Navigating CAD Principles with CATIA in Mechanical Engineering.
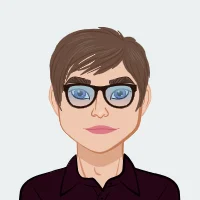
Navigating the intricate landscape of Mechanical Engineering requires a keen understanding of the technological tools that underpin the design and innovation processes. In this ever-evolving realm, Computer-Aided Design (CAD) stands as a cornerstone, revolutionizing the way engineers conceptualize and bring their ideas to life. The fusion of precision and creativity within CAD opens a world of possibilities, and at the forefront of this technological wave is CATIA. This blog post endeavors to unravel the complexities of CAD principles, specifically within the realm of Mechanical Engineering, shedding light on the pivotal role that CATIA plays in shaping the future of design. Whether you're a student looking to explore CAD principles or seeking help with your CATIA assignment, the comprehensive capabilities of CATIA make it an essential tool for those venturing into the intricacies of Mechanical Engineering design.
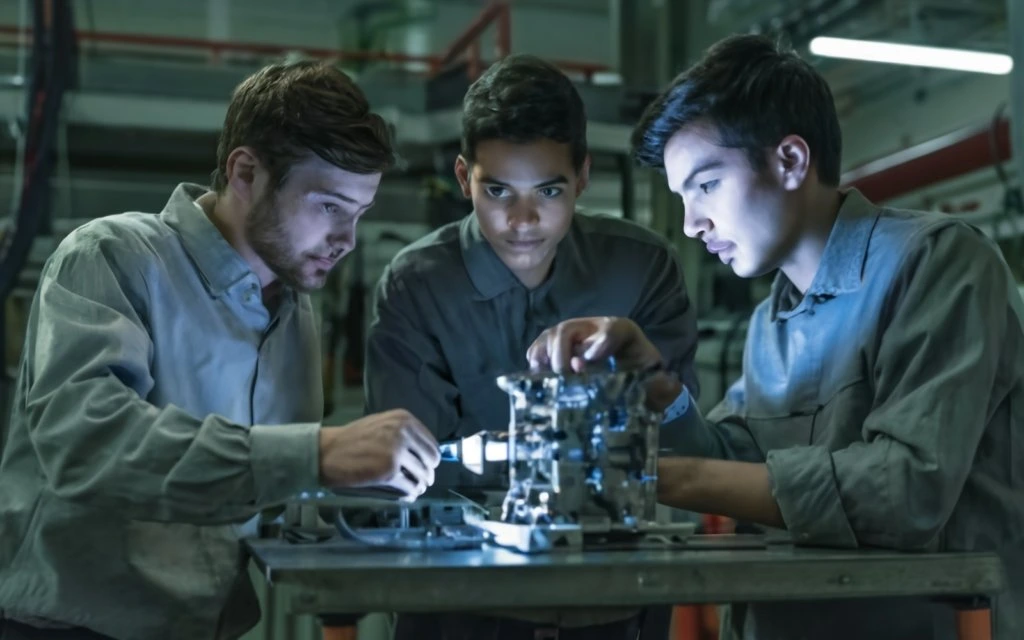
In the expansive domain of Mechanical Engineering, where innovation and efficiency are paramount, CAD has emerged as a transformative force. It transcends traditional design methodologies, offering engineers a virtual canvas to ideate, prototype, and refine their concepts with unprecedented precision. CAD empowers designers to transcend the limitations of manual drafting, facilitating the creation of intricate and sophisticated models that are the backbone of modern engineering projects. As we delve into the depths of CAD principles, it becomes evident that a comprehensive understanding of these tools is not merely advantageous but imperative for those navigating the complex terrain of Mechanical Engineering.
At the heart of this technological revolution lies CATIA, a powerhouse among CAD software. CATIA, an acronym for Computer-Aided Three-dimensional Interactive Application, has garnered acclaim for its robust suite of features that cater specifically to the demands of Mechanical Engineering. Its versatility extends across various domains, including product design, aerospace, automotive, and beyond. The significance of CATIA in the realm of Mechanical Engineering cannot be overstated, as it serves as a catalyst for innovation, streamlining design processes, and elevating the quality of engineering outputs.
