Essential Concepts in Dynamics of Machinery Every Student Should Master!
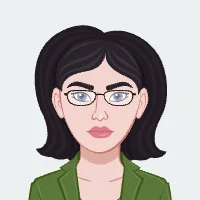
The dynamics of machinery holds a pivotal position within the realm of mechanical engineering, serving as the cornerstone for comprehending the intricate behaviors and functionalities of various mechanical systems. At its core, this discipline focuses on the study of motion, forces, and moments within machinery, providing engineers with the essential toolkit to analyze, design, and optimize mechanical components. Mastery of these dynamic concepts is not merely an academic pursuit; it is a linchpin for success in the field of mechanical engineering. A profound understanding of dynamics equips engineers with the ability to predict and control the motion of machines, ensuring their efficient and reliable operation. Whether it be the translational, rotational, or oscillatory motion encountered in diverse machinery, the principles of dynamics illuminate the underlying mechanisms governing these movements.
In the dynamic landscape of mechanical engineering, the importance of mastering these concepts cannot be overstated. Dynamics serves as the bridge between theory and real-world application, allowing engineers to translate mathematical models into practical solutions. For instance, in the design phase of a complex mechanical system, an engineer well-versed in dynamics can meticulously assess the forces acting on different components, predict their effects on motion, and subsequently optimize the system for optimal performance. Moreover, in troubleshooting scenarios, where unexpected vibrations or malfunctions arise, a deep understanding of dynamics enables engineers to diagnose and rectify issues swiftly, ensuring the reliability and safety of machinery.
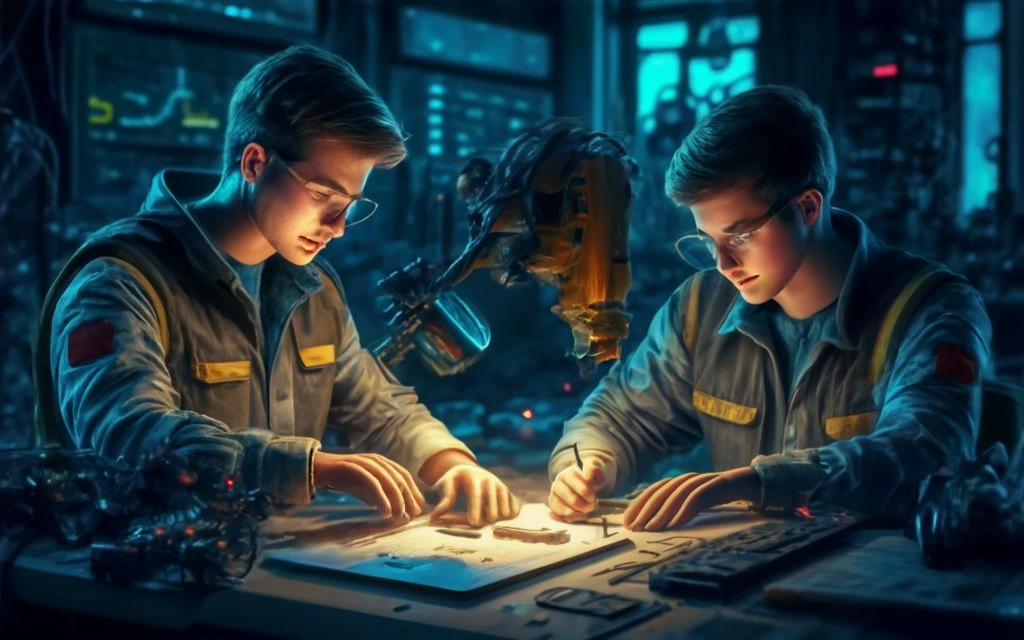
Balancing is a critical aspect of dynamics that directly influences the performance and longevity of machinery. Unwanted vibrations, often resulting from imbalances, can lead to premature wear and tear, compromising the efficiency and structural integrity of mechanical systems. By mastering the principles of balancing, engineers can mitigate these vibrations, ensuring smooth and stable operation. This is particularly crucial in high-precision applications, such as aerospace or medical equipment, where even the slightest deviation from optimal performance can have significant consequences.
