Fluid Dynamics Simulations in ANSYS: Techniques for Accurate Modeling!
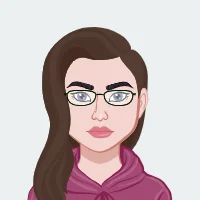
Fluid dynamics simulations in mechanical engineering are indispensable tools that allow engineers to gain a deep understanding of how fluids behave in different scenarios, enabling them to optimize and enhance various engineering processes. Accurate modeling within these simulations plays a pivotal role in ensuring the reliability and precision of results, which are critical for making informed decisions in the field of mechanical engineering. Whether you need help with your Ansys assignment or are simply looking to delve deeper into fluid dynamics simulations, mastering the intricacies of software like Ansys is essential for success in the field of mechanical engineering.
Fluid dynamics simulations involve the numerical analysis of fluid flow, heat transfer, and other related phenomena within a virtual environment. In mechanical engineering, these simulations are applied to a wide range of scenarios, from aerodynamics in aircraft design to optimizing the performance of industrial machinery. Accurate modeling is the cornerstone of these simulations, as it allows engineers to replicate real-world conditions with a high degree of fidelity, ensuring that the insights gained from the simulations are applicable and reliable.
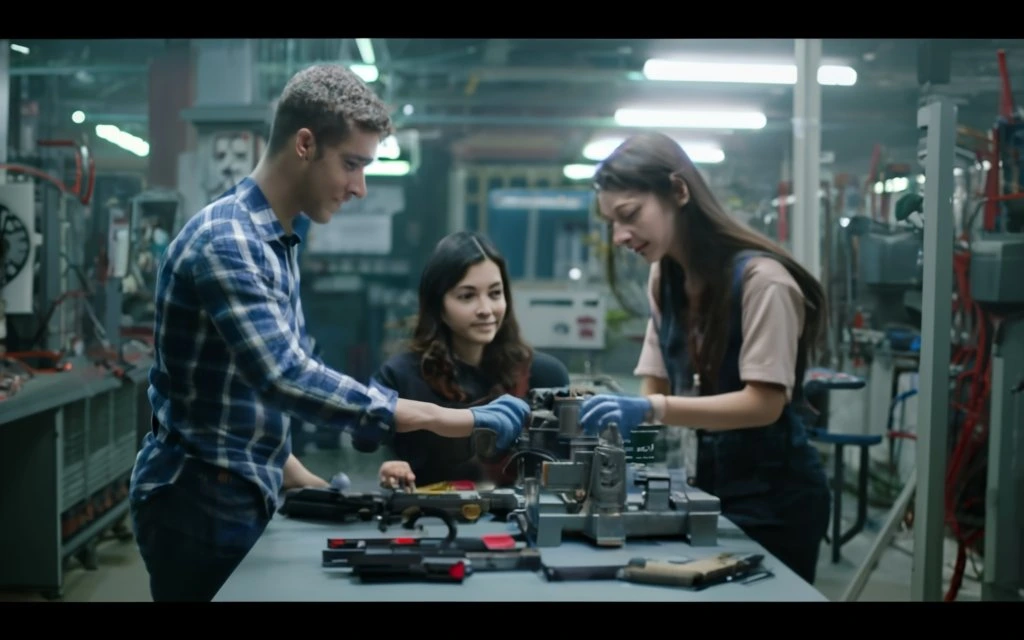
One of the primary reasons why accurate modeling is crucial in fluid dynamics simulations is its impact on understanding complex fluid behaviors. Fluids, whether gases or liquids, exhibit intricate patterns and interactions that can significantly influence the performance of mechanical systems. Accurate modeling enables engineers to capture these nuances, providing a comprehensive view of how fluids behave under different conditions. This understanding is essential for designing systems that operate efficiently and reliably.
Moreover, accurate modeling plays a crucial role in optimizing engineering processes. Whether designing a more fuel-efficient aircraft or improving the efficiency of a heat exchanger in an industrial plant, engineers rely on fluid dynamics simulations to assess and refine their designs. The accuracy of these simulations directly translates to the effectiveness of the optimizations made. Engineers can explore various design parameters, tweak geometries, and analyze the impact of different factors on fluid behavior. This iterative process of optimization is only meaningful when the simulations accurately represent the physical reality, ensuring that the proposed improvements are valid and effective.