As we embark on a journey through the nuances of CAD principles with a focus on CATIA, it is crucial to recognize the multifaceted nature of this software. From parametric modeling that allows for dynamic changes in design parameters to assembly design that orchestrates the integration of complex components, CATIA serves as a comprehensive toolbox for engineers. The precision and accuracy offered by CATIA extends to surface modeling, enabling the creation of sleek and aerodynamic structures that are vital in industries such as automotive and aerospace.
Real-world applications illuminate the profound impact of CATIA in Mechanical Engineering projects. Its utilization spans from the initial stages of conceptualization to the finalization of intricate assembly designs. Engineers and designers across industries leverage CATIA to innovate, collaborate, and overcome the challenges inherent in the complex world of Mechanical Engineering. This blog post aims to unravel the layers of CATIA's applications, providing insights into its role in shaping the technological landscape.
As we navigate the expansive realm of CAD principles within CATIA, this post will not only elucidate key concepts but also offer practical tips and tricks for users. From shortcuts that enhance workflow efficiency to lesser-known features that unlock new possibilities, readers will gain valuable insights into maximizing their proficiency with CATIA. Challenges inherent in mastering such a robust tool will be addressed, accompanied by pragmatic solutions that empower users to navigate complexities with confidence.
In conclusion, this exploration into the realm of CAD principles with a focus on CATIA seeks to empower aspiring engineers, seasoned professionals, and enthusiasts alike. The fusion of theoretical understanding and practical application is the essence of mastering CAD tools, and this blog post endeavors to bridge that gap. As we unravel the intricacies of CATIA, it becomes apparent that proficiency in CAD principles is not merely a skill but a key to unlocking the door to innovation in Mechanical Engineering.
Overview of CAD in Mechanical Engineering.
Computer-Aided Design (CAD) has evolved into an indispensable tool within the realm of Mechanical Engineering, revolutionizing the way engineers conceptualize, design, and refine their creations. At its core, CAD is a digital representation of the traditional drafting board, offering a virtual workspace where intricate designs and complex engineering solutions come to life. This overview delves into the multifaceted role of CAD in Mechanical Engineering, emphasizing its transformative impact on the industry.
CAD serves as a technological bridge between imagination and realization, providing engineers with a powerful platform to translate abstract ideas into tangible designs. The traditional method of manual drafting, characterized by painstakingly detailed drawings, has given way to the precision and efficiency of CAD. With the advent of this technology, engineers can visualize and manipulate three-dimensional models with unprecedented accuracy, enabling a level of detail and complexity that was previously unattainable.
One of the key advantages of CAD in Mechanical Engineering lies in its ability to facilitate parametric modeling. This dynamic approach allows engineers to define design parameters and establish relationships between various components, providing the flexibility to make real-time adjustments. The parametric nature of CAD not only expedites the design process but also empowers engineers to explore multiple iterations of a concept, fostering innovation and optimization.
The collaborative nature of CAD is another cornerstone of its significance. In a globalized and interconnected world, where teams may be dispersed across geographical boundaries, CAD provides a centralized platform for seamless collaboration. Design files can be shared, reviewed, and modified in real-time, fostering efficient communication and reducing the likelihood of errors. This collaborative aspect is particularly crucial in industries where complex projects require the integration of diverse expertise.
Furthermore, CAD serves as a repository of knowledge, preserving design intent and enabling easy modifications throughout the product lifecycle. Changes can be implemented at any stage, from the initial concept to the manufacturing phase, ensuring that the design remains adaptable to evolving requirements. This not only enhances the longevity of the design but also contributes to a more sustainable and cost-effective engineering process.
In the broader context of Mechanical Engineering, CAD has become a catalyst for innovation, significantly impacting industries such as automotive, aerospace, and manufacturing. The speed and precision afforded by CAD tools have streamlined the prototyping and testing phases, accelerating the overall product development cycle. As technology continues to advance, CAD remains at the forefront, continually evolving to meet the evolving needs of Mechanical Engineering, from intricate component design to the assembly of complex systems. In essence, CAD is not merely a tool; it is a transformative force that empowers engineers to push the boundaries of what is possible in the dynamic and ever-evolving field of Mechanical Engineering.
Introduction to CATIA.
