A Comprehensive Guide to 5 Technical CATIA Assignment Topics for University Students
.webp)
CATIA (Computer-Aided Three-Dimensional Interactive Application) is a powerful software suite widely used in the field of mechanical engineering for designing, analyzing, and simulating various products. As part of their coursework, students pursuing mechanical engineering often encounter CATIA assignments that test their skills and understanding of the software's functionalities. In this blog post, we will delve into the different topics covered in CATIA assignments at the university level and discuss the types of assignments students can expect to encounter, potentially seeking assistance with your CATIA assignment to ensure you approach them with confidence and achieve successful outcomes.
1. Sketching and Part Modeling
One of the fundamental aspects of CATIA is sketching and part modeling. Assignments in this category often require students to create 2D sketches and then transform them into 3D models using various tools and features. These assignments may involve creating simple geometric shapes, complex mechanical components, or even assemblies of parts. Some common types of sketching and part modeling assignments include:
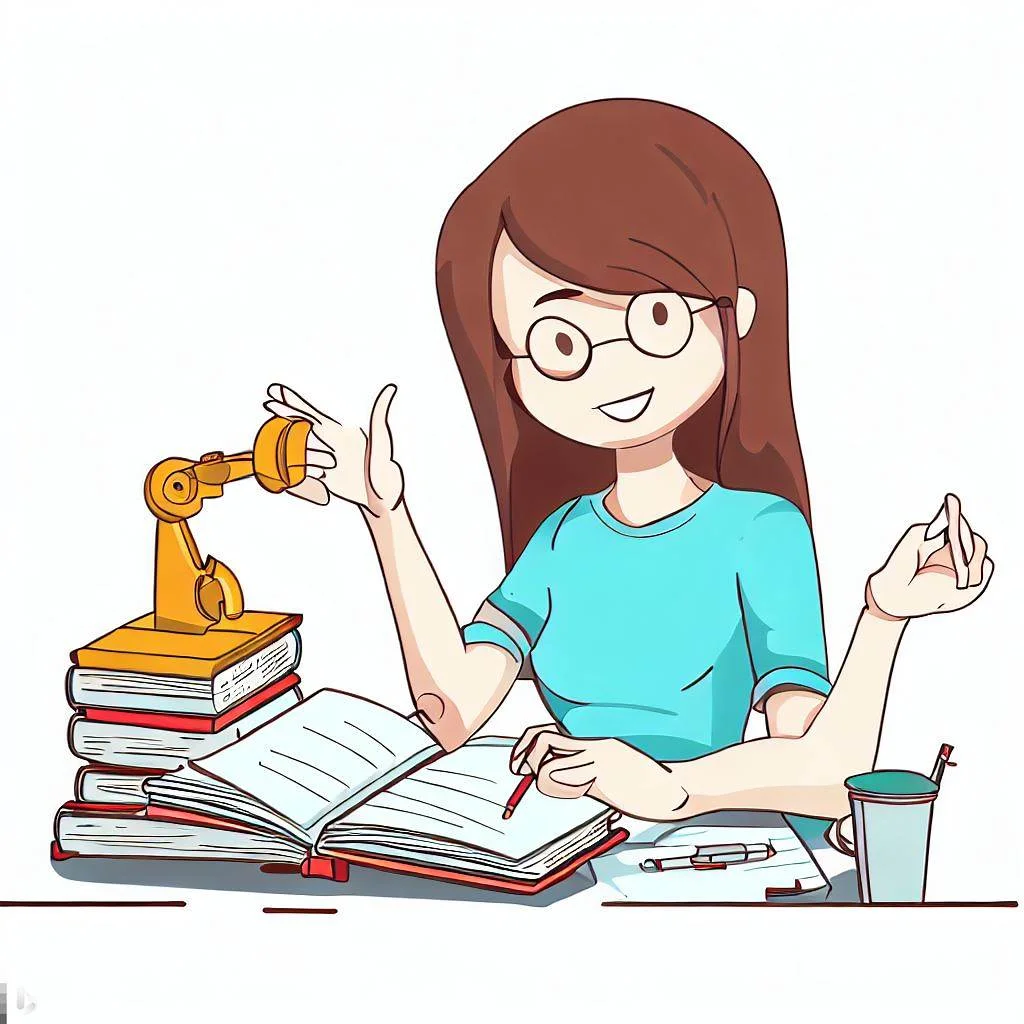
a. Basic Geometric Shapes: Students might be tasked with creating 3D models of basic geometric shapes such as cubes, cylinders, spheres, and cones. These assignments help students become familiar with CATIA's sketching tools and extrusion features.
b. Mechanical Components: Assignments can become more intricate by challenging students to design mechanical components like gears, screws, bolts, and hinges. These assignments focus on refining part modeling skills and understanding the importance of accurate measurements.
c. Assembly Modeling: Assembly assignments involve creating an assembly of multiple parts that fit together seamlessly. Students are expected to understand constraints, joints, and relationships between components.
