Thermal Analysis in ANSYS: Strategies for Solving Heat Transfer Problems!
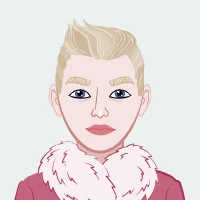
In the dynamic realm of mechanical engineering, understanding and controlling heat transfer processes is a cornerstone for the development of efficient and reliable systems. Thermal analysis plays a pivotal role in this domain, offering engineers profound insights into the intricate interplay of heat within mechanical structures. Whether designing automotive components, aerospace systems, or industrial machinery, the ability to predict and manage thermal behavior is paramount for help with your Ansys assignment.
Thermal analysis encompasses the study of heat generation, distribution, and dissipation within a given system. It allows engineers to assess the impact of temperature variations on material properties, structural integrity, and overall performance. This discipline becomes particularly crucial when dealing with applications where temperature fluctuations can influence functionality, safety, and longevity.
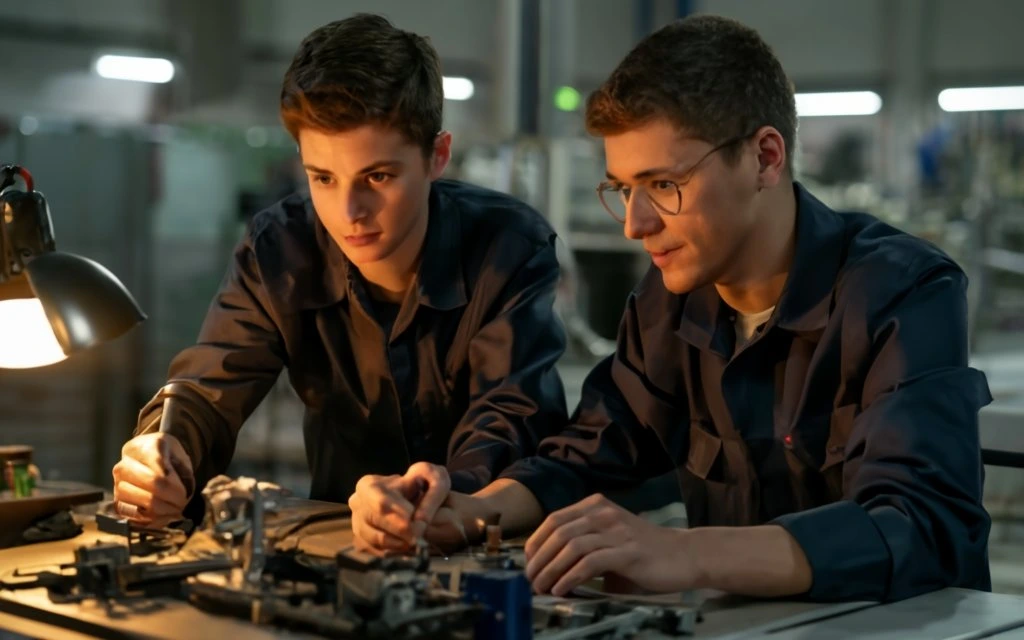
The significance of thermal analysis is most pronounced in the context of ANSYS software, a powerful tool that has become synonymous with advanced engineering simulations. ANSYS provides a comprehensive platform for conducting sophisticated thermal analyses, enabling engineers to model and predict thermal behavior with remarkable accuracy. Its capabilities extend across a spectrum of applications, from simulating the heat dissipation in electronic components to predicting thermal stresses in complex mechanical systems.
One of the key strengths of ANSYS lies in its ability to handle multiphysics simulations, seamlessly integrating thermal analysis with other crucial aspects such as structural mechanics and fluid dynamics. This holistic approach allows engineers to explore the interconnected nature of different physical phenomena, providing a more realistic representation of real-world conditions. In the realm of heat transfer problems, where the influence of structural deformations or fluid flow on temperature distribution is significant, ANSYS emerges as an indispensable tool for comprehensive analyses.
The software's versatility in handling various boundary conditions and material properties adds another layer of sophistication to thermal simulations. Engineers can accurately model diverse scenarios, from transient heat conduction in intricate geometries to convective heat transfer in complex fluid-solid interfaces. ANSYS empowers users to explore the nuances of heat transfer phenomena, offering a nuanced understanding that goes beyond simplified approximations.
Furthermore, ANSYS provides an extensive library of predefined elements and material models, streamlining the simulation setup process. This not only enhances efficiency but also ensures that engineers can focus on interpreting results and optimizing designs rather than grappling with the intricacies of numerical modeling.