In the expansive landscape of Computer-Aided Design (CAD) tools, CATIA (Computer-Aided Three-dimensional Interactive Application) stands tall as a powerhouse, wielding unparalleled capabilities that have made it a linchpin in the world of Mechanical Engineering. CATIA transcends the conventional boundaries of design software, offering a comprehensive suite of tools that empower engineers to tackle the most intricate challenges with finesse. This introduction aims to unravel the multifaceted nature of CATIA, delving into its origins, core features, and its transformative impact on the field of Mechanical Engineering.
CATIA, developed by Dassault Systèmes, has its roots tracing back to the late 1970s when the aerospace industry was in dire need of a revolutionary design tool. Over the decades, CATIA has evolved into a sophisticated and versatile software, finding applications not only in aerospace but also in automotive, shipbuilding, and various other industries where precision and innovation are paramount. Its development has been characterized by a commitment to providing engineers and designers with a unified platform that encompasses the entire product development process.
At the heart of CATIA's prowess lies its robust suite of features, each meticulously crafted to cater to the diverse demands of Mechanical Engineering. The software's parametric modeling capabilities set it apart, allowing engineers to create designs that are not static entities but dynamic, responsive to changes in design parameters. This flexibility not only expedites the design process but also facilitates iterative refinement, a crucial aspect in the pursuit of optimal engineering solutions.
CATIA's prowess extends beyond individual component design, encompassing the intricacies of assembly design. The software facilitates the seamless integration of complex components, providing engineers with a holistic view of the entire system. This is particularly critical in industries such as automotive and aerospace, where the interaction of various parts within an assembly is integral to the overall functionality and performance of the final product.
Surface modeling is another hallmark feature of CATIA, enabling engineers to craft intricate and aesthetically pleasing designs. Whether in automotive body design or aerospace components, the ability to create and manipulate complex surfaces is indispensable. CATIA's surface modeling tools empower designers to achieve a level of sophistication and precision that is essential in industries where form and function are intrinsically linked.
CATIA's applications in Mechanical Engineering are as diverse as the field itself. From conceptualization and design validation to prototyping and manufacturing, CATIA serves as a comprehensive toolbox that accompanies engineers throughout the entire product development lifecycle. Its role is not confined to the digital realm; CATIA integrates seamlessly with computer-aided manufacturing (CAM) and computer-aided engineering (CAE) tools, creating a synergistic ecosystem that optimizes efficiency and ensures a seamless transition from design to production.
As we navigate the intricate terrain of CATIA, it becomes evident that its impact extends far beyond the digital realm. It is an enabler of innovation, a catalyst for collaboration, and a guardian of precision in Mechanical Engineering. This introduction serves as a gateway to a deeper exploration of CATIA's features, applications, and the myriad ways in which it empowers engineers to transcend the boundaries of what is achievable in the dynamic and ever-evolving world of Mechanical Engineering.
Key CAD Principles in CATIA.
Within the dynamic realm of Computer-Aided Design (CAD), CATIA stands out for its robust implementation of key principles that underpin the design process in Mechanical Engineering. As engineers navigate the intricate landscape of CATIA, several fundamental CAD principles come to the forefront, shaping the way designs are conceived, developed, and optimized. One of the key principles inherent in CATIA is parametric modeling, which forms the bedrock of its design philosophy. This principle allows engineers to create dynamic, adaptive models by establishing relationships between various components and defining parameters that govern their behavior. This dynamic nature enables real-time modifications, fostering a responsive design environment where changes in one part of the model propagate throughout the entire system.
Another critical CAD principle embedded in CATIA is assembly design. CATIA facilitates the seamless integration of individual components into complex assemblies, providing engineers with a comprehensive view of the entire system. This principle is essential in industries where products consist of numerous interconnected parts, such as automotive or aerospace. Engineers can visualize the assembly, assess how components interact, and identify potential issues early in the design phase. The ability to manage complex assemblies efficiently is a testament to CATIA's commitment to enhancing the holistic design process.
Surface modeling stands as a pinnacle principle within CATIA, especially in industries where aesthetics and aerodynamics play a crucial role. CATIA's surface modeling tools empower engineers to create and manipulate complex, freeform surfaces with precision. Whether designing automotive exteriors or aerospace components, this principle ensures that the form and function of the product are harmoniously balanced. Surface modeling in CATIA goes beyond traditional solid modeling, allowing for the creation of visually appealing and aerodynamically efficient designs.
