Advanced Techniques in Finite Element Analysis for Solids and Fluids
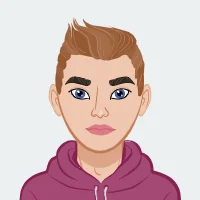
Finite Element Analysis (FEA) is a powerful numerical method used for solving complex structural, fluid, and thermal problems. By breaking down a large system into smaller, more manageable elements, FEA allows for precise approximation of physical behaviors, making it an indispensable tool in modern engineering. This method is crucial in engineering, as it helps predict how products react to real-world forces, vibration, heat, fluid flow, and other physical effects. Engineers rely on FEA to optimize designs, improve product performance, and ensure safety and compliance with industry standards. Whether you're dealing with the structural integrity of a bridge, the thermal distribution in an engine component, or the fluid dynamics in a pipeline, FEA provides a detailed insight into how these systems behave under various conditions.
Understanding how to apply FEA to various engineering problems can be challenging, involving a deep understanding of mathematical formulations, material properties, and boundary conditions. It requires a solid foundation in the principles of mechanics, numerical methods, and computational techniques. However, with the right approach, it becomes manageable and highly rewarding. This blog will guide you through the fundamental steps of tackling FEA problems, from understanding the theoretical background to practical implementation, ensuring you can confidently approach similar Finite Element Analysis assignments with proficiency and confidence. By mastering these steps, you'll be able to dissect complex engineering problems, develop accurate models, and interpret results to make informed design decisions. Whether you are a student new to FEA or an experienced engineer looking to refine your skills, this guide will provide valuable insights and practical tips to enhance your understanding and application of finite element analysis.
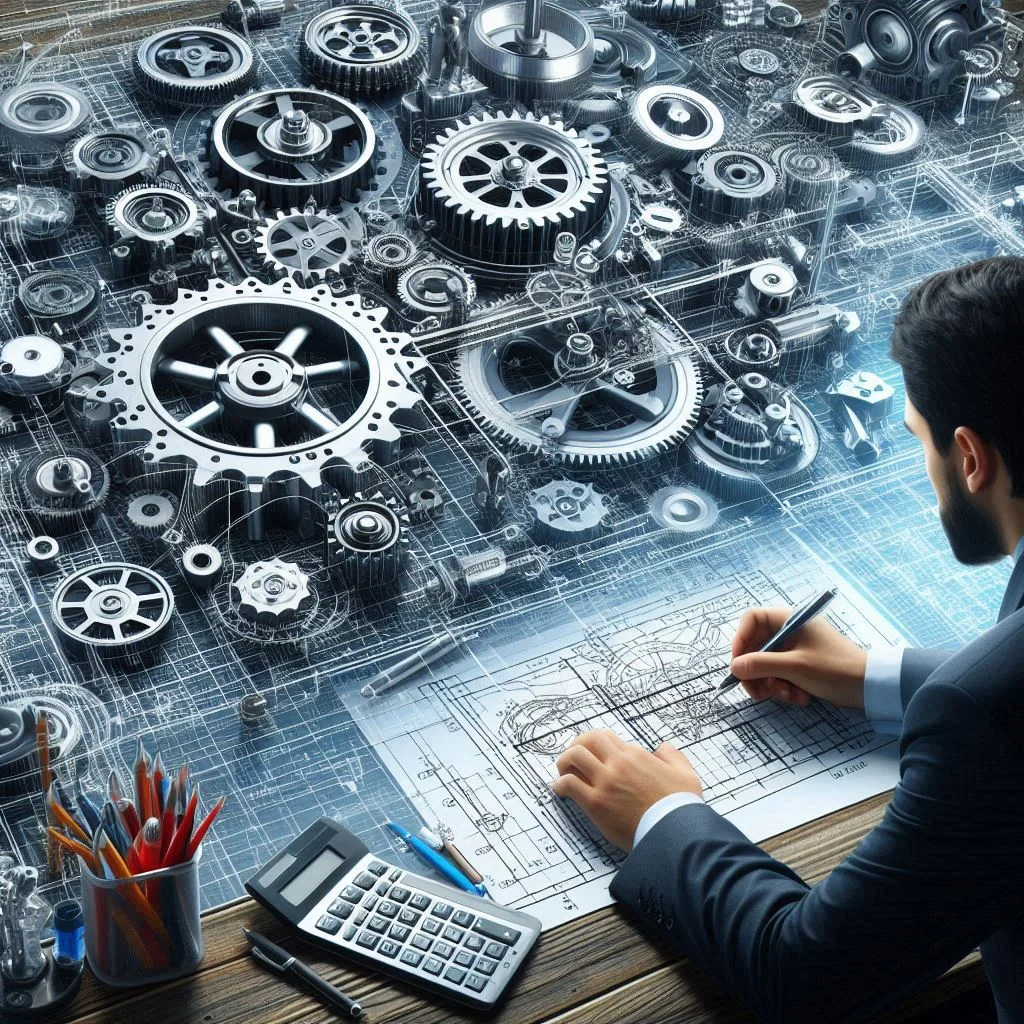
Understanding the Problem Statement
Before diving into the calculations and numerical methods involved in Finite Element Analysis (FEA), it is crucial to thoroughly understand the problem statement. This initial step sets the foundation for the entire analysis and ensures that you correctly interpret the physical phenomena and requirements of the problem. Here are the key aspects to consider:
- Governing Equations: Identify the differential equations that govern the physical behavior of the system. These equations describe how variables such as displacement, temperature, or fluid velocity change within the domain. For example, in the given problem, the equation is 2d2θdx2=d2vdx2+kcθ2 \frac{d^2 \theta}{dx^2} = \frac{d^2 v}{dx^2} + \frac{k}{c} \theta2dx2d2θ=dx2d2v+ckθ. Understanding these equations is fundamental as they form the basis of the FEA model.
- Non-Dimensional Form: Converting the governing equations to their non-dimensional form can simplify the problem and make it easier to handle. Non-dimensionalization often reduces the number of parameters, allowing for a clearer understanding of the problem's core dynamics. This step involves identifying characteristic scales for the variables and normalizing the equations accordingly.