In addition to optimizing designs, accurate modeling in fluid dynamics simulations contributes to the identification and mitigation of potential issues in engineering systems. Engineers can simulate extreme conditions, identify potential failure points, and make design modifications to enhance safety and reliability. This proactive approach, made possible by accurate modeling, is instrumental in preventing costly failures and ensuring that engineering systems meet the required performance standards.
Furthermore, accurate fluid dynamics simulations are essential in industries where efficiency and precision are paramount, such as the automotive and aerospace sectors. From designing more aerodynamic vehicles to optimizing the cooling systems of engines, accurate modeling allows engineers to fine-tune every aspect of their designs. This level of precision is crucial in meeting performance goals, regulatory requirements, and customer expectations.
In conclusion, fluid dynamics simulations are indispensable tools in mechanical engineering, providing insights that are instrumental in optimizing designs and processes. The importance of accurate modeling cannot be overstated, as it ensures that the simulations faithfully represent real-world conditions. Through accurate modeling, engineers can confidently make decisions, optimize designs, and address potential issues, ultimately contributing to the advancement and efficiency of mechanical engineering processes.
Overview of ANSYS:
ANSYS, a leading simulation software company, has established itself as a cornerstone in the field of mechanical engineering, providing powerful tools for simulation, analysis, and optimization. With a rich suite of software products, ANSYS has become synonymous with advanced engineering simulation and is widely acclaimed for its ability to address complex challenges across various industries.
At its core, ANSYS offers a comprehensive platform for finite element analysis (FEA), computational fluid dynamics (CFD), electromagnetic simulation, and structural mechanics. Its significance in mechanical engineering lies in its capability to model and simulate a broad spectrum of physical phenomena, allowing engineers to explore and understand the behavior of structures, fluids, and electromagnetic fields under diverse conditions.
In the realm of fluid dynamics simulations, ANSYS stands out as a go-to solution for engineers and researchers. Its CFD capabilities enable users to simulate fluid flow, heat transfer, and related phenomena with a high level of accuracy. ANSYS employs advanced numerical methods and algorithms to solve complex fluid dynamics equations, providing detailed insights into the behavior of fluids in different scenarios. This is particularly crucial in mechanical engineering applications where understanding and optimizing fluid flow are paramount, such as in aerodynamics, thermal management, and chemical processes.
The popularity of ANSYS in conducting fluid dynamics simulations can be attributed to several factors. Firstly, the software offers a user-friendly interface that allows engineers to set up, run, and analyze simulations efficiently. This accessibility is coupled with a robust solver that can handle intricate geometries and complex physics, providing realistic results that align closely with real-world conditions.
Another key aspect of ANSYS's popularity is its versatility. The software accommodates a wide range of boundary conditions, turbulence models, and fluid types, allowing engineers to tailor simulations to specific applications. Whether simulating airflow over an aircraft wing or predicting heat transfer in a manufacturing process, ANSYS provides the flexibility needed to address diverse fluid dynamics challenges.
Furthermore, ANSYS is renowned for its commitment to innovation. Regular updates and enhancements ensure that the software keeps pace with advancements in simulation technology and meets the evolving needs of the engineering community. This commitment to staying at the forefront of simulation capabilities enhances ANSYS's appeal and contributes to its widespread adoption in the mechanical engineering domain.
In summary, ANSYS plays a crucial role in the field of mechanical engineering, offering a comprehensive simulation platform with a particular emphasis on fluid dynamics. Its capabilities, user-friendly interface, versatility, and commitment to innovation have solidified its popularity among engineers and researchers, making it an indispensable tool for those seeking accurate and reliable insights into fluid behavior in diverse engineering applications.
Importance of Accurate Modeling:
Accurate modeling is indispensable in fluid dynamics simulations as it forms the bedrock for reliable and precise results, profoundly influencing the decision-making process in engineering designs. The intricacies of fluid behavior demand a high level of fidelity in simulation models to ensure that the predicted outcomes closely mirror real-world conditions. Inaccuracies in modeling can lead to unreliable results, compromising the effectiveness of simulations and undermining the trust placed in the insights derived from them.
At the core of accurate modeling is the need to capture the complexities inherent in fluid flow, turbulence, heat transfer, and other related phenomena. Fluids exhibit intricate patterns and interactions that play a pivotal role in determining the performance of engineering systems. Accurate modeling enables the representation of these nuances, providing a comprehensive understanding of how fluids behave under different conditions. This fidelity is essential for predicting the impact of design changes, operational parameters, or external factors on the fluid dynamics of a system.