In essence, the marriage of thermal analysis and ANSYS software heralds a new era in mechanical engineering, where the virtual realm becomes a playground for innovation and optimization. The ability to predict thermal performance with a high degree of confidence empowers engineers to push the boundaries of design, creating products and systems that are not only functional but also resilient in the face of thermal challenges. As industries continue to evolve and demand ever-higher standards, the synergy between thermal analysis and ANSYS proves instrumental in shaping the next generation of cutting-edge mechanical solutions.
Understanding Heat Transfer:
Heat transfer, a fundamental phenomenon in the realm of mechanical engineering, is characterized by the movement of thermal energy from regions of higher temperature to lower temperature. Three primary modes govern this transfer: conduction, convection, and radiation, each playing a distinctive role in shaping the thermal behavior of systems.
- Conduction, the first mode, occurs through direct physical contact between particles. In solids, such as metal rods or composite materials, heat travels by causing adjacent particles to vibrate. This transfer is highly efficient in conductive materials, making it a prevalent mechanism in scenarios where solids dominate the structure.
- Convection, the second mode, involves the transfer of heat through the movement of fluids (liquids or gases). As fluids circulate, they carry thermal energy from hot regions to cooler areas. This mechanism is prominent in applications like HVAC systems, where air or water is employed to distribute and regulate temperature.
- Radiation, the third mode, is unique as it operates without the need for a medium. Infrared waves transport heat energy across space, making radiation effective even in a vacuum. This phenomenon is crucial in situations where direct physical contact or fluid movement is impractical, such as in spacecraft or electronic components.
Accurate heat transfer analysis is paramount across diverse mechanical engineering applications due to its pervasive impact on system performance, safety, and efficiency. In structural components like bridges or buildings, improper heat dissipation can lead to thermal stresses, potentially compromising the structural integrity over time. In the automotive industry, understanding heat transfer is vital for optimizing engine performance, ensuring components operate within safe temperature ranges, and minimizing wear and tear. Additionally, in electronics and semiconductor manufacturing, precise thermal control is imperative to prevent overheating, which can degrade the functionality and lifespan of sensitive electronic devices.
Moreover, in aerospace applications, where extreme temperature variations are commonplace, a thorough understanding of heat transfer mechanisms is essential for designing components that can withstand the rigors of space travel. In renewable energy systems like solar panels, efficient heat transfer ensures maximum energy conversion, contributing to the sustainability of power generation.
In essence, accurate heat transfer analysis serves as a linchpin in the design and optimization of mechanical systems. It not only prevents potential failures due to thermal issues but also allows engineers to innovate and enhance the performance of products across various industries, ultimately shaping the landscape of modern mechanical engineering.
Introduction to ANSYS:
ANSYS, a powerful finite element analysis software, stands as a cornerstone in the world of mechanical engineering, providing engineers with a sophisticated platform for conducting comprehensive simulations. With a robust suite of tools, ANSYS facilitates a myriad of analyses, ranging from structural and fluid dynamics to electromagnetic simulations. Its versatility makes it a go-to solution for engineers seeking to gain deep insights into the behavior of complex systems.
In the realm of mechanical engineering, ANSYS plays a pivotal role in performing advanced simulations that transcend traditional boundaries. Its finite element analysis capabilities enable engineers to model and analyze intricate structures with a high degree of accuracy. Whether predicting the stresses on a mechanical component or simulating fluid flow through a complex geometry, ANSYS excels in providing a holistic understanding of diverse engineering scenarios.
One of the standout features of ANSYS is its prowess in handling complex thermal analysis problems. In the dynamic field of heat transfer, where accuracy is paramount, ANSYS stands as a reliable ally for engineers tackling challenging thermal scenarios.
- Geometry and Material Properties: ANSYS allows engineers to accurately define and manipulate the geometry of their models, ensuring a precise representation of real-world structures. Moreover, it provides a comprehensive library of material properties, enabling users to simulate a wide range of materials with diverse thermal characteristics.
- Boundary Conditions: Accurate representation of boundary conditions is crucial for meaningful thermal analysis. ANSYS offers a rich set of tools for specifying and refining boundary conditions, allowing engineers to model realistic thermal environments. This includes the simulation of heat sources, convective heat transfer, and thermal radiation.
- Meshing: The efficiency of thermal simulations is heavily dependent on the quality of the mesh. ANSYS provides robust meshing capabilities, allowing engineers to create finely detailed meshes that capture the intricacies of thermal gradients. This ensures accurate and reliable results in the analysis of heat transfer problems.
- Solver Settings: ANSYS offers a range of solver options tailored for thermal simulations. Engineers can fine-tune solver settings to meet the specific requirements of their analysis, whether it involves transient heat conduction, convective heat transfer, or radiation heat transfer.