- Boundary Conditions: Clearly define the boundary conditions for the problem. Boundary conditions specify the values of the variables or their derivatives at the boundaries of the domain. These conditions are essential for the accurate application of FEA, as they ensure that the solution is physically meaningful and adheres to the real-world constraints of the problem. Types of boundary conditions include Dirichlet (fixed value), Neumann (fixed gradient), and mixed conditions.
- Initial Conditions: For time-dependent problems, initial conditions must be specified. These conditions provide the state of the system at the beginning of the analysis. Properly defining initial conditions is crucial for dynamic simulations and transient analyses.
- Material Properties: Gather all relevant material properties that affect the behavior of the system. These properties include elasticity, thermal conductivity, density, viscosity, and others depending on the nature of the problem. Accurate material properties are vital for realistic simulation results.
- Geometric Considerations: Understand the geometry of the problem domain. Complex geometries may require special meshing techniques or simplifications to make the problem tractable. Accurately representing the geometry is important for ensuring that the FEA results are applicable to the actual physical system.
- External Forces and Loads: Identify any external forces, loads, or other influences acting on the system. These could be mechanical loads, thermal loads, fluid pressures, or other types of external effects. Properly defining these inputs is necessary for obtaining meaningful results from the FEA.
- Objective of the Analysis: Clearly state the objective of the analysis. Are you looking to determine stress distribution, deformation, temperature gradients, or fluid flow characteristics? Knowing the specific goals of the analysis helps in setting up the problem correctly and interpreting the results effectively.
By thoroughly understanding the problem statement and considering all these aspects, you can ensure that your FEA model accurately represents the physical system and provides reliable results. This foundational step is critical for the success of the entire analysis process and sets the stage for effective problem-solving in engineering applications.
Discretization of the Domain
Discretization of the domain is a fundamental step in Finite Element Analysis (FEA), where the continuous problem domain is divided into a finite number of smaller, simpler parts called elements. This process transforms complex differential equations into a system of algebraic equations that can be solved numerically. Here's a detailed look at the key steps and considerations involved in the discretization of the domain:
1. Mesh Generation:
Element Types: Choose appropriate element types based on the problem's nature and complexity. Common element types include:
- 1D Elements: Line elements used for problems like trusses and beams.
- 2D Elements: Triangular or quadrilateral elements used for plane stress, plane strain, and shell problems.
- 3D Elements: Tetrahedral or hexahedral elements used for solid mechanics and three-dimensional heat transfer problems.