The reliability of fluid dynamics simulations hinges on the accuracy of the models in replicating physical reality. Engineers rely on these simulations to gain insights into the performance of prototypes, analyze the efficiency of systems, and predict potential issues. Accurate modeling ensures that the simulation results align with actual observations, allowing engineers to make informed decisions about design modifications, operational strategies, or safety measures. This reliability is crucial for minimizing the risk of unexpected failures or suboptimal performance in real-world applications.
Precision in fluid dynamics simulations is equally vital, particularly when dealing with engineering designs where small variations can have significant consequences. Accurate modeling contributes to the precision of results by minimizing errors and uncertainties in the simulation process. This precision enables engineers to confidently assess the impact of design parameters, evaluate the effectiveness of optimization strategies, and make decisions that are grounded in a thorough understanding of fluid dynamics principles.
In the decision-making process of engineering designs, the consequences of inaccurate modeling can be far-reaching. A flawed simulation model may lead to misguided design choices, resulting in suboptimal performance, increased costs, or safety concerns. On the contrary, accurate modeling enhances the credibility of simulation results, empowering engineers to make decisions with a higher level of confidence. This, in turn, streamlines the design iteration process, reduces the need for costly physical prototypes, and accelerates the overall product development timeline.
In conclusion, accurate modeling is essential in fluid dynamics simulations as it underpins the reliability and precision of results, significantly impacting the decision-making process in engineering designs. By ensuring that simulations faithfully represent real-world conditions, accurate modeling provides engineers with the confidence to make informed decisions, optimize designs effectively, and navigate the complex landscape of fluid dynamics with precision and reliability.
Techniques for Accurate Fluid Dynamics Simulations:
Accurate fluid dynamics simulations are pivotal in deciphering the complex behaviors of fluids in various engineering applications, ranging from aerodynamics and automotive design to chemical processes and environmental studies. To achieve meaningful and reliable results, it is essential to employ techniques that ensure the accuracy of the simulation models. The intricacies of fluid flow, turbulence, and heat transfer necessitate a nuanced approach to modeling, taking into account a multitude of factors that influence fluid behavior. In this exploration of "Techniques for Accurate Fluid Dynamics Simulations," we delve into the methodologies and practices that engineers and researchers employ to enhance the precision and reliability of their simulations.
The success of fluid dynamics simulations relies heavily on the quality of the model's representation of the physical world. An introduction to accurate fluid dynamics simulations requires an understanding of the significance of these simulations in predicting real-world phenomena and optimizing engineering designs. Fluid dynamics governs the behavior of liquids and gases, making it a critical aspect of various industrial processes and systems. Accurate simulations serve as virtual laboratories, allowing engineers to explore and understand fluid behavior without the need for costly and time-consuming physical experiments.
The introduction to techniques for accurate fluid dynamics simulations begins by acknowledging the challenges inherent in modeling fluid flow. From the complexities of turbulent flows to the intricacies of multiphase systems, each scenario demands specialized techniques to ensure a faithful representation. This introduction sets the stage for a comprehensive exploration of the methodologies that engineers employ to address these challenges. By emphasizing the critical role of accurate simulations in decision-making processes related to design optimization, safety assessments, and performance predictions, the introduction aims to underscore the practical importance of mastering the techniques discussed in subsequent sections.
Moreover, the introduction highlights the broader context of the simulation landscape, where advancements in computational power and simulation software have opened up new possibilities for achieving higher levels of accuracy. The integration of cutting-edge technologies and innovative approaches enhances the precision of fluid dynamics simulations, enabling engineers to explore scenarios and gain insights that were once inconceivable. By framing the discussion within this context, the introduction fosters an appreciation for the dynamic and evolving nature of fluid dynamics simulation techniques.
In essence, the introduction serves as a gateway to a deeper understanding of the techniques that contribute to the accuracy of fluid dynamics simulations. It conveys the significance of these simulations in the realm of engineering and sets the tone for a detailed exploration of the methodologies that engineers employ to overcome the challenges posed by fluid complexities. As we embark on this journey, the goal is to equip practitioners with a robust toolkit of techniques, ensuring that their fluid dynamics simulations not only meet but exceed the demands of real-world applications.
