Avoiding Pitfalls: Common Mistakes in Abaqus Simulations!
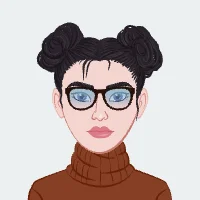
Abaqus, a powerful and versatile finite element analysis (FEA) software, stands at the forefront of simulation tools widely employed in the dynamic realm of mechanical engineering. Developed by Dassault Systèmes SIMULIA, Abaqus has become synonymous with innovation, offering engineers a comprehensive platform to simulate and analyze complex behaviors of structures, components, and materials under a variety of conditions. Its robust capabilities encompass structural, thermal, and coupled thermal-structural simulations, making it an invaluable asset for engineers engaged in the design and optimization of mechanical systems. Understanding the intricacies of this software and its applications in mechanical engineering is crucial for mastering finite element analysis and achieving success in your Abaqus assignments and projects.
In the ever-evolving landscape of engineering projects, the significance of accurate simulations cannot be overstated. The ability to virtually replicate and assess the performance of components or systems before physical prototypes are built has transformed the way engineers approach design challenges. Accurate simulations serve as a predictive lens, allowing engineers to foresee potential issues, optimize designs, and make informed decisions throughout the product development lifecycle. This not only accelerates the design process but also minimizes the need for costly physical testing and iterations.
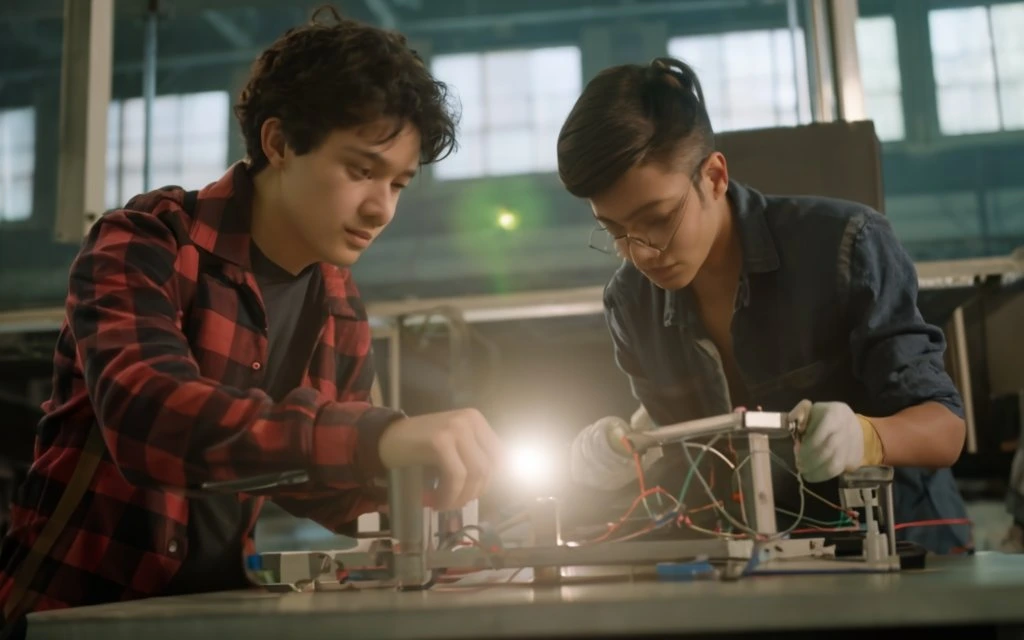
One paramount aspect of Abaqus is its capacity to simulate the complex interactions that occur within mechanical systems, capturing the nuances of material behaviors, structural deformations, and thermal effects. This capability is crucial for engineers working on projects ranging from automotive and aerospace to civil and biomechanical applications. The software enables users to model and analyze diverse scenarios, such as the impact of external forces, thermal gradients, or fluid-structure interactions, with a level of accuracy that mirrors real-world conditions.
Accurate simulations in engineering projects act as a virtual laboratory, providing engineers with insights that might be challenging or impractical to obtain through physical experiments alone. They allow for the exploration of multiple design iterations, facilitating an iterative and optimization-driven design process. By identifying potential issues early in the development phase, engineers can make informed design modifications, thereby reducing the likelihood of costly errors and ensuring the final product meets or exceeds performance expectations.