Mesh Density: Decide on the mesh density (fineness or coarseness of the mesh). A finer mesh provides more accurate results but increases computational cost. Balancing accuracy and computational efficiency is key.
Mesh Quality: Ensure high-quality mesh with well-shaped elements (avoiding overly skewed or stretched elements) to improve numerical stability and accuracy.
2. Element Equations:
- Interpolation Functions: Select appropriate interpolation (shape) functions to approximate the solution within each element. Linear shape functions are often used for simplicity, but higher-order functions (quadratic, cubic) can provide more accuracy.
- Local Coordinates: Define local coordinate systems for each element to simplify the formulation of element equations. This helps in mapping the global coordinates to local element coordinates.
3. Assembly of Global Equations:
- Element Stiffness Matrix: Compute the stiffness matrix for each element, which represents the relationship between nodal forces and displacements within the element.
- Global Stiffness Matrix: Assemble the global stiffness matrix by summing the contributions from all individual element stiffness matrices. This process involves mapping local element matrices to the global coordinate system and ensuring continuity across element boundaries.
4. Applying Boundary Conditions:
- Essential (Dirichlet) Boundary Conditions: Modify the global stiffness matrix and force vector to incorporate specified values of the primary variable (e.g., displacements or temperatures) at the boundary nodes.
- Natural (Neumann) Boundary Conditions: Incorporate specified values of the derivative of the primary variable (e.g., forces or heat fluxes) into the global force vector.
5. Load Application:
- External Loads: Distribute external loads (forces, pressures, thermal loads) to the appropriate nodes or elements in the mesh. Ensure accurate representation of the loading conditions to obtain meaningful results.
- Body Forces: Include body forces (e.g., gravitational forces) that act throughout the volume of the domain. These forces are often integrated over the elements and added to the global force vector.
6. Numerical Integration:
- Gauss Quadrature: Use numerical integration techniques, such as Gauss quadrature, to evaluate the integrals in the element equations. This involves selecting integration points and weights to accurately compute the contributions from each element.
7. Convergence and Refinement:
- Convergence Study: Perform a convergence study by refining the mesh and observing the changes in the results. A converged solution indicates that further mesh refinement does not significantly alter the results.
- Adaptive Mesh Refinement: Implement adaptive mesh refinement techniques to automatically refine the mesh in regions with high gradients or where higher accuracy is required. This improves efficiency by concentrating computational effort where it is most needed.
8. Geometric Representation:
- Complex Geometries: For problems with complex geometries, use advanced meshing tools to accurately capture the domain's shape. Techniques such as CAD integration and mesh smoothing can help create high-quality meshes for intricate geometries.
By carefully following these steps, you can discretize the domain effectively, ensuring that your FEA model accurately represents the physical system and provides reliable and accurate results. This crucial step in FEA allows you to transform complex engineering problems into a form that can be solved using numerical methods, enabling detailed analysis and optimization of engineering designs.
Application of the Principle of Virtual Work
The principle of virtual work is a fundamental concept in finite element analysis (FEA) that provides a powerful and general method for deriving the governing equations for mechanical systems. This principle states that the work done by internal forces on a virtual displacement must equal the work done by external forces. Here's a detailed explanation of how to apply the principle of virtual work in FEA:
1. Virtual Displacement and Virtual Work:
- Virtual Displacement: A virtual displacement is an infinitesimally small, arbitrary change in the system's configuration that is compatible with the boundary conditions. It does not correspond to any actual motion but is used as a hypothetical change to derive equations.
- Virtual Work: The virtual work done by internal forces (stresses) and external forces during this virtual displacement is considered. The principle of virtual work equates these two quantities.
2. Internal Virtual Work:
The internal virtual work is the work done by the internal forces (stresses) over the virtual displacements. For a solid body, this can be expressed as: δWinternal=∫Vσ:δϵ dV\delta W_{\text{internal}} = \int_V \boldsymbol{\sigma} : \delta \boldsymbol{\epsilon} \, dVδWinternal=∫Vσ:δϵdV where σ\boldsymbol{\sigma}σ is the stress tensor, δϵ\delta \boldsymbol{\epsilon}δϵ is the virtual strain tensor, and VVV is the volume of the body.