CATIA also excels in the principle of design validation through its advanced simulation and analysis capabilities. Engineers can subject their designs to virtual testing, assessing factors such as stress, strain, and fluid dynamics. This principal aids in refining designs, optimizing performance, and ensuring that products meet the stringent requirements of real-world applications. CATIA's integration with computer-aided engineering (CAE) tools reinforces its commitment to providing a comprehensive platform for design validation.
In summary, the key CAD principles embedded in CATIA - parametric modeling, assembly design, surface modeling, and design validation - collectively contribute to its status as a preeminent CAD tool in Mechanical Engineering. These principles not only streamline the design process but also empower engineers to create innovative, functional, and aesthetically pleasing products. As users delve into the intricacies of CATIA, they navigate a landscape where these principles converge, offering a powerful and versatile toolkit for tackling the challenges inherent in the diverse and ever-evolving field of Mechanical Engineering.
Applications in Mechanical Engineering.
CATIA's applications in Mechanical Engineering span a broad spectrum, influencing and optimizing various facets of the design and development process. In the realm of product design, CATIA is an indispensable tool for creating detailed 3D models of mechanical components. Engineers leverage their parametric modeling capabilities to define parameters, ensuring designs are adaptable to changes and iterations. This flexibility streamlines the iterative design process, allowing for rapid prototyping and facilitating the exploration of multiple design alternatives.
In assembly design, CATIA excels by providing a platform for the integration of complex mechanical systems. Industries such as automotive and aerospace benefit significantly from CATIA's assembly design capabilities, allowing engineers to visualize, simulate, and analyze the interactions between various components. This ensures that the assembled product functions seamlessly and meets rigorous standards of safety and performance.
The automotive industry relies heavily on CATIA for tasks ranging from conceptualizing vehicle designs to simulating crash tests and optimizing aerodynamics. CATIA's surface modeling tools play a pivotal role in shaping the sleek exteriors of automobiles, contributing to both aesthetics and functionality. Additionally, CATIA's ability to simulate and analyze structural elements ensures that vehicles are not only visually appealing but also robust and safe.
Aerospace engineering is another domain where CATIA's applications shine. The software aids in the design and analysis of aircraft components, enabling engineers to create models that adhere to strict industry standards. CATIA's capabilities extend to the simulation of complex aerodynamic forces, contributing to the development of aircraft that are not only fuel-efficient but also possess optimal performance characteristics. From conceptualizing airframes to designing intricate components like turbine blades, CATIA plays a pivotal role in shaping the aerospace landscape.
In the manufacturing sector, CATIA facilitates the transition from design to production seamlessly. Its integration with computer-aided manufacturing (CAM) tools ensures that designs are translated into precise instructions for machining and fabrication. This alignment between design and manufacturing reduces errors, minimizes production costs, and accelerates time-to-market.
Beyond these industries, CATIA finds applications in a diverse range of Mechanical Engineering fields, including consumer goods, industrial machinery, and renewable energy. Its versatility allows engineers to address a myriad of challenges, from optimizing the efficiency of industrial equipment to designing components for renewable energy systems.
In essence, CATIA's applications in Mechanical Engineering are extensive and transformative. The software's adaptability, robust feature set, and integration capabilities make it a cornerstone in the toolkit of engineers across various industries, enabling them to innovate, collaborate, and navigate
Challenges and Solutions.
While CATIA is a powerful and versatile tool in Mechanical Engineering, its utilization is not without challenges. One significant challenge engineer may face is the learning curve associated with mastering the extensive features and capabilities of CATIA. The software's richness and complexity can be overwhelming for beginners, requiring dedicated training and practice to unlock its full potential. To overcome this challenge, companies and individuals can invest in comprehensive training programs, online tutorials, and mentorship to accelerate the learning process. Establishing a structured learning path can empower users to navigate the intricacies of CATIA effectively.
Another challenge lies in the potential for data management issues, especially when dealing with large and complex projects. CATIA generates vast amounts of data, including 3D models, assemblies, and simulations, which can lead to difficulties in version control, collaboration, and file organization. Implementing robust data management systems, such as Product Data Management (PDM) or Product Lifecycle Management (PLM) solutions, becomes crucial. These systems help streamline collaboration, ensure version control, and enhance overall data organization, mitigating the risk of errors and inefficiencies.