In essence, ANSYS serves as an indispensable tool for engineers navigating the complexities of thermal analysis in mechanical engineering. Its capabilities not only streamline the simulation process but also empower engineers to make informed decisions, optimize designs, and push the boundaries of innovation in the quest for robust and efficient mechanical systems.
Strategies for Efficient Heat Transfer Problem Solving:
Parameter Sensitivity Analysis:
In the intricate realm of thermal simulations, parameter sensitivity analysis emerges as a critical strategy for understanding how variations in input parameters can influence heat transfer results and provide valuable insights into system behavior. This approach involves systematically altering key parameters, such as material properties, geometry, or boundary conditions, to assess their impact on the overall thermal performance of a system. By scrutinizing how changes in these parameters reverberate through the simulation results, engineers gain a nuanced understanding of the system's sensitivity to different factors. For example, in a heat exchanger simulation, altering the thermal conductivity of the materials or adjusting the flow rate of the fluid can unveil the system's responsiveness to these variations. Parameter sensitivity analysis not only aids in identifying influential factors but also guides engineers in optimizing designs and operational parameters to achieve desired thermal outcomes. It provides a roadmap for decision-making, allowing engineers to focus efforts on the most influential aspects, ultimately leading to more robust and efficient heat transfer solutions.
Optimization Techniques:
Introducing optimization methods within ANSYS elevates the quest for efficient heat transfer solutions to a new level. ANSYS provides a comprehensive suite of tools for optimization, allowing engineers to systematically enhance the performance of heat transfer systems. Optimization in the context of thermal analysis involves refining design parameters to achieve specific objectives, such as minimizing heat loss, maximizing heat dissipation, or optimizing temperature distribution. Engineers can define design variables, constraints, and objective functions, and ANSYS employs algorithms to iteratively explore the design space and converge toward optimal solutions. This iterative process not only refines the design but also provides insights into the trade-offs inherent in the system. Engineers can explore a multitude of design scenarios, identifying the most efficient configurations that meet performance criteria. Whether optimizing fin geometries in a heat sink or refining insulation materials in a thermal barrier, ANSYS optimization techniques empower engineers to fine-tune designs, improve thermal efficiency, and extract maximum performance from heat transfer systems. In essence, optimization becomes a guiding compass for engineers, steering them toward designs that not only meet thermal requirements but also push the boundaries of efficiency and innovation in the realm of heat transfer.
Conclusion:
In the blog post, "Thermal Analysis in ANSYS: Strategies for Solving Heat Transfer Problems," we delved into the intricacies of thermal analysis in mechanical engineering, particularly focusing on the capabilities of ANSYS software. The three main modes of heat transfer—conduction, convection, and radiation—were introduced, emphasizing their significance in various mechanical engineering applications. ANSYS, as a versatile finite element analysis tool, emerged as a powerhouse for advanced simulations, offering engineers a comprehensive platform to model and analyze complex systems.
The post highlighted ANSYS's prowess in handling intricate thermal analysis problems, covering aspects such as geometry and material properties, boundary conditions, meshing, and solver settings. The discussion extended to two key strategies for efficient heat transfer problem-solving: parameter sensitivity analysis and optimization techniques. Parameter sensitivity analysis was presented as a method to systematically vary input parameters and gain insights into their impact on heat transfer results, guiding engineers in optimizing designs. Optimization techniques within ANSYS were introduced as a means to refine design parameters iteratively, aiming to achieve specific thermal objectives and enhance overall system performance.
In conclusion, the synergy between thermal analysis and ANSYS software stands as a catalyst for innovation in mechanical engineering, allowing engineers to make informed decisions, optimize designs, and push the boundaries of efficiency. The encouragement for readers lies in the recognition of the paramount importance of accurate heat transfer analysis across various industries. Aspiring engineers and professionals are urged to explore thermal analysis further, recognizing its role in shaping the next generation of mechanical solutions. The capabilities of ANSYS open doors to a realm of possibilities, and readers are invited to harness this tool for their projects.
For those navigating the complexities of mechanical engineering assignments, seeking professional assistance is highlighted as a prudent step. The intricate nature of thermal analysis and the power of ANSYS demand a nuanced understanding that professionals in the field possess. Engaging with experts ensures not only the completion of assignments but also an opportunity to gain insights into best practices, further enhancing one's grasp of thermal analysis concepts. By taking this proactive approach, students and professionals alike can bridge the gap between theoretical knowledge and practical application, paving the way for success in the dynamic field of mechanical engineering.