Moreover, accurate simulations contribute to enhanced safety and reliability in engineering endeavors. Whether it be assessing the structural integrity of a bridge, optimizing the aerodynamics of an aircraft wing, or analyzing the thermal behavior of electronic components, Abaqus simulations empower engineers to uncover potential weaknesses and address them proactively. This not only enhances the overall safety of structures and systems but also mitigates risks associated with unforeseen failures or suboptimal performance.
In conclusion, Abaqus stands as a cornerstone in the toolkit of mechanical engineers, offering a sophisticated platform for accurate and comprehensive simulations. The software's capabilities align seamlessly with the demands of modern engineering, where precision, efficiency, and reliability are paramount. The importance of accurate simulations cannot be overstressed, as they not only streamline the design process but also foster innovation, reduce development costs, and ultimately contribute to the creation of safer, more robust engineering solutions. In embracing Abaqus, engineers embark on a journey where the virtual and physical realms converge, unlocking a realm of possibilities in the pursuit of engineering excellence.
Importance of Abaqus Simulations
Engineers widely use Abaqus for simulations due to its robust capabilities and versatility, making it an indispensable tool in the field of mechanical engineering. Simulation plays a pivotal role in various aspects of engineering, including product design, optimization, and performance prediction.
Abaqus stands out for its ability to model and simulate complex physical behaviors accurately, enabling engineers to analyze and understand the intricate interactions within a system. In product design, simulations with Abaqus allow engineers to virtually prototype and test components before physical prototypes are built. This not only accelerates the design process but also minimizes the need for costly and time-consuming physical testing. Engineers can explore different design variations and scenarios in a virtual environment, leading to more informed and optimized design decisions.
Optimization is another critical area where Abaqus excels. The software enables engineers to perform parametric studies and optimization processes to fine-tune designs and achieve optimal performance. By systematically varying design parameters and analyzing their impact on performance, engineers can identify the most efficient and effective configurations. This iterative optimization process helps in creating products that meet performance requirements while minimizing material usage and overall cost.
Abaqus plays a crucial role in predicting the performance of engineering systems under various operating conditions. Through simulations, engineers can evaluate how different factors such as loads, temperatures, and material properties influence the behavior of a structure or component. This predictive capability is invaluable in assessing the structural integrity, thermal performance, and overall reliability of designs. By identifying potential issues early in the design phase, engineers can make informed adjustments, reducing the likelihood of unexpected failures in the real-world application.
Simulations with Abaqus also contribute to risk mitigation in product development. Engineers can assess the safety margins of designs, identify potential failure modes, and implement design changes to enhance reliability. This proactive approach significantly reduces the likelihood of costly errors and recalls in the later stages of product development.
In conclusion, engineers choose Abaqus for simulations because of its advanced capabilities in modeling complex physical behaviors. Simulations with Abaqus empower engineers in product design by providing a virtual testing ground, enable optimization through iterative design improvements, and contribute to performance prediction for enhanced reliability. The software's versatility and accuracy make it an indispensable tool for ensuring the success of engineering projects across various industries.
Overview of Abaqus Simulation Process
Setting up an Abaqus simulation involves a systematic process that encompasses multiple steps to ensure accurate and reliable results. The process typically begins with defining the geometry and progresses through material properties, mesh generation, boundary conditions, and finally, the execution of the simulation. Each step plays a crucial role in determining the simulation's fidelity and its ability to reflect real-world scenarios.
Firstly, the geometry of the structure or component under analysis must be accurately defined. This includes specifying dimensions, shapes, and any intricate details essential for the simulation. Ensuring a precise representation of the physical model lays the foundation for the entire simulation process.
Once the geometry is established, the next step involves assigning material properties. This includes defining material models, material constants, and any nonlinear behavior that may be present. Selecting the appropriate material model is critical, as it directly influences the accuracy of the simulation. Engineers must carefully consider the material's response under different loading conditions to capture realistic behavior.
Following material assignment, mesh generation becomes a pivotal stage. Meshing involves discretizing the geometry into smaller elements, enabling the software to perform calculations at specific points within the structure. The quality of the mesh significantly impacts simulation accuracy. Engineers must strike a balance between a fine mesh for detailed results and a coarse mesh for computational efficiency.