Furthermore, the study of forces and moments in dynamics provides a comprehensive framework for assessing the structural integrity of mechanical components. Engineers armed with this knowledge can design robust structures capable of withstanding the forces they will encounter during operation. This not only enhances the safety of machinery but also contributes to cost-effectiveness by minimizing the risk of component failure and the associated maintenance and repair expenses.
In conclusion, the dynamics of machinery is the bedrock upon which mechanical engineering stands. Its significance lies not only in theoretical foundations but in its practical application, guiding engineers in the design, analysis, and optimization of mechanical systems. Mastery of dynamic concepts empowers engineers to navigate the complexities of motion, forces, and moments, ensuring the success of mechanical endeavors. As technology continues to advance, the role of dynamics in mechanical engineering becomes increasingly vital, making it imperative for aspiring engineers to delve deep into these principles for a prosperous and impactful career in the field.
Definition of Dynamics of Machinery:
Dynamics of Machinery is a fundamental discipline within the realm of mechanical engineering that delves into the intricate study of forces, motions, and interactions in mechanical systems. At its core, it encapsulates the comprehensive analysis of how machines and mechanical components behave under the influence of external forces, providing invaluable insights into the dynamic aspects of their motion and functionality. Unlike statics, which concerns itself with systems in equilibrium, dynamics shifts its focus to the dynamic forces and moments that propel machines into motion or govern their responses to external stimuli.
In the mechanical engineering domain, mastering the concepts of Dynamics of Machinery holds profound significance as it forms the cornerstone for designing, optimizing, and troubleshooting various mechanical systems. Understanding the dynamic behavior of machines is indispensable for engineers aiming to enhance performance, efficiency, and safety in mechanical applications. Whether dealing with rotating components, reciprocating machinery, or complex interconnected systems, a profound grasp of dynamics empowers engineers to predict and control the intricate interplay between forces and motions.
The significance of Dynamics of Machinery becomes particularly evident when considering the implications for real-world applications. Engineers engaged in designing engines, conveyor systems, robotics, or any mechanical system must navigate the complex landscape of dynamic forces to ensure optimal performance and longevity. For instance, an in-depth understanding of dynamic forces is critical for designing engines that operate smoothly and efficiently, minimizing wear and tear. Similarly, in the realm of robotics, where precise and controlled motions are paramount, dynamics plays a pivotal role in crafting systems that respond seamlessly to external stimuli.
Moreover, Dynamics of Machinery plays a pivotal role in addressing challenges related to vibrations, imbalances, and resonance. Engineers armed with a profound knowledge of dynamics can effectively analyze and mitigate issues arising from vibrations, ensuring the structural integrity and longevity of machinery. This discipline serves as a guiding beacon for engineers, enabling them to fine-tune designs, predict potential failures, and implement solutions that optimize performance while minimizing undesirable effects.
In essence, Dynamics of Machinery is the bedrock upon which mechanical engineering principles stand. It provides the analytical tools and conceptual frameworks necessary to comprehend the dynamic intricacies of machines, empowering engineers to innovate, troubleshoot, and elevate the efficiency and reliability of mechanical systems across diverse applications. In the dynamic world of mechanical engineering, mastery of these concepts is not just an academic pursuit but a gateway to shaping the future of technology and industry.
Types of Motion in Machinery:
Motion in machinery is a multifaceted concept, encompassing various types that play pivotal roles in the functioning of mechanical systems. Translational motion, a fundamental form, involves the linear displacement of an object from one point to another. This is exemplified by the straightforward back-and-forth motion of a piston within an engine, where the reciprocal translation transforms into useful mechanical work. In translational motion, the object's path follows a straight line, emphasizing the simplicity and directness of this movement.
Rotational motion, on the other hand, manifests as the circular or spinning motion of an object around an axis. An illustrative example is the rotation of a wheel on an axle. This type of motion is fundamental in machinery, especially in components like gears and turbines, where the circular motion is harnessed for mechanical advantage. Rotational motion is integral to the operation of many mechanical systems, providing the means to transfer power and transmit motion effectively.
