CFD Analysis in ANSYS Fluent: Strategies for Fluid Flow Problems!
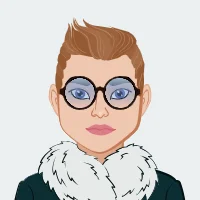
Computational Fluid Dynamics (CFD) stands as an indispensable tool within the realm of mechanical engineering, revolutionizing the way engineers understand and optimize fluid flow phenomena. At its core, CFD leverages numerical methods and algorithms to simulate the behavior of fluids and gases in complex environments. The significance of CFD in mechanical engineering lies in its ability to provide detailed insights into fluid dynamics, enabling engineers to analyze and predict the performance of various systems and components. Whether it's aerodynamics in automotive design, heat transfer in electronic devices, or the optimization of industrial processes involving fluid flow, CFD plays a pivotal role in enhancing efficiency, reducing costs, and ensuring the safety and reliability of engineering solutions. If you need help with your ANSYS assignment, delving into Computational Fluid Dynamics provides students with the necessary skills to utilize ANSYS software effectively, enabling them to simulate and analyze fluid flow phenomena in mechanical engineering applications.
In this context, ANSYS Fluent emerges as a leading and widely adopted CFD software package, offering a sophisticated platform for conducting fluid flow simulations. ANSYS Fluent's role is paramount in translating theoretical concepts into actionable insights. One of its primary strengths lies in its versatility, accommodating a broad spectrum of fluid flow problems encountered in diverse industries. From aerodynamic analyses of aircraft to thermal simulations of electronic devices and intricate multiphase flow scenarios in chemical engineering, ANSYS Fluent proves to be an invaluable tool for engineers seeking comprehensive solutions.
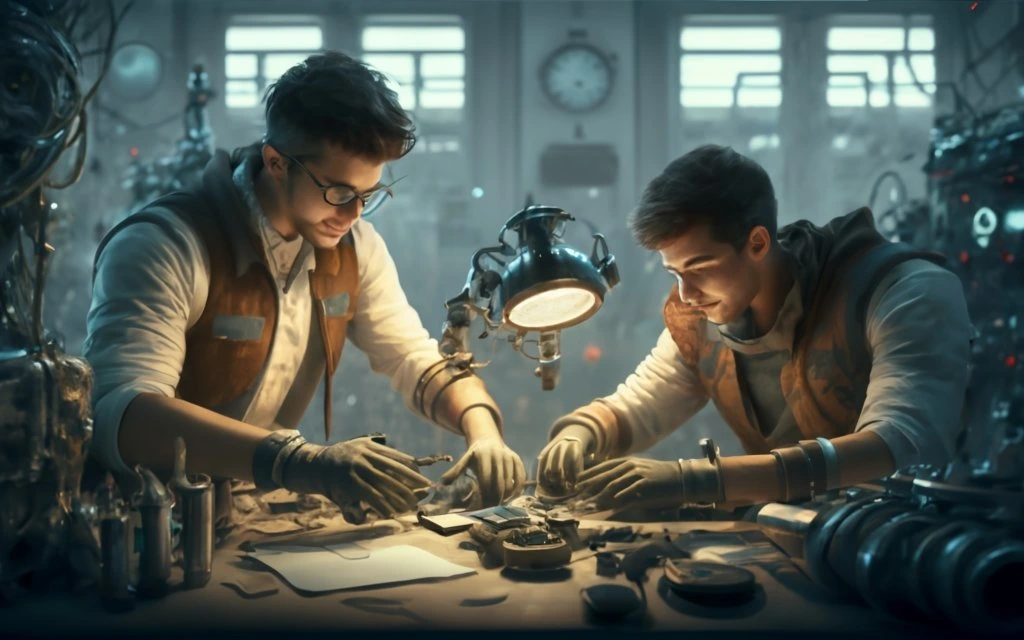
The software's prowess is exemplified in its capability to handle complex geometries, allowing engineers to model real-world scenarios with a high degree of fidelity. The meshing capabilities of ANSYS Fluent facilitate the discretization of these intricate geometries, ensuring accurate and reliable simulations. Moreover, the software provides an extensive array of boundary conditions, allowing users to replicate a wide range of environments and scenarios. This flexibility is crucial in capturing the nuances of different fluid flow problems, enabling engineers to derive meaningful insights that contribute to informed decision-making.