2. Surface Modeling
Surface modeling is essential for industries where design intricacy and aesthetics are paramount, such as consumer electronics, automotive, aerospace, and industrial design. CATIA's surface modeling capabilities offer several advantages:
1. Complex Geometries: Surface modeling allows engineers to create freeform and complex geometries that are not achievable through traditional solid modeling methods.
2. Aesthetics: Engineers can design visually appealing and ergonomic products with smooth curves and flowing surfaces, enhancing the overall look and feel of a design.
3. Aerodynamics: Surface modeling is crucial in industries like aerospace, where streamlined and aerodynamic shapes are essential for reducing drag and optimizing performance.
4. Prototyping and Visualization: Surface models facilitate rapid prototyping and visualization, enabling designers to visualize and test their concepts early in the design process.
5. Innovative Design: Engineers can explore innovative design concepts and push the boundaries of traditional design constraints.
Examples of Assignments
a. Aesthetic Product Design
Assignments in aesthetic product design challenge students to create visually appealing and user-friendly consumer products using CATIA's surface modeling tools. These assignments emphasize the importance of form, ergonomics, and attention to detail. Here's an example of an aesthetic product design assignment:
Assignment Scenario: Design a futuristic, ergonomic computer mouse that combines aesthetics and functionality. The mouse should be comfortable to hold and visually captivating.
Tasks:
1. Concept Sketching: Students begin by sketching out different design concepts for the computer mouse, considering factors such as grip, button placement, and overall form.
2. Surface Modeling: Using CATIA's surface modeling tools, students create a 3D model of the computer mouse, focusing on achieving smooth and organic curves.
3. Ergonomic Evaluation: Students evaluate the ergonomics of the design, ensuring that the mouse fits comfortably in the hand and promotes natural movement.
4. Material and Texture Application: Students apply appropriate materials and textures to the surface model to visualize how the mouse would look in real-world conditions.
5. Presentation: Students prepare a presentation showcasing their design process, concept sketches, 3D model, and rationale behind their design choices.
b. Aerospace Components
Surface modeling is crucial in aerospace engineering for creating streamlined and aerodynamic components. Assignments in this category challenge students to design aerospace components that optimize performance and reduce drag. Here's an example of an aerospace components assignment:
Assignment Scenario: Design a streamlined winglet for an aircraft that enhances fuel efficiency by reducing drag and improving aerodynamics.
Tasks:
a. Aerodynamic Analysis: Students analyze the aircraft's current wing design and identify areas for improvement in terms of drag reduction.
b. Surface Modeling: Using CATIA's advanced surface modeling tools, students design a winglet that seamlessly integrates with the existing wing structure and reduces airflow disturbances.
c. Aerodynamic Simulations: Students use CATIA's simulation capabilities to perform aerodynamic simulations, analyzing how the new winglet design affects airflow and drag.
d. Optimization: Based on simulation results, students iterate on the winglet design, adjusting curvature and surface features to further enhance aerodynamic performance.
e. Visualization and Presentation: Students present their final design, showcasing simulations, aerodynamic improvements, and the overall impact on aircraft performance.
3. Generative Shape Design
Generative Shape Design is a critical tool for engineers and designers seeking to push the boundaries of conventional design. It offers a range of advanced tools and features that enable the creation of highly complex and aesthetically pleasing shapes. Some key benefits of Generative Shape Design in CATIA include:
1. Innovative Design: Engineers can unleash their creativity and explore innovative design concepts that go beyond traditional geometric forms.
2. Organic and Curved Surfaces: Generative Shape Design is particularly suited for creating smooth, organic, and curved surfaces that are challenging to achieve with standard modeling techniques.
3. Aesthetic Appeal: The module allows for the creation of visually appealing and artistic designs that can make products stand out in competitive markets.
4. Prototyping and Visualization: Generative Shape Design aids in rapid prototyping and visualization, allowing designers to quickly translate their ideas into tangible 3D models.
5. Complex Geometry: Engineers can model complex and intricate geometries that are often required in industries such as aerospace, automotive, and consumer electronics.
