Key Assignment Topics in CREO CAD that All Mechanical Engineering Students Should Know
.webp)
In the dynamic world of mechanical engineering, the utilization of Computer-Aided Design (CAD) software has revolutionized the design, analysis, and manufacturing processes. Among the prominent CAD tools, CREO CAD stands out as a versatile and powerful solution that empowers engineers and designers to create intricate and innovative designs. As mechanical engineering students embark on their journey with CREO CAD, they encounter a diverse array of topics and assignments that challenge their skills, ignite their creativity, and enhance their knowledge. This blog delves into the essential topics within CREO CAD for which university assignments are commonly designated, highlighting the distinct types of assignments associated with each topic. Whether it's 3D modeling, simulation, or assembly design, seeking help with your CREO CAD assignment can provide you with valuable insights and guidance for successful completion.
1. Sketching and Basic Geometry Creation
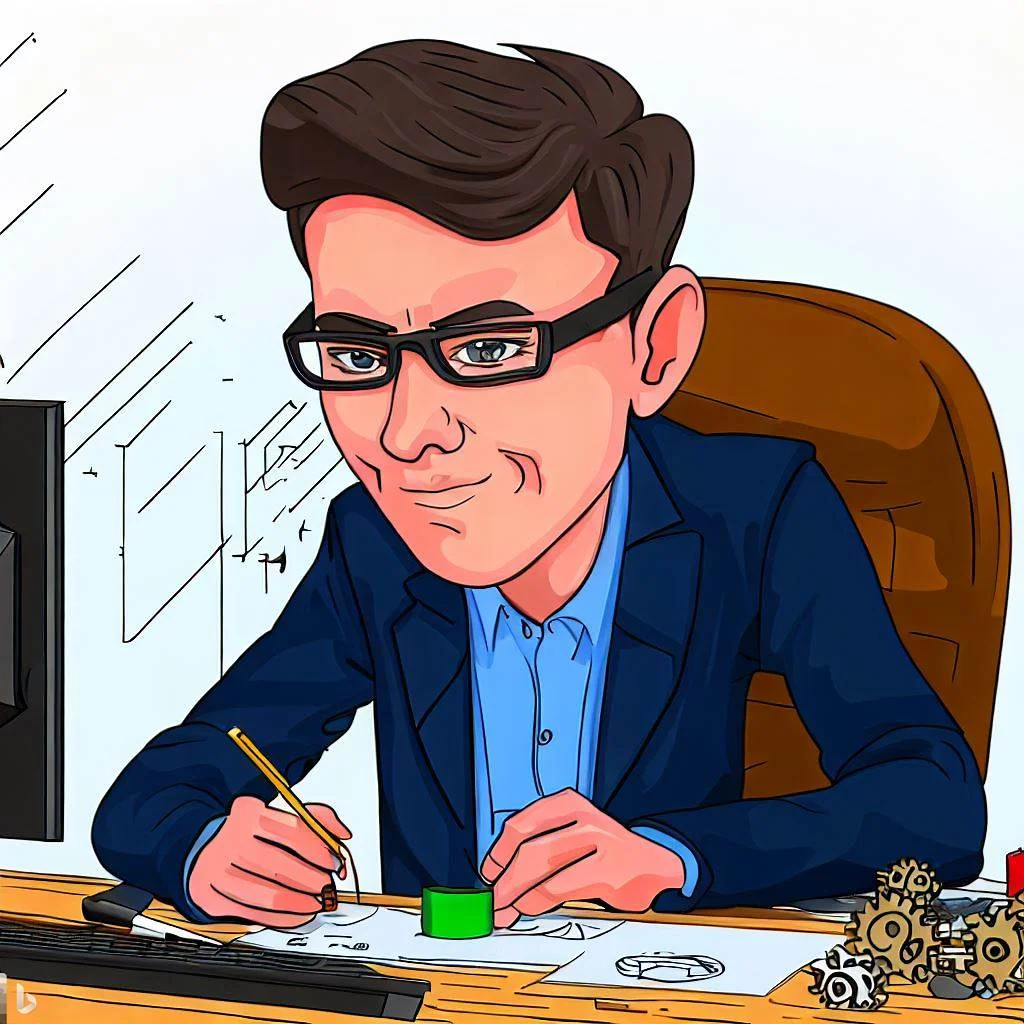
Mastering the art of sketching is fundamental to translating design concepts into a digital realm. Basic geometry creation forms the cornerstone of any CAD endeavor, requiring precision, attention to detail, and a solid understanding of sketch constraints. Assignments under this category focus on developing fundamental skills and familiarity with sketching tools.