ANSYS Fluent further distinguishes itself through its advanced solver options, providing users with the ability to choose from a variety of turbulence models and numerical schemes. This flexibility is instrumental in tailoring simulations to the specific characteristics of the fluid flow under investigation. Whether simulating laminar flows in microfluidic devices or turbulent flows around industrial structures, ANSYS Fluent empowers engineers to select the most appropriate solver settings, enhancing the accuracy and reliability of their analyses.
Post-processing capabilities within ANSYS Fluent facilitate the extraction and visualization of simulation results. Engineers can explore and interpret a wealth of data, gaining a deeper understanding of fluid flow phenomena. This capacity for detailed post-processing is crucial for extracting actionable insights and refining designs based on simulation outcomes.
Understanding CFD Analysis:
Computational Fluid Dynamics (CFD) is a multidisciplinary field that leverages numerical methods and algorithms to simulate and analyze the behavior of fluid flows. At its core, CFD involves the mathematical modeling of fluid flow phenomena, allowing engineers and scientists to gain insights into complex fluid dynamics scenarios without resorting to expensive and time-consuming physical experiments. The foundational principles of CFD are rooted in the Navier-Stokes equations, which govern the motion of fluid substances. These equations describe the conservation of mass, momentum, and energy in a fluid, forming the basis for understanding and predicting fluid behavior under various conditions.
In mechanical engineering, the importance of fluid flow analysis through CFD cannot be overstated. Fluids, whether liquids or gases, play a pivotal role in numerous engineering applications, and comprehending their behavior is essential for designing efficient and optimal systems. One key application is in the aerodynamic design of vehicles and aircraft. CFD enables engineers to model and assess the airflow around these structures, predicting aerodynamic forces and optimizing designs for improved performance and fuel efficiency. Additionally, in the design of industrial components such as pumps, fans, and heat exchangers, CFD allows for a detailed examination of fluid flow patterns, aiding in the refinement of these devices to enhance efficiency and reduce energy consumption.
Moreover, CFD finds extensive use in the analysis of heat transfer processes. Understanding how fluids transport and dissipate heat is critical in the design of thermal systems, ranging from electronic cooling systems to HVAC (heating, ventilation, and air conditioning) systems. CFD simulations enable engineers to evaluate the effectiveness of heat exchangers, assess thermal management strategies, and optimize designs to prevent overheating issues. In the realm of renewable energy, CFD is instrumental in assessing the performance of wind turbines and predicting the flow patterns within solar collectors, contributing to the advancement of sustainable energy solutions.
In the field of chemical engineering, CFD plays a vital role in simulating and optimizing processes involving fluid flows. Whether it's the mixing of chemicals in reactors or the analysis of multiphase flows in pipelines, CFD aids in understanding the intricate details of these processes, ensuring safety, efficiency, and cost-effectiveness in chemical manufacturing. Additionally, in the biomedical sector, CFD is employed to model blood flow in arteries and simulate airflow in the respiratory system, providing valuable insights for medical device design and healthcare research.
In essence, fluid flow analysis through CFD empowers mechanical engineers to make informed decisions in the design and optimization of a wide array of systems. It enables them to predict and understand fluid behavior under diverse conditions, leading to more efficient designs, reduced development costs, and improved overall performance in engineering applications across various industries. As technology continues to advance, CFD remains a cornerstone in the toolkit of engineers, fostering innovation and pushing the boundaries of what is achievable in the dynamic realm of fluid dynamics.
Overview of ANSYS Fluent:
ANSYS Fluent stands as a flagship software solution in the realm of Computational Fluid Dynamics (CFD), empowering engineers and researchers to simulate and analyze fluid flow, heat transfer, and associated phenomena. With its comprehensive suite of tools and advanced numerical algorithms, ANSYS Fluent has become an indispensable ally for professionals dealing with complex fluid dynamics problems in the field of mechanical engineering.
At its core, ANSYS Fluent is designed to address a wide spectrum of fluid flow scenarios, from simple incompressible flows to intricate multiphase and turbulent flows. The software excels in handling a diverse range of fluid dynamics problems encountered across industries, such as aerospace, automotive, energy, and environmental engineering. Its capabilities extend beyond mere fluid flow simulations, encompassing heat transfer, chemical reactions, and combustion processes. This versatility makes ANSYS Fluent a go-to solution for engineers seeking to gain insights into the behavior of fluids under varying conditions.