After meshing, boundary conditions are applied to mimic the physical constraints and loading conditions the structure will experience. Constraints define how the structure interacts with its surroundings, and accurate representation of these conditions is paramount for meaningful simulation outcomes. Incorrect boundary conditions can lead to unrealistic results and compromise the reliability of the simulation.
Key parameters such as time step size, convergence criteria, and solution controls are established before running the simulation. Time step size influences the temporal resolution of dynamic simulations, convergence criteria dictate the stopping criteria for iterative solvers, and solution controls manage the overall numerical solution strategy. Balancing these parameters is crucial for achieving convergence and obtaining meaningful results.
Throughout the entire setup process, engineers must consider the specific requirements of their simulation, such as the type of analysis (static, dynamic, thermal, etc.) and any additional features like contact interactions or material nonlinearity. Regular validation against experimental data and sensitivity analyses are also recommended to ensure the simulation accurately represents the real-world behavior of the system under investigation.
In summary, the key to a successful Abaqus simulation lies in meticulous attention to detail at each stage of the setup process. From geometry definition to boundary conditions and solution controls, every step demands thoughtful consideration to produce reliable and accurate results, aligning the virtual simulation with the physical reality it seeks to represent.
Common Mistakes in Abaqus Simulations
In the realm of Abaqus simulations, the accuracy of results hinges significantly on the meticulousness with which engineers handle crucial aspects such as meshing, boundary conditions, material model selection, convergence, and contact interactions. Common mistakes in any of these areas can undermine the reliability of the simulation, leading to inaccurate predictions and potentially jeopardizing the success of engineering projects.
Inadequate meshing is a frequent pitfall that engineers encounter. The mesh serves as a numerical representation of the physical structure, and its quality profoundly influences the precision of the simulation. Proper meshing is crucial for capturing the complex behaviors of the model. Common errors in mesh generation include overly coarse meshes that fail to capture details, or overly fine meshes that introduce excessive computational demands. These mistakes can result in inaccurate stress distributions, deformation patterns, and failure predictions, compromising the overall reliability of the simulation.
Accurate representation of boundary conditions is equally pivotal. Boundary conditions define how the structure interacts with its environment and withstands external loads. Common mistakes in applying boundary conditions include overlooking essential constraints, applying incorrect restraints, or misrepresenting loading conditions. These errors can lead to unrealistic deformations, stress concentrations, and failure predictions, rendering the simulation less useful for real-world applications.
The selection of the right material model is paramount for capturing the material's response under different loading conditions. Common errors in material model selection involve choosing models that inadequately represent the material behavior or making incorrect assumptions about material properties. Such mistakes can result in simulations that diverge significantly from reality, impacting the accuracy of predictions related to structural integrity, durability, and performance.
Convergence issues pose another challenge in Abaqus simulations. Achieving convergence is crucial for obtaining reliable results, especially in nonlinear analyses. Common convergence problems include divergence of the solution, failure to meet convergence criteria, or excessive computational demands. Engineers must employ appropriate solution controls, adjust time step sizes, and carefully monitor convergence to overcome these challenges and ensure accurate results.
Overlooking contact and interaction between components can also lead to significant inaccuracies. In many engineering scenarios, different parts of a structure interact with each other, and modeling these interactions is vital for realistic simulations. Common mistakes involve neglecting contact interfaces, using inappropriate contact formulations, or misjudging the nature of interactions. These errors can result in unphysical separation, unrealistic stresses, or improper load transfer between components.
In conclusion, a thorough understanding of the importance of proper meshing, accurate boundary conditions, material model selection, convergence considerations, and contact interactions is essential for engineers conducting Abaqus simulations. Addressing common mistakes in these areas is crucial for enhancing the reliability and relevance of simulation results, ultimately contributing to informed decision-making in mechanical engineering projects.
Best Practices for Successful Abaqus Simulations
Successfully conducting Abaqus simulations requires not only a thorough understanding of the software but also adherence to best practices that can enhance the accuracy and reliability of results. Here are practical tips to avoid common mistakes and insights into validation techniques and model verification.
1. Comprehensive Material Characterization:
- Accurate material characterization is fundamental. Ensure a thorough understanding of material behavior under different loading conditions.