3. External Virtual Work:
The external virtual work is the work done by external forces, including body forces, surface forces, and point loads, over the virtual displacements. This can be expressed as: δWexternal=∫Vf⋅δu dV+∫ST⋅δu dS+∑iFi⋅δui\delta W_{\text{external}} = \int_V \mathbf{f} \cdot \delta \mathbf{u} \, dV + \int_S \mathbf{T} \cdot \delta \mathbf{u} \, dS + \sum_i \mathbf{F}_i \cdot \delta \mathbf{u}_iδWexternal=∫Vf⋅δudV+∫ST⋅δudS+i∑Fi⋅δui where f\mathbf{f}f is the body force per unit volume, T\mathbf{T}T is the surface traction, Fi\mathbf{F}_iFi are point forces, δu\delta \mathbf{u}δu is the virtual displacement vector, SSS is the surface area, and the summation is over all point forces.
4. Equilibrium Equations:
According to the principle of virtual work, the total virtual work done by internal and external forces must be equal for any virtual displacement: δWinternal=δWexternal\delta W_{\text{internal}} = \delta W_{\text{external}}δWinternal=δWexternal This equality leads to the weak form of the equilibrium equations, which is the basis for the finite element formulation.
5. Finite Element Formulation:
- Discretization: The domain is discretized into finite elements. The displacement field within each element is approximated using shape functions NiN_iNi and nodal displacements ui\mathbf{u}_iui: u≈∑i=1nNiui\mathbf{u} \approx \sum_{i=1}^n N_i \mathbf{u}_iu≈i=1∑nNiui
- Virtual Strain and Stress: The virtual strain δϵ\delta \boldsymbol{\epsilon}δϵ and stress σ\boldsymbol{\sigma}σ are derived from the virtual displacement and the constitutive relations.
- Element Stiffness Matrix: The internal virtual work for an element is: δWinternale=∫Veσ:δϵ dV=δuTKeu\delta W_{\text{internal}}^e = \int_{V_e} \boldsymbol{\sigma} : \delta \boldsymbol{\epsilon} \, dV = \delta \mathbf{u}^T \mathbf{K}_e \mathbf{u}δWinternale=∫Veσ:δϵdV=δuTKeu where Ke\mathbf{K}_eKe is the element stiffness matrix, which relates nodal forces to nodal displacements.
- Global Equations: Assemble the global stiffness matrix K\mathbf{K}K and force vector F\mathbf{F}F by summing contributions from all elements: Ku=F\mathbf{K} \mathbf{u} = \mathbf{F}Ku=F Here, K\mathbf{K}K is the global stiffness matrix, u\mathbf{u}u is the global displacement vector, and F\mathbf{F}F is the global force vector.
6. Applying Boundary Conditions:
Modify the global stiffness matrix and force vector to incorporate boundary conditions. Essential (Dirichlet) boundary conditions are applied by setting specified displacements, while natural (Neumann) boundary conditions are incorporated into the force vector.
7. Solving the System of Equations:
Solve the resulting system of algebraic equations to find the unknown nodal displacements. These displacements can then be used to compute strains, stresses, and other quantities of interest within each element.
By following these steps and applying the principle of virtual work, you can systematically derive and solve the finite element equations for a wide range of engineering problems. This approach ensures that the model accurately represents the physical behavior of the system, providing reliable results for design and analysis.
Solving the Discretized Equations
Once the domain has been discretized and the finite element model has been formulated, the next step in Finite Element Analysis (FEA) is to solve the resulting system of discretized equations. This involves finding the unknown nodal displacements, which can then be used to determine other quantities of interest such as strains, stresses, and reaction forces. Here are the detailed steps for solving the discretized equations:
1. Formulating the Global System of Equations:
After discretization, the finite element method converts the governing differential equations into a system of linear algebraic equations. This system can be written in matrix form as: Ku=F\mathbf{K} \mathbf{u} = \mathbf{F}Ku=F where K\mathbf{K}K is the global stiffness matrix, u\mathbf{u}u is the vector of unknown nodal displacements, and F\mathbf{F}F is the global force vector.
2. Applying Boundary Conditions:
Essential (Dirichlet) Boundary Conditions: These conditions specify the values of the primary variable (e.g., displacements in structural problems) at certain nodes. These known values must be incorporated into the system of equations by modifying the stiffness matrix and the force vector. Typically, this involves:
- Setting the corresponding entries in the displacement vector u\mathbf{u}u to the known values.