One of the standout features of ANSYS Fluent lies in its robust meshing capabilities, allowing users to generate high-quality computational meshes that accurately represent the geometry of the system under investigation. The significance of meshing cannot be overstated, as it directly influences the accuracy and reliability of simulation results. ANSYS Fluent's meshing tools enable users to refine and adapt meshes to capture intricate flow details, ensuring a precise representation of real-world conditions.
Moreover, ANSYS Fluent offers an extensive array of turbulence models, enabling users to simulate the complex nature of turbulent flows encountered in practical engineering applications. This includes models for laminar, transitional, and turbulent flows, providing flexibility to users based on the specific characteristics of their fluid dynamics problems. The software's robust solver options further enhance its adaptability, allowing engineers to choose the most suitable solution method for their simulations.
In addition to its prowess in solving fluid dynamics problems, ANSYS Fluent excels in post-processing capabilities. The software provides a rich set of tools for visualizing and interpreting simulation results, facilitating the extraction of valuable insights. Engineers can analyze flow patterns, temperature distributions, and other critical parameters to make informed decisions in the design and optimization of engineering systems.
In essence, ANSYS Fluent stands as a pinnacle in the world of CFD software, offering a comprehensive platform for tackling the intricacies of fluid dynamics. Its capabilities extend far beyond conventional simulations, making it an indispensable tool for those navigating the challenges of complex fluid flow problems in diverse engineering domains.
Key Steps in CFD Analysis Using ANSYS Fluent:
In the realm of Computational Fluid Dynamics (CFD) analysis using ANSYS Fluent, the initial steps of Geometry and Meshing are paramount. The geometry serves as the foundation for accurate simulations, influencing the fidelity of results. A well-constructed geometry ensures that the computational domain accurately represents the physical system under consideration. Furthermore, the meshing process plays a crucial role in discretizing the geometry into finite elements, impacting simulation accuracy. A refined mesh, with appropriate element sizes and distributions, is essential for capturing intricate flow phenomena and gradients within the fluid domain.
Moving on to Boundary Conditions, their proper definition is fundamental for simulating realistic fluid flow scenarios. The significance lies in accurately representing the physical constraints of the system, influencing the behavior of fluid at boundaries. Examples of common boundary conditions vary with the nature of fluid flow problems. For instance, specifying inlet velocities, pressures, or temperature profiles are standard practices in ensuring a representative simulation environment. Defining suitable boundary conditions is pivotal for obtaining meaningful and applicable CFD results.
Solver Settings represent a critical facet of CFD analysis in ANSYS Fluent. A spectrum of solver options is available, each tailored to address specific types of fluid flow problems. Whether it be steady-state or transient simulations, laminar or turbulent flows, the choice of solver significantly influences computational efficiency and accuracy. Insights into selecting appropriate solver settings involve understanding the physics of the problem, computational resources, and convergence criteria. The judicious choice of solver settings ensures that simulations converge to accurate and reliable solutions.
Post-Processing is the final phase where simulation results come to life. ANSYS Fluent provides a plethora of post-processing tools for visualizing and interpreting simulation outcomes. From contour plots to velocity vectors, these tools aid in extracting valuable insights from the data. Effectively interpreting and analyzing simulation results involves scrutinizing key parameters, identifying flow patterns, and validating the simulation against experimental or theoretical benchmarks. Post-processing transforms raw data into actionable knowledge, enabling engineers to draw meaningful conclusions and make informed decisions based on the simulation outcomes.
In conclusion, mastering the key steps in CFD analysis using ANSYS Fluent demands a holistic approach. From creating a robust geometry and mesh to defining boundary conditions, configuring solver settings, and finally delving into post-processing, each step plays a pivotal role in the success of the simulation. A meticulous execution of these steps ensures that the simulation outcomes align with real-world scenarios, providing engineers with invaluable insights for optimizing and refining their mechanical designs.