Examples of Assignments
a. Organic Shape Creation
Assignments in organic shape creation challenge students to think creatively and translate natural forms and inspirations into digital designs. This type of assignment encourages students to explore the capabilities of Generative Shape Design while focusing on artistic expression and aesthetics. Here's an example of an organic shape creation assignment:
Assignment Scenario: Design a decorative vase inspired by the flowing lines and contours of ocean waves. The vase should be visually striking and emphasize the seamless transition between waves.
Tasks:
1. Concept Exploration: Students research and gather visual references of ocean waves, understanding the unique shapes and curves that define them.
2. Generative Shape Design: Using CATIA's Generative Shape Design tools, students create a 3D model of the vase, focusing on capturing the fluid and organic nature of waves.
3. Surface Refinement: Students refine the surfaces of the vase, ensuring smooth transitions between wave-like elements and addressing any potential imperfections.
4. Visualization: Students apply materials and textures to the model to visualize how the vase would appear in different lighting conditions.
5. Presentation: Students prepare a presentation showcasing the design process, inspirations, and the final 3D model of the ocean-inspired vase.
b. Custom Tools and Accessories
Generative Shape Design can also be applied to designing custom tools, machine parts, or accessories with intricate and unconventional geometries. These assignments challenge students to create functional yet visually appealing components that exhibit advanced design techniques. Here's an example of a custom tools and accessories assignment:
Assignment Scenario: Design a custom ergonomic handle for a handheld power tool, optimizing comfort and grip for prolonged use.
Tasks:
a. Ergonomic Analysis: Students analyze ergonomic principles and user requirements to determine the optimal shape and contours for the handle.
b. Generative Shape Design: Using CATIA's advanced tools, students design the custom handle, considering factors such as hand placement, grip angles, and material properties.
c. Functional Integration: Students ensure that the handle seamlessly integrates with the existing power tool, allowing for easy attachment and use.
d. Surface Optimization: Students refine the handle's surfaces to ensure a comfortable and tactile grip, considering factors like texture and tactile feedback.
e. Prototyping and Testing: Students may create a physical prototype of the handle using 3D printing or other rapid prototyping methods to assess its comfort and usability.
4. Sheet Metal Design
Sheet metal design is a critical aspect of mechanical engineering, particularly in industries where lightweight yet durable components are essential, such as aerospace, automotive, electronics, and construction. CATIA's sheet metal design tools provide engineers with the capability to:
1. Create Complex Shapes: Engineers can design intricate and geometrically complex shapes using sheet metal, enabling the creation of functional and aesthetically pleasing components.
2. Optimize Material Usage: Sheet metal design tools allow for efficient nesting of components on metal sheets, minimizing material wastage during manufacturing.
3. Accurate Manufacturing: CATIA's unfolding features ensure that sheet metal components can be accurately manufactured, bent, and formed to match the intended design.
4. Consider Manufacturing Constraints: Engineers can design components while considering manufacturing constraints, such as bend radii, minimum flange lengths, and hole distances.
5. Rapid Prototyping: Sheet metal designs can be quickly prototyped and tested, facilitating the iterative design process.
Examples of Assignments
a. Sheet Metal Enclosures
Sheet metal enclosures are widely used to protect and house electronic devices, ensuring their functionality and safeguarding them from external elements. Assignments in this category challenge students to design sheet metal enclosures for electronic devices while considering factors crucial to successful manufacturing. Here's an example of a sheet metal enclosure assignment:
Assignment Scenario: Design a sheet metal enclosure for a handheld electronic device, such as a tablet or smartphone. The enclosure should meet structural requirements, accommodate internal components, and adhere to manufacturing guidelines.
Tasks:
1. Component Layout: Students create a 3D model of the electronic device, considering the arrangement of internal components such as the display, battery, and circuit board.
2. Enclosure Design: Using CATIA's sheet metal design tools, students design the outer shell of the enclosure, considering factors like material thickness, bend radii, and allowances for hinges or openings.
3. Bend and Flange Definition: Students define bends and flanges in the sheet metal, ensuring that the enclosure can be accurately manufactured and assembled.
4. Unfolding and Manufacturing Considerations: Students use CATIA's unfolding features to generate a 2D flat pattern of the enclosure. They verify that the unfolded geometry adheres to manufacturing constraints and can be efficiently produced.
5. Prototype Visualization: Students visualize a prototype of the unfolded enclosure, identifying any potential issues or interferences that may arise during manufacturing or assembly.
b. Ducts and HVAC Components
In the construction industry, sheet metal is extensively used for creating ducts and components in heating, ventilation, and air conditioning (HVAC) systems. Assignments in this category require students to design ducts or HVAC components that meet specific airflow and spatial requirements. Here's an example of a duct design assignment:
Assignment Scenario: Design a sheet metal duct for an HVAC system in a commercial building. The duct should efficiently distribute airflow while fitting within space constraints.