- Adjusting the force vector F\mathbf{F}F to account for these known displacements.
- Modifying the stiffness matrix K\mathbf{K}K to ensure that the equations reflect the boundary conditions.
Natural (Neumann) Boundary Conditions: These conditions specify the values of the derivative of the primary variable (e.g., forces or fluxes) and are incorporated directly into the force vector F\mathbf{F}F.
3. Solving the Linear System:
The modified system of equations after applying boundary conditions can be solved using various numerical techniques. Common methods include:
- Direct Methods: These involve matrix factorizations such as Gaussian elimination, LU decomposition, or Cholesky decomposition. Direct methods are highly accurate but can be computationally expensive for large systems.
- Iterative Methods: These methods, such as the Conjugate Gradient (CG) method, Generalized Minimal Residual (GMRES) method, and Multigrid methods, are often used for large, sparse systems. Iterative methods are more memory-efficient and can handle larger problems but may require good preconditioning to ensure convergence.
4. Post-Processing the Results:
Once the nodal displacements u\mathbf{u}u are obtained, other quantities of interest can be calculated:
- Strains: The strain within each element can be computed using the displacement gradients. For linear elements, this is straightforward, but higher-order elements require more complex calculations.
- Stresses: Stresses are calculated from the strains using the material constitutive relations (e.g., Hooke's Law for linear elastic materials).
- Reaction Forces: Reaction forces at the constrained nodes can be determined from the global stiffness matrix and the known displacements.
5. Verifying and Validating the Results:
- Verification: Ensure that the numerical solution is correct by checking the residuals of the equations and verifying that the boundary conditions are satisfied.
- Validation: Compare the numerical results with experimental data or analytical solutions to validate the accuracy of the model. This step is crucial to ensure that the FEA model correctly represents the physical problem.
6. Refinement and Convergence Study:
- Mesh Refinement: If the results are not satisfactory, refine the mesh to increase the accuracy of the solution. This involves creating a denser mesh in regions with high gradients or where more precision is required.
- Convergence Study: Perform a convergence study by systematically refining the mesh and observing the changes in the results. Ensure that the solution converges to a stable value as the mesh is refined.
7. Interpreting the Results:
- Analyze the computed results to gain insights into the behavior of the system. For structural problems, this may involve examining stress distributions, deformation patterns, and identifying critical regions prone to failure. For thermal or fluid problems, it might involve analyzing temperature gradients, heat fluxes, or fluid velocities.
By following these steps, you can solve the discretized equations in FEA effectively, ensuring accurate and reliable results for engineering analysis and design. The ability to solve these equations efficiently is crucial for making informed decisions in the design, optimization, and safety assessment of engineering systems.
Post-Processing the Results
Post-processing is the final step in the finite element analysis (FEA) workflow, where the raw numerical results obtained from solving the discretized equations are interpreted, visualized, and analyzed to provide meaningful insights into the behavior of the system. This stage is crucial for validating the model, understanding the physical phenomena, and making informed decisions based on the simulation. Here's a detailed guide to post-processing the results:
1. Visualizing Displacements:
- Deformation Plot: Visualize the deformed shape of the structure or domain to understand how it responds to applied loads. This helps identify regions of significant deformation and overall structural behavior.
- Displacement Contours: Create contour plots of displacement magnitudes to easily see how displacement varies throughout the domain. These plots highlight areas of maximum and minimum displacement.
2. Calculating Strains:
- Strain Tensors: Compute the strain tensors within each element using the nodal displacements and shape functions. For small deformations, the linear strain-displacement relationship is used, while for large deformations, nonlinear formulations may be necessary.
- Strain Components: Visualize different components of the strain tensor (e.g., normal strains, shear strains) to understand how the material deforms in various directions.
3. Evaluating Stresses:
- Stress Tensors: Calculate the stress tensors from the strains using the material constitutive equations (e.g., Hooke’s Law for linear elasticity).
- Von Mises Stress: For ductile materials, compute the Von Mises stress to assess the yield criteria. This scalar value helps in determining the likelihood of yielding or failure.
- Stress Contours: Generate contour plots for various stress components (e.g., normal stress, shear stress, principal stresses) to identify stress concentration areas, which are critical for failure analysis.