Common Assignments
Orthographic Sketching:Orthographic sketching is the cornerstone of design communication, enabling engineers to convey their ideas accurately and comprehensively. In this assignment, students undertake the task of crafting precise 2D sketches of mechanical components from various viewpoints. The emphasis here lies not only in capturing the visual representation of the component but also in conveying dimensioning and geometrical accuracy. By mastering orthographic sketching, students develop a visual language that bridges the gap between concepts and tangible designs, preparing them to effectively communicate their ideas in the professional realm.
Constraint Proficiency:The ability to impose constraints on sketches is pivotal in achieving controlled and well-defined designs. In the constraint proficiency assignment, students delve into the world of geometric constraints, mastering their application to achieve desired sketch layouts. Constraints like coincident, parallel, and perpendicular become tools that guide the sketch towards specific geometric relationships. By successfully applying these constraints, students demonstrate their aptitude for transforming abstract concepts into structured, purposeful sketches. This skill empowers students to create designs that adhere to engineering principles while maintaining the flexibility to adapt to evolving requirements.
Parametric Design Exploration:Parametric design lies at the heart of modern engineering, enabling dynamic modification and adaptation of designs. In the parametric design exploration assignment, students embark on a journey of creation and experimentation. They begin by constructing a parametric model of a basic shape, setting the stage for exploration. By altering dimensions and parameters, students observe the effects of these changes on the design, fostering an intuitive understanding of how modifications influence the final product. This assignment nurtures students' ability to anticipate design variations and empowers them to iteratively refine and optimize their creations. Through parametric design exploration, students not only gain proficiency in a fundamental aspect of modern engineering but also cultivate a mindset of continuous improvement and adaptability.
2. Part Modeling and Parametric Design
The realm of part modeling allows students to construct intricate 3D models using parametric techniques. These models serve as the foundation for more complex assemblies and systems. Assignments in this category prompt students to unravel the complexities of parametric design, employing a strategic approach to feature creation and modification.
Common Assignments
Feature-Based Component Design:In the realm of feature-based component design, students embark on a journey that melds creativity with engineering precision. This assignment revolves around crafting mechanical components by seamlessly integrating a range of features, such as extrusions, revolves, chamfers, and fillets. However, the true art lies in ensuring that each feature serves a purpose and contributes harmoniously to the overall design intent. This task challenges students to think critically about how each feature enhances the component's functionality, manufacturability, and aesthetics. By mastering feature-based design, students showcase their ability to create components that are not only visually appealing but also optimized for real-world applications.
Parametric Modification Challenge:The ability to modify existing designs while preserving functionality and structural integrity is a hallmark of adept engineering. In the parametric modification challenge, students face a practical exercise where they must revise the dimensions of an established part model. The key lies in conducting these modifications meticulously, avoiding errors or inconsistencies that could compromise the design's performance. This assignment hones students' attention to detail and understanding of the intricate relationships between dimensions, features, and constraints. By successfully completing this challenge, students demonstrate their proficiency in parametric modeling and their capacity to adapt designs to evolving requirements without sacrificing quality.
Assembly-Ready Components:The backbone of any mechanical system lies in its assembly, and designing components that seamlessly integrate into an assembly is a skill of paramount importance. In the assembly-ready components assignment, students engineer parts with a keen focus on proper mating surfaces and efficient parametric relationships. Each part is meticulously crafted to ensure optimal fit, alignment, and functionality when integrated into a larger assembly. This task requires a deep understanding of how components interact, highlighting the significance of standardized interfaces and precise parametric connections. By excelling in this assignment, students showcase their ability to design with a systems-oriented mindset, contributing to the overall success of complex mechanical assemblies.>
3. Assembly Modeling and Mechanisms
Assembly modeling introduces students to the intricacies of combining multiple parts to form functional mechanical systems. The focus shifts from individual components to the dynamic interactions between them. Assignments here delve into the dynamics of motion and proper component interplay.