Oscillatory motion introduces a periodic back-and-forth movement, akin to the swinging of a pendulum. This type of motion is prevalent in machinery components like crankshafts, which undergo oscillations during their rotation. Understanding oscillatory motion is crucial for designing systems with reciprocating elements, such as engines with pistons moving back and forth. Oscillatory motion is characterized by a repetitive pattern, and its mastery is essential for achieving precision and efficiency in mechanical applications.
These different types of motion are not mutually exclusive, and machinery often involves a combination of translational, rotational, and oscillatory motions. For instance, a piston in an engine undergoes both translational and oscillatory motions as it moves up and down within a cylinder. The synchronized interplay of these motions is what ultimately drives the machinery's overall functionality.
In conclusion, a comprehensive understanding of motion in machinery is vital for mechanical engineering students. Translational, rotational, and oscillatory motions are foundational concepts that form the basis of intricate mechanical systems. By delving into these types of motion and exploring real-world examples, students can grasp the dynamic nature of machinery, laying the groundwork for solving complex engineering challenges and contributing to advancements in the field.
Kinematics vs. Dynamics:
Kinematics and dynamics are two fundamental branches of mechanics that play a crucial role in understanding the motion of machinery. While both are integral to the field of mechanical engineering, they address distinct aspects of motion. Kinematics primarily focuses on the geometric aspects of motion, studying the position, velocity, and acceleration of objects without delving into the forces that cause the motion.
In the realm of machinery, kinematics serves as the foundation for analyzing the spatial and temporal characteristics of moving components. It allows engineers to describe the motion of machine parts, determine their trajectories, and comprehend the relationships between different elements. Essentially, kinematics provides a framework for visualizing and quantifying motion, making it an essential tool for designing mechanisms and predicting their movements.
On the other hand, dynamics delves deeper into the causes behind motion by considering the forces and torques acting on objects. In the context of machinery, dynamics explores how these forces influence the motion of components, affecting their velocity, acceleration, and ultimately their overall behavior. Unlike kinematics, which is concerned solely with motion's "what" and "how," dynamics introduces the critical "why" by examining the forces that drive or hinder the movement of machine parts.
For mechanical engineers, understanding the interplay between kinematics and dynamics is paramount. Kinematics provides a baseline understanding of how components move, enabling engineers to design systems that achieve specific motions. However, it is dynamics that adds a layer of complexity by introducing the physical forces and moments that machines experience. Engineers must carefully balance these forces to ensure optimal performance, efficiency, and safety of machinery.
In practical terms, kinematics might be applied to analyze the motion of a robotic arm, determining its range of motion and speed. Meanwhile, dynamics would come into play when considering the forces required to lift and manipulate objects, ensuring that the motor and structural components can withstand the applied loads.
In conclusion, while kinematics lays the groundwork for understanding motion in machinery by focusing on geometric parameters, dynamics takes a comprehensive approach by incorporating forces into the equation. Both branches are indispensable for mechanical engineers seeking to design, analyze, and optimize machinery for various applications, and mastering the interplay between kinematics and dynamics is key to engineering success.
Forces and Moments:
Forces and moments play a pivotal role in the intricate realm of the dynamics of machinery, wielding a profound influence on the behavior and performance of mechanical components. In the dynamic study of machinery, forces are omnipresent agents that propel motion and govern the equilibrium of systems. These forces, whether applied externally or arising from within the machinery, define the trajectories and motions of various components. For instance, in a rotating shaft, forces acting at different points can induce bending or torsional deformations, thereby dictating the mechanical response of the system. Understanding the intricate interplay of forces is paramount for engineers tasked with designing and optimizing machinery for efficiency and reliability.
Moments, on the other hand, introduce a rotational element to the dynamics, adding a layer of complexity to the machinery's behavior. Moments are rotational forces that manifest as twisting actions around an axis. In machinery, moments can lead to angular accelerations or decelerations, affecting the overall dynamics of the system. A classic example is the moment generated by an unbalanced force in a rotating component, causing the machinery to exhibit undesirable vibrations and reducing operational stability. Engineers must meticulously analyze and balance these moments to ensure optimal performance and longevity of machinery components.