Tasks:
1. System Understanding: Students familiarize themselves with the building's HVAC requirements, including airflow rates, pressure drops, and space limitations.
2. Duct Geometry: Using CATIA's sheet metal design tools, students create the 3D geometry of the duct, considering the path of airflow and any necessary bends or transitions.
3. Flange and Connection Design: Students design flanges and connections for joining the duct to other HVAC components, ensuring airtight seals and efficient assembly.
4. Unfolding and Fabrication: Students unfold the duct's geometry using CATIA, generating a flat pattern that can be easily manufactured from a sheet of metal.
5. Flow Simulation: Students use CATIA's simulation capabilities to analyze the airflow through the duct, ensuring that it meets the required performance specifications.
5. Kinematics and Simulation
Kinematics is the study of motion without considering the forces that cause it. It plays a crucial role in mechanical design by enabling engineers to understand how components move relative to each other within a mechanical system. Simulation, on the other hand, involves creating a virtual model of a system and observing its behavior under different conditions. Together, kinematics and simulation help engineers:
1. Optimize Design: By simulating the motion of a mechanical assembly, engineers can identify potential design flaws or interferences before manufacturing. This helps in minimizing costly errors and streamlining the design process.
2. Evaluate Performance: Kinematic and dynamic simulations allow engineers to assess the performance of a system, such as its speed, acceleration, and range of motion. This is crucial for ensuring that the final product meets desired specifications.
3. Iterative Design: Engineers can iterate and refine their designs based on simulation results, leading to more innovative and efficient solutions.
4. Education and Training: Kinematics and simulation assignments provide students with hands-on experience in applying theoretical concepts to real-world scenarios, preparing them for future engineering challenges.
Examples of Assignments
a. Mechanical Assemblies
In CATIA assignments focusing on mechanical assemblies, students are presented with the task of creating and simulating complex systems composed of interconnected components. This assignment type challenges students to apply their knowledge of joints, constraints, and motion sequences. Here's how such an assignment might unfold:
Assignment Scenario: Design a robotic arm with multiple degrees of freedom for a manufacturing process. The arm should be able to perform pick-and-place operations accurately.
Tasks:
1. Component Modeling: Students create individual 3D models of each robotic arm component, considering their shape, dimensions, and interaction points.
2. Assembly Creation: Using CATIA's assembly design tools, students assemble the robotic arm components, defining appropriate joints and constraints to replicate real-world mechanical behavior.
3. Kinematic Analysis: Students set up motion sequences for the robotic arm, simulating its movement through different pick-and-place operations. They analyze joint angles, velocities, and accelerations to ensure smooth and precise motion.
- Performance Evaluation: Based on simulation results, students evaluate the robotic arm's performance, identifying any potential collisions, overextensions, or inefficiencies.
- Optimization: If necessary, students iterate on the design, adjusting joint parameters or component placements to optimize the robotic arm's performance.
b. Motion Analysis
Motion analysis assignments focus on understanding the motion of specific mechanical systems and components. These assignments help students develop an in-depth grasp of kinematic principles and their practical applications. Here's an example of a motion analysis assignment:
Assignment Scenario: Analyze the motion of a four-bar linkage mechanism commonly used in automotive suspension systems.
Tasks:
1. Mechanism Definition: Students create 3D models of the four-bar linkage components, including links and joints, accurately representing their dimensions and connection points.
2. Motion Setup: Using CATIA's motion analysis tools, students define the initial conditions and constraints for the four-bar linkage system. They set the system in motion by specifying input parameters.
3. Trajectory Analysis: Students observe and analyze the trajectory followed by specific points on the four-bar linkage as it undergoes motion. They calculate joint angles, velocities, and accelerations.
4. Dynamic Effects: Students explore dynamic effects such as inertia and gravity, understanding how these factors influence the behavior of the linkage system during motion.
5. Performance Comparison: By varying input parameters, students compare the effects of different motion profiles on the four-bar linkage's performance, such as its range of motion or stability.
Conclusion
CATIA is a versatile software tool that plays a crucial role in the education and practice of mechanical engineering. Assignments in CATIA provide students with hands-on experience in designing, modeling, and simulating various mechanical components and systems. The topics covered in CATIA assignments are diverse and reflect the real-world challenges engineers face in their careers. By successfully completing these assignments, students not only enhance their CATIA skills but also develop a deeper understanding of mechanical engineering principles. As technology continues to advance, CATIA remains an indispensable tool for aspiring mechanical engineers, empowering them to bring their innovative ideas to life.