Common Assignments
Functional Mechanical Assembly:Creating a functional mechanical assembly that replicates a real-world mechanism, such as a gear train or lever system, requires a nuanced understanding of how individual parts interact to achieve specific functions. In this assignment, students embark on a journey to translate theoretical principles into practical designs. The emphasis on precise mating conditions ensures that components fit seamlessly, mirroring the precision demanded by actual machinery. Accurate motion simulation further enhances the realism of the assembly, allowing students to visualize how forces and interactions play out in a dynamic environment. By successfully completing this assignment, students not only demonstrate their grasp of engineering fundamentals but also showcase their ability to engineer practical solutions with real-world applicability.
Kinematic Analysis:Kinematics forms the backbone of mechanical engineering design, governing the motion and behavior of mechanisms. When students undertake kinematic analysis, they employ a range of constraints and mates to simulate the motion of an assembly. This assignment emphasizes the significance of kinematics in engineering design by enabling students to observe how various components move, interact, and transmit forces. By meticulously configuring constraints, students gain insight into how mechanisms respond to input motion, aiding in the identification of potential issues and the optimization of designs. Kinematic analysis transforms abstract design concepts into tangible insights, empowering students to make informed decisions that lead to functional and efficient mechanical systems.
Interchangeable Component Assembly:The concept of interchangeability lies at the heart of efficient manufacturing and maintenance processes. Developing an assembly comprised of interchangeable parts challenges students to design with modularity in mind. This assignment underscores the importance of standardized designs and modular components, promoting streamlined production and simplified maintenance procedures. By crafting an assembly where components seamlessly swap without compromising functionality, students grasp the significance of designing for manufacturability and ease of maintenance. This task nurtures skills in modular design, encouraging students to envision products that can adapt to changing requirements, minimize downtime, and enhance overall system efficiency.
4. Surface Modeling and Complex Shapes
Surface modeling provides a pathway for tackling intricate shapes and forms that cannot be fully encapsulated by traditional solid models. This category pushes students to embrace creativity and stretch the boundaries of design possibilities.
Common Assignments
Organic Shape Design: When tasked with fabricating a consumer product characterized by fluid and organic contours, students are embarking on a journey that pushes the boundaries of creativity and engineering prowess. Organic shapes often emulate forms found in nature, evoking a sense of elegance and sophistication. However, creating such shapes requires a delicate balance between aesthetics and manufacturability.
Students must employ advanced surface modeling techniques to sculpt these intricate shapes. They delve into tools that allow for the manipulation of curves, surfaces, and control points to craft a design that is not only visually appealing but also structurally sound. Achieving manufacturability involves considering factors like material properties, molding processes, and potential challenges in production.
In this assignment, students navigate challenges such as maintaining consistent wall thickness, ensuring proper draft angles, and avoiding sharp corners that could hinder mold release. The outcome showcases their ability to merge artistry with engineering acumen, resulting in a design that seamlessly blends aesthetic allure with real-world functionality.
Hybrid Solid-Surface Integration: The world of design rarely adheres to strict boundaries between solid and surface modeling techniques. Instead, students often encounter scenarios where combining these approaches leads to the most effective and efficient designs. In this assignment, students embark on a journey to create a design that seamlessly merges solid and surface features, celebrating the harmonious coexistence of different modeling techniques.
Students must identify where each technique is best suited and how they can complement each other. For instance, using solid modeling for structurally vital components and surface modeling for intricate, curvilinear surfaces. This exercise necessitates a deep understanding of both approaches and the ability to transition seamlessly between them.
The challenge lies not only in creating a coherent design but also in ensuring smooth transitions between solid and surface elements. These transitions demand meticulous attention to detail, as they influence aesthetics, strength, and manufacturability. By successfully integrating these techniques, students showcase their ability to navigate the complexities of modern design and create innovative solutions that push the boundaries of traditional approaches.
Curvature Continuity Showcase: Designing a model that emphasizes curvature continuity underscores the essence of high-quality design - the seamless flow of surfaces without abrupt changes or irregularities. In this assignment, students are tasked with constructing a model that demonstrates the art of curvature continuity, highlighting the importance of smooth transitions between surfaces.