Geometry Preparation:
Geometry preparation stands as a foundational step in the quest for accurate fluid dynamics simulations, wielding a profound impact on the reliability and efficiency of the entire simulation process. A well-prepared geometry serves as the digital representation of the physical system under consideration, and its accuracy directly influences the fidelity of the simulation results. The intricacies of fluid flow, turbulence, and heat transfer necessitate a geometrical model that faithfully captures the essential features of the real-world counterpart. Inaccuracies or complexities in the geometry can introduce errors that propagate throughout the simulation, compromising the validity of the results and hindering the decision-making process in engineering designs.
To enhance simulation efficiency and accuracy, techniques for cleaning and simplifying geometries play a pivotal role. Cleaning involves the removal of imperfections, anomalies, or unwanted artifacts from the geometric model. This process ensures that the simulation is based on a smooth and error-free representation of the physical system. Techniques for cleaning may include the removal of unnecessary details, elimination of small features that don't significantly impact the simulation, and addressing irregularities that could disrupt the fluid flow patterns.
Simplifying geometries is equally crucial for streamlining simulations without sacrificing accuracy. Complex geometries often result in computationally intensive simulations that demand significant resources. Techniques for simplification involve reducing the geometric complexity while retaining the essential features that influence fluid dynamics. This might entail merging or smoothing surfaces, collapsing small features, or employing parametric methods to represent intricate geometries more efficiently.
The significance of geometry preparation extends beyond mere data input; it serves as a gateway to meaningful insights. By embracing techniques that ensure a well-prepared geometry, engineers pave the way for simulations that accurately mirror real-world conditions. This, in turn, fosters a robust foundation for decision-making processes related to design optimization, performance predictions, and safety assessments. Ultimately, the meticulous attention given to geometry preparation not only enhances simulation efficiency but also reinforces the credibility and applicability of fluid dynamics simulations in the broader landscape of mechanical engineering.
Meshing Strategies:
Meshing plays a crucial role in achieving accurate results in fluid dynamics simulations by discretizing the geometry into smaller elements, or mesh, allowing numerical approximation of fluid behavior at specific points within the domain. The quality of the mesh directly influences the precision and reliability of the simulation results. Inaccurate or poorly-constructed meshes can introduce errors, leading to unreliable predictions of fluid flow, pressure, and heat transfer. As such, understanding meshing strategies becomes paramount in ensuring the fidelity of simulations.
ANSYS, a renowned simulation software, offers a range of meshing techniques that cater to the diverse requirements of fluid dynamics simulations. One prominent method is the ANSYS Meshing tool, which provides both automated and manual mesh generation options. Automated meshing employs algorithms to generate meshes based on specified settings and desired element sizes, simplifying the process for users with limited meshing expertise. On the other hand, manual meshing allows users greater control over the mesh quality, enabling refinement in specific regions of interest.
Best practices for fluid dynamics simulations in ANSYS emphasize the importance of mesh quality over sheer mesh density. A fine mesh doesn't guarantee accuracy if it lacks quality. Therefore, it's crucial to focus on achieving a well-structured mesh that accurately captures the geometry's intricacies. Techniques such as local mesh refinement in areas of high gradient or complex flow patterns enhance accuracy without an unnecessary increase in computational cost.
Furthermore, utilizing inflation layers near solid boundaries and refining the mesh in regions with anticipated flow separation or turbulence is essential. This helps in capturing boundary layer effects and ensuring accurate predictions of fluid behavior near surfaces. Regular validation and sensitivity analysis of the mesh, adjusting it based on the physics of the problem, contribute to robust and reliable simulations.
In conclusion, the role of meshing in achieving accurate results in fluid dynamics simulations cannot be overstated. ANSYS provides a suite of meshing tools and techniques that, when coupled with best practices, enable engineers to generate high-quality meshes. By understanding the intricacies of meshing and implementing sound strategies, practitioners can enhance the accuracy of their simulations, paving the way for more reliable and insightful analyses in the field of fluid dynamics.
Boundary Conditions:
Boundary conditions play a crucial role in fluid dynamics simulations, serving as the interface between the simulated system and its external environment. The accuracy of these conditions significantly influences the reliability of simulation results and, by extension, the overall effectiveness of the engineering analysis. Properly defining boundary conditions is paramount because they mimic the interactions of fluids with their surroundings, influencing flow patterns, temperature distributions, and pressure gradients within the system.