The influence of forces and moments extends beyond mere motion; they profoundly impact the structural integrity of machinery components. Excessive forces can induce stress concentrations, leading to material fatigue and eventual failure. Engineers must meticulously calculate and analyze these forces to ensure that components can withstand operational loads and environmental conditions. Furthermore, moments can contribute to the misalignment of gears, belts, or other interconnected parts, amplifying wear and tear. Consequently, mastering the comprehension of forces and moments is indispensable for engineers seeking to enhance the reliability, safety, and efficiency of machinery.
In the pursuit of machinery design excellence, engineers employ sophisticated tools and methodologies to simulate and predict the effects of forces and moments. Finite element analysis (FEA) and computational fluid dynamics (CFD) are integral in scrutinizing how forces propagate through components and how moments influence the overall dynamics. By leveraging such advanced techniques, engineers can optimize designs, mitigate potential failures, and enhance the overall performance of machinery.
In conclusion, the nuanced understanding of forces and moments is a cornerstone in the study of dynamics of machinery. Engineers grappling with the complexities of machinery design and optimization must navigate the intricate web of forces and moments to ensure the seamless interplay of components, fostering robust, reliable, and efficient mechanical systems.
Balancing of Machinery:
Balancing of machinery is a critical aspect in mechanical engineering, playing a pivotal role in reducing vibrations and ensuring the smooth operation of rotating equipment. The importance of balancing lies in its ability to enhance the performance, longevity, and reliability of machinery by mitigating the adverse effects of uneven mass distribution.
Unbalanced machinery can lead to excessive vibrations, causing wear and tear on components, decreased efficiency, and even catastrophic failures. These vibrations not only compromise the structural integrity of the machinery but can also adversely affect the surrounding environment and personnel safety. Therefore, achieving balance in rotating machinery is imperative for optimal functionality.
Various methods and techniques are employed for balancing rotating machinery. One common approach is static balancing, which involves redistributing mass within the rotating component to eliminate the initial imbalance. This is typically achieved by adding or removing material strategically to ensure that the center of mass coincides with the axis of rotation. Static balancing is particularly effective for components with a single plane of rotation.
Dynamic balancing, on the other hand, addresses imbalances that may occur during actual operation. This method involves the use of advanced instrumentation to measure the forces and moments acting on the rotating machinery. By analyzing these measurements, engineers can identify the specific locations and magnitudes of imbalance. Counterweights are then strategically added or adjusted to achieve dynamic balance, minimizing vibrations during operation.
Furthermore, precision balancing machines are utilized in industries where stringent balance requirements are necessary. These machines are equipped with sophisticated sensors and software that can detect even minute imbalances. They provide a comprehensive analysis of the rotating component's dynamic behavior, allowing for precise adjustments to achieve optimal balance.
In some cases, auxiliary devices such as balance weights, eccentric masses, or damping systems may be employed to fine-tune the balance of rotating machinery. Additionally, advancements in technology have led to the development of computerized balancing systems, which automate the balancing process and offer real-time monitoring and adjustment capabilities.
In conclusion, the balancing of machinery is indispensable for ensuring the longevity, efficiency, and safety of rotating equipment. By addressing imbalances through methods like static and dynamic balancing, industries can significantly reduce vibrations, prevent premature wear and tear, and ultimately enhance the overall performance of their machinery. The continuous evolution of balancing techniques, coupled with technological advancements, underscores the ongoing commitment to achieving precision and reliability in mechanical systems.
Vibration Analysis:
Vibration Analysis is a crucial discipline within the realm of mechanical engineering, focusing on understanding and managing the oscillatory movements exhibited by machinery. The relevance of vibration analysis lies in its ability to provide insights into the dynamic behavior of mechanical systems, aiding in the identification of potential issues, ensuring structural integrity, and enhancing overall performance. The intricate nature of machinery often exposes it to various forces and moments, resulting in vibrations that, if unchecked, can lead to undesirable consequences.