Curvature continuity, often referred to as G2 continuity, involves ensuring that adjacent surfaces have matching curvatures at their common boundary. This meticulous attention to detail enhances not only aesthetics but also the tactile experience of the final product. Achieving curvature continuity is crucial for products that demand superior quality, such as automotive body panels, consumer electronics, and medical devices.
Through this assignment, students must exhibit mastery of advanced surface modeling techniques, as well as a profound understanding of curvature analysis tools. They navigate the complexities of curvature combs, curvature plots, and curvature maps to ensure that their model exemplifies the desired level of smoothness. By successfully showcasing curvature continuity, students demonstrate their commitment to excellence in design and their ability to deliver products of the highest caliber.
5. Drafting and Documentation:
Clear and concise documentation is the linchpin that communicates design intent and specifications to various stakeholders. In this section, students learn the art of creating engineering drawings that convey critical information effectively.
Common Assignments:
Comprehensive Engineering Drawings:Producing comprehensive engineering drawings is a pivotal skill for mechanical engineers, as these drawings serve as a bridge between conceptual design and actual fabrication. When assigned a task involving creating a complete set of engineering drawings for a given 3D model, students are required to delve into the world of standards, conventions, and meticulous detailing.
Creating these drawings involves multiple stages. First, the 3D model is meticulously inspected to identify each feature, component, and part that needs to be represented on paper. Once the components are identified, students need to apply various annotations, dimensions, and notation to accurately convey the design intent. This includes labeling each component, specifying dimensions for critical features, and indicating tolerances and material specifications.
Adhering to industry standards and conventions is paramount in this task. Students must ensure that their drawings follow recognized symbols, line types, and notation rules. These standards not only enhance the clarity of the drawing but also ensure that anyone familiar with engineering drawings can easily interpret the information presented.
Detailed Assembly Drawings:Detailing a complex assembly through annotated and dimensioned drawings is a challenge that goes beyond merely illustrating the physical arrangement of parts. These drawings serve as a roadmap for manufacturers, assemblers, and quality control teams to understand how each part fits together, interacts, and contributes to the functionality of the whole system.
When tasked with annotating and dimensioning a complex assembly, students are expected to display a deep understanding of the components' interrelationships. This involves accurately placing dimensions, annotations, and labels that clearly depict how parts align, connect, and interface with one another. The goal is to make the assembly process smooth, highlighting features that require careful alignment or precise fits.
Effective organization is key in detailed assembly drawings. Students must present information in a logical sequence, allowing viewers to follow the assembly process step by step. This often includes exploded views, where components are shown in disassembled positions to illustrate how they come together. These drawings aim to minimize ambiguity, reduce errors, and optimize the assembly workflow.
Exploded Views and Instructions:Crafting exploded views and assembly instructions brings the mechanical design to life in a tangible and actionable manner. In this assignment, students not only need to visualize how parts fit together but also communicate this knowledge to others who will assemble the final product.
Exploded views offer a visual representation of the assembly's disassembled state, showing how each component relates to others. Students need to consider the spatial relationships, arrangement, and order of assembly. This requires a deep understanding of the design's mechanical logic, as well as the ability to foresee potential challenges during the assembly process.
Accompanying these exploded views are assembly instructions that guide assemblers through the process. Clear and concise instructions are vital to avoid confusion, reduce errors, and enhance efficiency. Students need to describe each step in a logical sequence, while also addressing potential obstacles and offering solutions. This assignment not only tests their technical knowledge but also their communication skills, as the clarity of the instructions directly impacts the ease of assembly.
Conclusion
CREO CAD serves as an invaluable canvas upon which mechanical engineering students paint their creative and technical mastery. By engaging with a diverse array of assignments that span sketching, part modeling, assembly creation, surface design, and drafting, students cultivate essential skills, broaden their horizons, and solidify their understanding of design principles. With each assignment completed, students inch closer to their goals of becoming adept engineers capable of envisioning, creating, and optimizing the machines and systems that shape our world. As these students evolve into seasoned professionals, they contribute to the ongoing advancement of technology and innovation within the realm of mechanical engineering.