Interoperability can present a challenge, particularly in environments where multiple CAD tools are in use. Compatibility issues may arise when exchanging files between CATIA and other software platforms, potentially leading to data loss or format discrepancies. To address this challenge, investing in translators or converters that facilitate seamless data exchange between different CAD systems is essential. Additionally, staying abreast of industry standards and file formats can enhance interoperability, enabling smoother collaboration in multi-CAD environments.
Performance optimization is another challenge, especially when dealing with large and complex models. CATIA's robust features can sometimes lead to software performance issues, affecting responsiveness and efficiency. To tackle this challenge, engineers can adopt best practices in model simplification, utilize level-of-detail representations, and leverage hardware upgrades to enhance system performance. Regular software updates and patches provided by the software developer can also address performance issues by introducing optimizations and bug fixes.
Collaboration across dispersed teams poses a significant challenge, particularly in today's globalized work environment. CATIA's collaboration tools, such as the 3DEXPERIENCE platform, aim to address this challenge by providing a cloud-based collaborative environment. Embracing these collaborative features, coupled with effective communication protocols and project management strategies, can enhance teamwork, ensuring that team members can seamlessly contribute to projects irrespective of their geographical locations.
In conclusion, while CATIA offers unparalleled capabilities in Mechanical Engineering, challenges such as the learning curve, data management, interoperability, performance optimization, and collaboration must be acknowledged and addressed. Strategic investments in training, data management systems, interoperability solutions, performance optimization techniques, and collaborative platforms can empower engineers to maximize the benefits of CATIA while overcoming the inherent challenges associated with its use. By doing so, professionals can harness the full potential of CATIA, contributing to innovative and efficient solutions in the field of Mechanical Engineering.
Conclusion:
In the ever-evolving landscape of Mechanical Engineering, the journey through the intricacies of CATIA reveals a transformative tool that transcends conventional boundaries, leaving an indelible mark on the design and innovation process. The exploration of CATIA's applications, challenges, and solutions underscores its pivotal role in shaping the way engineers conceive, visualize, and bring their ideas to fruition. As we draw the curtain on this exploration, a comprehensive conclusion emerges, highlighting the significance of CATIA in the realm of Mechanical Engineering.
CATIA's applications in Mechanical Engineering extend far beyond mere design; they encompass the entire product development lifecycle. From the conceptualization of innovative ideas to the detailed design of intricate components, CATIA serves as a digital canvas where creativity meets precision. Its role in assembly design, particularly in industries such as automotive and aerospace, showcases its ability to orchestrate the integration of complex systems, providing engineers with a holistic view of their creations. In sectors like automotive design, CATIA's surface modeling principles contribute not only to aesthetics but also to aerodynamics, influencing the efficiency and performance of vehicles.
However, this journey through CATIA is not without its challenges. The learning curve, inherent in mastering its extensive features, demands commitment and structured training programs. Data management challenges, interoperability issues, and the need for performance optimization add layers of complexity to its utilization. These challenges, though formidable, are not insurmountable. Strategic investments in training, data management systems, interoperability solutions, and performance optimization techniques pave the way for engineers to harness the full potential of CATIA.
In addressing these challenges, CATIA emerges as a solution-oriented tool. Its adaptability and robust feature set allow engineers to navigate complexities with confidence. The collaboration tools embedded in CATIA, such as the 3DEXPERIENCE platform, exemplify its commitment to fostering teamwork and enabling seamless collaboration across global teams. By overcoming challenges, engineers elevate their proficiency, leveraging CATIA as an instrument for innovation, efficiency, and excellence.
As we conclude this exploration, it becomes evident that CATIA is not just software; it is a catalyst for advancement in Mechanical Engineering. It empowers engineers to push the boundaries of what is achievable, fostering a culture of continuous improvement and technological innovation. CATIA's legacy is etched in its ability to transform concepts into tangible designs, drive collaboration in globalized work environments, and optimize the product development process. In the ever-challenging landscape of Mechanical Engineering, CATIA stands as a beacon, guiding engineers towards a future where precision, creativity, and efficiency converge to shape the next generation of groundbreaking innovations.