4. Assessing Reaction Forces:
- Reaction Forces and Moments: Calculate the reaction forces and moments at the supports and boundaries. These are essential for ensuring that the applied loads and boundary conditions are correctly implemented and balanced.
- Equilibrium Check: Verify that the sum of all reaction forces and moments equals the sum of the applied external forces and moments, ensuring equilibrium and the correctness of the simulation.
5. Identifying Critical Regions:
- Stress Concentration: Identify regions with high-stress concentrations, which are potential sites for crack initiation or failure. This information is crucial for design improvements and ensuring safety.
- Deformation Zones: Highlight areas with significant deformation that may affect the functionality or aesthetics of the structure or component.
6. Validating Results:
- Comparative Analysis: Compare the FEA results with experimental data or analytical solutions to validate the model. This step is essential to ensure the accuracy and reliability of the simulation.
- Error Estimation: Evaluate the error in the numerical solution, especially in critical regions. Use techniques such as mesh refinement studies and convergence analysis to estimate and minimize errors.
7. Reporting and Documentation:
- Summary of Findings: Document the key findings of the analysis, including maximum displacements, critical stress regions, and potential failure points. Summarize the implications for design and safety.
- Visual Aids: Include visual aids such as deformation plots, stress and strain contours, and graphs to clearly present the results. These aids help in communicating the analysis outcomes to stakeholders.
8. Optimization and Design Improvements:
- Design Iteration: Use the insights gained from the FEA results to make informed decisions on design modifications and optimizations. For instance, reducing stress concentrations by modifying geometry or material properties.
- Sensitivity Analysis: Perform sensitivity analysis to understand how changes in design parameters affect the performance and reliability of the system. This helps in identifying critical parameters that need precise control.
9. Further Analysis:
- Dynamic Analysis: If applicable, extend the analysis to dynamic simulations to study the behavior under time-varying loads. This includes modal analysis, transient dynamic analysis, and harmonic response analysis.
- Thermal and Fluid Analysis: For coupled problems, analyze the thermal and fluid behavior in addition to structural analysis. This involves evaluating temperature distributions, heat fluxes, and fluid flow characteristics.
By effectively post-processing the results, you can gain deep insights into the physical behavior of the system, validate the simulation model, and make informed decisions to enhance design and performance. This step ensures that the numerical predictions are not only accurate but also practical and useful for real-world applications.
Tips for Success in FEA
Finite Element Analysis (FEA) is a powerful tool for solving complex engineering problems, but its accuracy and effectiveness depend on proper application and understanding. Here are some tips to ensure success in your FEA projects:
1. Understand the Physics:
- Comprehensive Knowledge: Make sure you have a solid understanding of the physical principles governing your problem, whether it's structural mechanics, fluid dynamics, or thermal analysis. Knowing the underlying physics helps in setting up the problem correctly and interpreting the results accurately.
- Material Properties: Ensure that you have accurate material properties for your analysis. Incorrect material data can lead to significant errors in the results.
2. Define Clear Objectives:
- Specific Goals: Clearly define what you want to achieve with your FEA. Are you looking to determine stress distributions, predict failure, or optimize a design? Having specific objectives helps in focusing your efforts and setting up the simulation appropriately.
- Scope and Assumptions: Clearly outline the scope of your analysis and any assumptions made. This includes simplifications in geometry, boundary conditions, and loading scenarios.
3. Simplify the Model:
- Geometry Simplification: Simplify the geometry of your model where possible. Remove unnecessary details that do not significantly affect the results but can increase computational complexity.
- Symmetry and Boundary Conditions: Use symmetry and appropriate boundary conditions to reduce the size of the model and computational effort.
4. Mesh Quality:
- Mesh Density: Ensure that the mesh is fine enough to capture important details but not too dense to make computations infeasible. Use a finer mesh in areas with high gradients (e.g., stress concentrations) and a coarser mesh in less critical areas.
- Element Quality: Use high-quality elements to avoid numerical inaccuracies. Poorly shaped elements can lead to convergence issues and erroneous results.
5. Verify Boundary Conditions:
- Correct Implementation: Ensure that boundary conditions are correctly implemented and reflect the real-world constraints and loads. Incorrect boundary conditions can lead to unrealistic results.
- Check Equilibrium: Verify that the sum of the applied loads and reactions is in equilibrium. This helps in detecting any issues with the boundary conditions or load application.