Strategies for Handling Fluid Flow Problems:
In ANSYS Fluent, a variety of turbulence models are available to capture the complexities of fluid flow accurately. The choice of turbulence model is crucial and depends on the nature of the flow being simulated. Common models include the k-ε model, Reynolds Stress Model (RSM), Large Eddy Simulation (LES), and the Spalart-Allmaras model. The k-ε model, for instance, is widely used for industrial applications due to its balance between accuracy and computational efficiency. On the other hand, LES is preferred for resolving unsteady turbulent flows with large-scale structures. The selection criteria involve considerations such as the Reynolds number, flow characteristics (transitional, fully turbulent), and the availability of computational resources. Engineers must weigh the trade-off between accuracy and computational cost, choosing a model that aligns with the specific features of the fluid flow problem at hand.
ANSYS Fluent excels not only in fluid flow simulations but also in handling intricate heat transfer problems. The software facilitates the simulation of conduction, convection, and radiation heat transfer. Engineers can model various heat transfer mechanisms within a system, allowing for a comprehensive analysis of thermal behavior. For instance, in electronics cooling applications, ANSYS Fluent can simulate the convective heat transfer from electronic components to surrounding fluids. In combustion simulations, it captures the heat release and transfer processes accurately. The integration of heat transfer into fluid flow simulations is essential for understanding the thermal aspects of engineering systems. Engineers can derive insights into temperature distributions, heat fluxes, and thermal gradients, aiding in the design and optimization of heat exchangers, electronic devices, and other thermal systems.
In the realm of multiphase flow, ANSYS Fluent provides robust capabilities to simulate scenarios involving multiple phases such as gas-liquid, liquid-liquid, or solid-liquid interactions. Multiphase flow is relevant in numerous industries, including chemical processing, petroleum, and environmental engineering. Engineers can model phenomena like boiling, cavitation, and sedimentation, gaining insights into complex real-world scenarios. ANSYS Fluent's multiphase modeling considers the interactions between different phases, enabling the accurate prediction of phase distribution, velocity profiles, and mass transfer. This capability is invaluable for optimizing processes like mixing in chemical reactors or predicting the behavior of oil-water flows in pipelines. The software allows engineers to explore and understand the intricate dynamics of multiphase systems, contributing to the efficient design and operation of diverse engineering applications.
Conclusion:
Conducting a successful Computational Fluid Dynamics (CFD) analysis in ANSYS Fluent involves several key strategies that are pivotal for accurate and insightful simulations in mechanical engineering projects. First and foremost, meticulous attention to the geometry and meshing process is crucial. Creating an appropriate geometry and employing a well-structured mesh significantly influences the accuracy of the simulation results. Properly defined boundary conditions form the second critical strategy, as they provide the simulation with realistic scenarios, ensuring that the virtual environment closely mimics the physical one. Selection of an appropriate solver and understanding its settings is the third key strategy. ANSYS Fluent offers a variety of solvers, each suited for different fluid flow problems; thus, comprehending and choosing the right solver settings are paramount for achieving reliable simulations.
Post-processing, as the fourth strategy, involves extracting meaningful insights from simulation results. ANSYS Fluent provides robust post-processing tools, enabling users to visualize and interpret complex fluid flow phenomena effectively. Within this strategy, it is essential to grasp the significance of interpreting velocity contours, pressure distributions, and other relevant parameters to draw informed conclusions. Moving on, addressing fluid flow problems often involves tackling turbulence, making it the fifth key strategy. ANSYS Fluent offers various turbulence models, and choosing the appropriate one based on the specific nature of the flow is crucial for accurate predictions.
Heat transfer analysis, as the sixth strategy, adds another layer of complexity to fluid flow simulations. ANSYS Fluent's capabilities in handling heat transfer problems make it a versatile tool for a wide range of mechanical engineering applications. The seventh strategy involves multiphase flow, a crucial aspect in scenarios where different phases of a fluid are involved. ANSYS Fluent's ability to simulate multiphase flows broadens the spectrum of applications, allowing users to explore diverse and intricate fluid dynamics problems.
Encouraging readers to explore the possibilities of fluid flow simulations in their mechanical engineering projects is essential. By implementing these strategies, engineers can gain valuable insights into the behavior of fluids in various scenarios, leading to optimized designs and solutions. The versatility of ANSYS Fluent empowers engineers to simulate and analyze real-world problems, providing a deeper understanding of fluid dynamics and contributing to more informed decision-making in the field of mechanical engineering. Embracing fluid flow simulations through ANSYS Fluent opens doors to innovation, efficiency, and enhanced problem-solving capabilities, making it an invaluable tool for aspiring and practicing mechanical engineers alike.