One key aspect of setting appropriate boundary conditions is ensuring they reflect the physical reality of the system being simulated. Accurate representation of the system's external influences, such as inlet velocities, environmental temperatures, and material properties at boundaries, is essential. For instance, in aerodynamic simulations, specifying realistic air velocities at inlet boundaries is vital for predicting the aerodynamic forces acting on an object. In heat transfer simulations, accurately defining thermal boundary conditions, such as convection coefficients and temperatures, is crucial for predicting temperature distributions and thermal gradients accurately.
Inaccurate or poorly defined boundary conditions can lead to misleading simulation results, compromising the validity of the entire analysis. For instance, if the inlet velocity is incorrectly set, it can introduce unrealistic flow patterns and affect pressure distributions within the system. Similarly, imprecise thermal boundary conditions may result in inaccurate predictions of temperature variations, impacting heat transfer analyses. These inaccuracies can propagate throughout the simulation domain, influencing critical engineering parameters and hindering the reliability of the simulation outcomes.
Conversely, when accurate boundary conditions are employed, the simulation mirrors real-world scenarios more closely. For example, in automotive aerodynamics, specifying the correct wind speed and direction at the inlet ensures that the simulation captures the intricacies of airflow around the vehicle accurately. In thermal analysis of electronic components, setting precise heat transfer coefficients at boundaries ensures an authentic representation of heat dissipation, aiding in the design of effective cooling systems.
In conclusion, the importance of setting appropriate boundary conditions in fluid dynamics simulations cannot be overstated. Accurate boundary conditions are the bridge between the simulated system and its surroundings, influencing the fidelity of results. Examples abound in various engineering applications, illustrating how meticulous definition of boundary conditions enhances simulation accuracy, enabling engineers to make informed decisions based on reliable insights derived from their analyses.
Solver Settings:
Solver settings play a pivotal role in the accuracy and efficiency of fluid dynamics simulations within ANSYS, influencing how the software processes and solves the mathematical equations governing fluid flow. ANSYS provides engineers with a comprehensive suite of solver settings, allowing for a nuanced adjustment of parameters to tailor simulations to specific scenarios. One crucial aspect of solver settings is the choice of numerical methods for discretizing the governing equations, such as finite volume or finite element methods. These methods impact the accuracy of the simulation by determining how the physical domain is divided into discrete elements for analysis.
Furthermore, the convergence criteria and tolerances set in the solver settings significantly influence the accuracy of the simulation results. Convergence criteria define when the simulation is considered converged, and tighter tolerances may result in more accurate but computationally expensive simulations. Engineers must strike a balance between computational efficiency and result accuracy when adjusting these settings.
The choice of turbulence models is another critical aspect within solver settings. Different turbulence models, such as k-epsilon or Reynolds-averaged Navier-Stokes (RANS), offer varying levels of accuracy and computational cost. Selecting an appropriate turbulence model depends on the specific characteristics of the flow being simulated. Additionally, the time-stepping scheme and the selection of implicit or explicit solvers impact the simulation's stability, convergence, and computational efficiency.
Solver settings also encompass the consideration of physical phenomena, such as heat transfer or multiphase flow, allowing engineers to customize simulations based on the complexities of the studied system. The accuracy of thermal simulations, for instance, relies on appropriately configuring parameters like thermal conductivity and specific heat within the solver settings.
The impact of different solver settings on simulation results is profound. Inaccurate or inappropriate choices may lead to non-convergence, unstable simulations, or results that deviate significantly from real-world observations. Conversely, well-tailored solver settings contribute to reliable and precise results, providing engineers with the confidence to make informed decisions during the design and optimization process. The interplay of these settings exemplifies the need for a thoughtful and informed approach, where a deep understanding of fluid dynamics principles is combined with practical expertise in configuring solver parameters to ensure the fidelity of simulation results in ANSYS.
Post-Processing and Visualization:
Post-processing and visualization play a pivotal role in extracting meaningful insights from fluid dynamics simulations conducted using ANSYS, a leading simulation software. ANSYS offers a comprehensive suite of post-processing tools that empowers engineers to interpret simulation results with precision and clarity. One of the standout features is the ability to visualize complex fluid flow patterns and temperature distributions, aiding in the identification of key trends and phenomena.