- Validate material models by comparing simulation results with experimental data. Calibration may be necessary to fine-tune material parameters.
2. Mesh Quality and Convergence:
- Invest time in generating a high-quality mesh. Avoid distorted elements and ensure adequate refinement where needed.
- Monitor convergence during simulations. Adjust time step sizes and convergence criteria to strike a balance between accuracy and computational efficiency.
3. Robust Boundary Conditions:
- Precise definition of boundary conditions is critical. Verify that constraints and loading conditions accurately represent the physical setup.
- Consider sensitivity analyses on boundary conditions to understand their impact on results.
4. Careful Contact Modeling:
- Pay attention to contact interfaces, ensuring proper definition of interactions between components.
- Validate contact formulations and parameters through benchmark tests or comparisons with analytical solutions.
5. Sensitivity Analyses:
- Conduct sensitivity analyses on key parameters to understand their influence on results.
- Identify critical parameters and their acceptable ranges to enhance the robustness of the simulation.
6. Validation against Experimental Data:
- Validate simulations by comparing results with experimental data. This helps ensure the model's predictive accuracy.
- Utilize a variety of tests, such as static and dynamic loadings, to validate different aspects of the simulation.
7. Model Verification:
- Verify the model against analytical solutions whenever possible. This provides confidence in the accuracy of the simulation setup.
- Implement benchmark tests that have established solutions to validate specific features of the simulation.
8. Documentation and Reproducibility:
- Maintain detailed documentation of simulation setup, including material properties, meshing parameters, and boundary conditions.
- Aim for reproducibility by providing clear instructions on how others can replicate your simulation.
9. Continuous Learning and Updates:
- Stay updated with the latest features and improvements in Abaqus. Regularly check for software updates and incorporate new functionalities into your simulations.
- Participate in forums and communities to learn from others' experiences and share insights.
10. Collaboration and Peer Review:
- Collaborate with colleagues or experts in the field for peer review of your simulation setup.
- Feedback from others can identify potential issues and improve the overall quality of the simulation.
By incorporating these best practices, engineers can significantly enhance the reliability and accuracy of their Abaqus simulations, fostering confidence in the virtual representation of mechanical systems and structures.
Conclusion:
In conclusion, this blog post has delved into the critical aspects of Abaqus simulations, aiming to guide engineers and students in avoiding common pitfalls. The journey from geometry definition to simulation execution involves meticulous considerations, and awareness of potential mistakes is paramount for achieving accurate and reliable results.
We began by emphasizing the importance of Abaqus simulations in the field of mechanical engineering, underlining their role in product design, optimization, and performance prediction. The comprehensive overview of the simulation process highlighted the sequential steps, starting with precise geometry definition and progressing through material assignment, mesh generation, and the application of boundary conditions. Each of these steps is interdependent, and any oversight can lead to compromised simulation outcomes.
The blog post specifically delved into common mistakes encountered in Abaqus simulations, such as inadequate meshing, incorrect boundary conditions, material model selection errors, convergence issues, and overlooking contact and interaction. Understanding these pitfalls is crucial for engineers and students alike, as it equips them with the knowledge needed to navigate the challenges inherent in simulation setup.
To mitigate these challenges, the blog provided best practices for successful Abaqus simulations. It emphasized the significance of proper meshing techniques, accurate application of boundary conditions, thoughtful material model selection, proactive convergence troubleshooting, and the meticulous consideration of contact and interaction between components. Incorporating these best practices into simulation workflows enhances the accuracy and reliability of results, ultimately leading to more meaningful insights for engineering projects.
In encouraging readers to adopt these best practices, it is essential to underscore the impact of simulations on real-world decision-making. Accurate simulations empower engineers to make informed design choices, optimize performance, and predict the behavior of structures and components. By adhering to the outlined best practices, individuals can elevate their simulation capabilities, ensuring that their virtual models align closely with physical reality.
In conclusion, successful Abaqus simulations demand a holistic approach, where attention to detail, validation against experimental data, and adherence to best practices converge to produce reliable results. As readers embark on their simulation endeavors, the blog encourages them to view these guidelines not just as technical instructions but as a roadmap toward achieving simulations that stand up to scrutiny and contribute meaningfully to the advancement of mechanical engineering knowledge and practice.