6. Run Convergence Studies:
- Mesh Convergence: Perform mesh convergence studies to ensure that the results are independent of the mesh size. Gradually refine the mesh and check if the results converge to a stable solution.
- Time Step Convergence: For transient problems, conduct time step convergence studies to ensure that the results are independent of the time step size.
7. Use Appropriate Solvers:
- Solver Selection: Choose the appropriate solver for your problem type. Direct solvers are robust and accurate but can be computationally expensive for large problems. Iterative solvers are more efficient for large, sparse systems.
- Solver Settings: Fine-tune solver settings such as convergence criteria, preconditioning, and tolerances to balance accuracy and computational efficiency.
8. Validate the Model:
- Comparison with Experiments: Validate your FEA results by comparing them with experimental data or analytical solutions. This helps in ensuring the accuracy and reliability of the simulation.
- Sensitivity Analysis: Conduct sensitivity analysis to understand how changes in model parameters affect the results. This helps in identifying critical parameters and improving model robustness.
9. Interpret Results Carefully:
- Physical Plausibility: Always check if the results make physical sense. Look for any unrealistic deformations, stresses, or other quantities that could indicate issues with the model setup or boundary conditions.
- Detailed Analysis: Analyze the results in detail to gain insights into the behavior of the system. Look for stress concentrations, deformation patterns, and other critical features.
10. Continuous Learning:
- Stay Updated: FEA software and techniques are constantly evolving. Stay updated with the latest developments, best practices, and software capabilities.
- Training and Workshops: Attend training sessions, workshops, and webinars to enhance your FEA skills and knowledge.
11. Documentation and Reporting:
- Comprehensive Documentation: Document all aspects of your FEA project, including model setup, assumptions, boundary conditions, material properties, and results. This ensures transparency and facilitates future reference.
- Clear Reporting: Present your findings clearly and concisely. Use visual aids such as plots, charts, and diagrams to effectively communicate the results and insights.
By following these tips, you can enhance the accuracy, efficiency, and reliability of your FEA simulations, ensuring successful outcomes for your engineering projects.
Conclusion
Finite Element Analysis (FEA) stands as a cornerstone in modern engineering, offering unparalleled capabilities to simulate and predict the behavior of complex systems under various physical conditions. It merges computational techniques with fundamental principles of physics and mathematics, enabling engineers to solve intricate problems in structural mechanics, fluid dynamics, thermal analysis, and beyond.
At its core, successful FEA requires a multifaceted approach. It begins with a profound understanding of the physical phenomena governing the problem at hand. Engineers must grasp the intricacies of material properties, loading scenarios, and boundary conditions to accurately represent real-world behaviors within the virtual model.
Modeling in FEA demands careful consideration of geometric complexities and mesh quality. While simplifying the model where possible to reduce computational burden, engineers must ensure the mesh is refined adequately to capture critical details without sacrificing computational efficiency. This delicate balance ensures that the simulation accurately reflects the system's response to applied forces and environmental conditions.
The accuracy of FEA hinges on the precise implementation of boundary conditions and loadings. Errors in specifying these parameters can propagate through the analysis, leading to misleading results. Therefore, meticulous attention to detail during setup is imperative to validate the integrity of the model and the reliability of subsequent findings.
Verification and validation serve as pillars of confidence in FEA. Engineers continually benchmark results against analytical solutions, empirical data, or industry standards to ensure the accuracy and fidelity of their simulations. Sensitivity analyses further enhance understanding by exploring how variations in parameters influence outcomes, offering insights into system behavior under different conditions.
Post-processing of results transforms raw data into actionable insights. Visualizing deformations, stress distributions, and other key metrics provides a comprehensive view of structural integrity, potential failure points, and performance optimization opportunities. Clear and concise reporting of findings facilitates informed decision-making and enhances communication across multidisciplinary teams.
Continuous learning and adaptation are essential in the evolving landscape of FEA. Engineers stay abreast of advancements in simulation techniques, software capabilities, and industry best practices through ongoing education, professional development, and collaboration with peers and experts.
In essence, mastering Finite Element Analysis empowers engineers to tackle complex engineering challenges with confidence and precision. By leveraging the full potential of FEA, engineers can innovate, optimize designs, mitigate risks, and ultimately deliver safer, more efficient, and sustainable solutions in a wide range of engineering applications.