIA's fluid dynamics simulations in a highly competitive and technologically advanced environment.
Another success story involves the design of high-speed trains. CATIA's fluid dynamics simulations were utilized to study the aerodynamics of train components, minimizing air resistance and optimizing the overall design for maximum speed and efficiency. This application highlights how CATIA's simulations contribute to advancements in transportation by ensuring that high-speed trains are both aerodynamically efficient and environmentally sustainable.
In conclusion, CATIA's fluid dynamics simulations have a profound impact on real-world mechanical engineering projects, ranging from aerospace and automotive design to energy systems and consumer electronics. Case studies and success stories underscore the software's ability to drive innovation, improve efficiency, and contribute to the development of cutting-edge technologies across diverse industries.
Conclusion:
The blog post "Exploring Fluid Dynamics in CATIA: A Student's Resource" delves into the significance of fluid dynamics in mechanical engineering and highlights CATIA's pivotal role in simulating and analyzing fluid dynamics. The post begins by emphasizing the fundamental importance of fluid dynamics in understanding the behavior of liquids and gases in motion, showcasing its critical role in designing and optimizing mechanical systems. It then shifts focus to CATIA, a powerful Computer-Aided Design (CAD) tool and discusses its versatile features that make it indispensable in the field of mechanical engineering. CATIA's prowess in creating, modifying, and analyzing 3D models, coupled with its fluid dynamics simulation capabilities, emerges as a game-changer for engineers.
The post provides a walkthrough of the process involved in setting up a fluid dynamics simulation in CATIA. It covers key steps such as creating the 3D model, meshing, defining fluid properties, and boundary conditions. The software's advanced simulation features, including real-time analysis and virtual testing, are highlighted, showcasing its user-friendly interface for both novice and experienced engineers. Moreover, the diverse range of engineering problems addressed by CATIA's fluid dynamics simulations is explored, encompassing aerodynamics, heat transfer, and multiphase flows. Real-world applications in aerospace, automotive, energy, and consumer electronics industries are presented, illustrating the tangible impact of CATIA simulations on critical projects.
The blog post concludes with an encouragement for students to explore fluid dynamics further and leverage CATIA for their assignments. Students are urged to delve into the complexities of fluid dynamics, understanding its principles and applications in mechanical engineering. The seamless integration of CATIA's simulation tools provides an opportunity for students to gain hands-on experience in analyzing fluid behavior, optimizing designs, and making informed decisions in their academic projects. By emphasizing the practical applications and real-world relevance of fluid dynamics and CATIA, the blog aims to inspire students to embrace the challenges of this dynamic field and harness the powerful tools available to them for academic success and future professional endeavors.