The effects of vibrations on machinery are multifaceted and can manifest in detrimental ways. Excessive vibrations not only compromise the structural integrity of components but also contribute to accelerated wear and tear, leading to premature failure of machinery. Unchecked vibrations can propagate through the entire system, causing misalignments, resonance, and, in extreme cases, catastrophic breakdowns. Furthermore, vibrations can negatively impact the efficiency of machinery, diminishing its operational effectiveness and, in turn, affecting the overall productivity of industrial processes.
To address these challenges, engineers employ vibration analysis as a diagnostic tool to scrutinize and quantify the vibrational characteristics of machinery. This analytical approach involves the measurement and assessment of the amplitude, frequency, and phase of vibrations. Through the utilization of sensors and accelerometers strategically placed on the machinery, engineers can collect pertinent data to identify irregularities and potential sources of vibrations. Subsequently, this information is processed and analyzed using specialized software and methodologies.
Mitigating the adverse effects of vibrations entails a systematic approach based on the findings of the vibration analysis. Engineers often resort to implementing countermeasures such as damping techniques, structural modifications, and precision balancing. Damping materials are employed to absorb excess energy and diminish vibrations, while structural enhancements, like stiffening elements, help fortify vulnerable components. Precision balancing, a fundamental technique, ensures that rotating machinery components are balanced symmetrically, minimizing vibrations induced by imbalances.
In conclusion, vibration analysis serves as a cornerstone in maintaining the health and functionality of machinery. By comprehensively understanding the effects of vibrations and employing meticulous analysis techniques, engineers can proactively address issues, enhance performance, and extend the operational lifespan of machinery. This discipline not only safeguards against unexpected failures but also contributes to the optimization of industrial processes, ensuring a reliable and efficient mechanical infrastructure.
Conclusion:
In conclusion, this exploration of "Essential Concepts in Dynamics of Machinery Every Student Should Master" has illuminated the fundamental principles that serve as the backbone of mechanical engineering. Dynamics of machinery, a pivotal domain within the discipline, encompasses a comprehensive understanding of motion, forces, and moments crucial for designing and analyzing mechanical systems. We delved into the different types of motion prevalent in machinery, including translational, rotational, and oscillatory motion, highlighting their significance in diverse engineering applications.
Moreover, the distinction between kinematics and dynamics was underscored, emphasizing the crucial role dynamics plays by considering the forces and moments acting on a system. Forces and moments were discussed as key players in shaping the behavior of machinery components, underscoring their importance in the overall performance of mechanical systems. Balancing mechanisms emerged as a critical facet, with insights into methods employed to mitigate vibrations and guarantee the smooth operation of rotating machinery.
Vibration analysis took center stage, revealing its pertinence in understanding and addressing the effects of vibrations on machinery. Real-world case studies were presented as illustrative examples, demonstrating how a profound comprehension of dynamics of machinery facilitated the resolution of complex engineering challenges. These instances underscored the practical applicability of the discussed concepts in ensuring the efficacy and reliability of mechanical systems.
As future mechanical engineers embark on their educational journeys, it is paramount for them to grasp these essential concepts. Mastery of dynamics of machinery not only provides a theoretical foundation but also equips students with the practical skills required to navigate the intricacies of the field. The ability to analyze forces, understand various types of motion, and effectively address issues related to balancing and vibrations is indispensable for success in mechanical engineering.
In essence, this exploration serves as a call to action for aspiring mechanical engineers to prioritize the mastery of dynamics of machinery. The concepts elucidated herein are not mere theoretical constructs; they form the bedrock of innovation and problem-solving in the dynamic realm of mechanical engineering. As students immerse themselves in these essential principles, they lay the groundwork for a future where their expertise in dynamics of machinery propels them to meet and overcome the challenges of a rapidly evolving technological landscape. In doing so, they not only enhance their academic prowess but also contribute to the advancement and sustainability of the engineering field as a whole.