ANSYS provides a range of post-processing tools, including contour plots, vector plots, streamline visualizations, and cut planes, which allow engineers to explore and analyze various aspects of fluid dynamics simulations. Contour plots, for example, enable the visualization of scalar quantities such as pressure or temperature across the simulated domain, offering a spatial understanding of the distribution. Vector plots represent the direction and magnitude of fluid velocities, providing insights into flow patterns. Streamline visualizations further enhance comprehension by illustrating the path that fluid particles follow within the simulated environment. These tools collectively contribute to a comprehensive understanding of the simulated fluid behavior.
Effective visualization and interpretation of fluid dynamics data involve more than just the use of software tools. Tips for optimizing this process include selecting appropriate visualization techniques based on the specific goals of the analysis. For instance, streamline visualizations may be particularly useful in identifying recirculation zones or flow separations, while contour plots can aid in pinpointing areas of extreme temperature gradients. It is crucial to choose visualization methods that align with the specific objectives of the simulation study.
Another key tip is to leverage animation capabilities within ANSYS to dynamically showcase the evolution of fluid flow over time. Animations enhance the communication of dynamic processes, making it easier for stakeholders to grasp transient phenomena and understand the temporal evolution of fluid behavior.
Furthermore, effective communication of results involves clear annotation and labeling within visualizations. Engineers should provide context and highlight key features to facilitate a deeper understanding of the simulation outcomes, especially when sharing results with interdisciplinary teams or decision-makers.
In conclusion, ANSYS offers a robust set of post-processing tools that empower engineers to interpret and visualize fluid dynamics simulation results. The effective use of these tools, coupled with thoughtful visualization techniques and clear communication strategies, enhances the understanding of complex fluid behaviors. By incorporating these tips, engineers can extract valuable insights from their simulations, supporting informed decision-making and design optimization in various mechanical engineering applications.
Conclusion:
In this comprehensive exploration of "Fluid Dynamics Simulations in ANSYS: Techniques for Accurate Modeling," several key points emerge, underscoring the critical role of accurate modeling in fluid dynamics simulations and its significance in the field of mechanical engineering.
The blog began by emphasizing the importance of fluid dynamics simulations in mechanical engineering, elucidating their role in understanding and optimizing various engineering processes. Accurate modeling was identified as the linchpin for reliable and precise results in these simulations, providing a foundation for decision-making processes in engineering designs.
A subsequent section delved into the brief overview of ANSYS, highlighting its position as a leading simulation software company. ANSYS's significance in mechanical engineering was elucidated, showcasing its capabilities in finite element analysis, computational fluid dynamics (CFD), electromagnetic simulation, and structural mechanics. The focus then shifted to the popularity of ANSYS in conducting fluid dynamics simulations, attributing its widespread adoption to a user-friendly interface, robust solver, and versatility in accommodating various boundary conditions, turbulence models, and fluid types.
The core of the blog delved into the techniques for accurate fluid dynamics simulations, detailing key aspects such as geometry preparation, meshing strategies, setting appropriate boundary conditions, solver settings, and post-processing and visualization. Each technique was examined for its role in contributing to the overall accuracy of the simulation models. Real-world examples and case studies were suggested to provide practical insights into the application of these techniques.
A specific emphasis was placed on the challenges and solutions associated with fluid dynamics simulations. The blog addressed common issues such as convergence problems, turbulence modeling intricacies, and the importance of accurate representation of geometries. Solutions were proposed, guiding engineers on how to navigate these challenges effectively.
Finally, the importance of post-processing and visualization in ANSYS was discussed, showcasing the array of tools available for interpreting simulation results. Tips for effective visualization and interpretation were provided, highlighting the significance of choosing appropriate visualization techniques, leveraging animation capabilities, and ensuring clear communication through annotations and labels.
In conclusion, the blog reaffirms the pivotal role of accurate modeling techniques in fluid dynamics simulations using ANSYS. Accurate modeling ensures the reliability and precision of results, directly impacting the decision-making process in engineering designs. Whether optimizing designs, identifying potential issues, or predicting system performance, the accuracy of the simulation models underpins their efficacy in guiding informed decisions. By employing the discussed techniques within ANSYS, engineers can unlock a deeper understanding of fluid behaviors, leading to more robust and efficient mechanical engineering solutions.