CREO for Professionals: Advanced Techniques to Elevate Your Skills
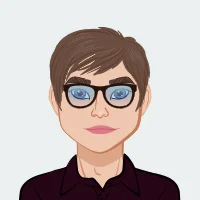
CREO, developed by PTC, stands as a preeminent parametric computer-aided design (CAD) software suite widely employed in the realm of mechanical engineering. Its name, derived from the term "Create," encapsulates its primary objective: to empower engineers and designers to bring innovative concepts to life. CREO offers a robust set of tools for 3D modeling, simulation, analysis, and collaboration, making it a cornerstone in the product development process. If you need help with your CREO assignment, understanding the capabilities of CREO in mechanical engineering can provide valuable insights and strategies to enhance your proficiency in utilizing this software for your assignments.
In the dynamic landscape of mechanical engineering, where innovation is relentless and designs are ever-evolving, the significance of CREO cannot be overstated. The software's parametric modeling capabilities allow engineers to create precise and scalable 3D models, offering a holistic view of a product's design and behavior. This parametric approach not only enhances accuracy but also facilitates quick modifications, enabling engineers to adapt designs swiftly in response to changing requirements or unforeseen challenges.
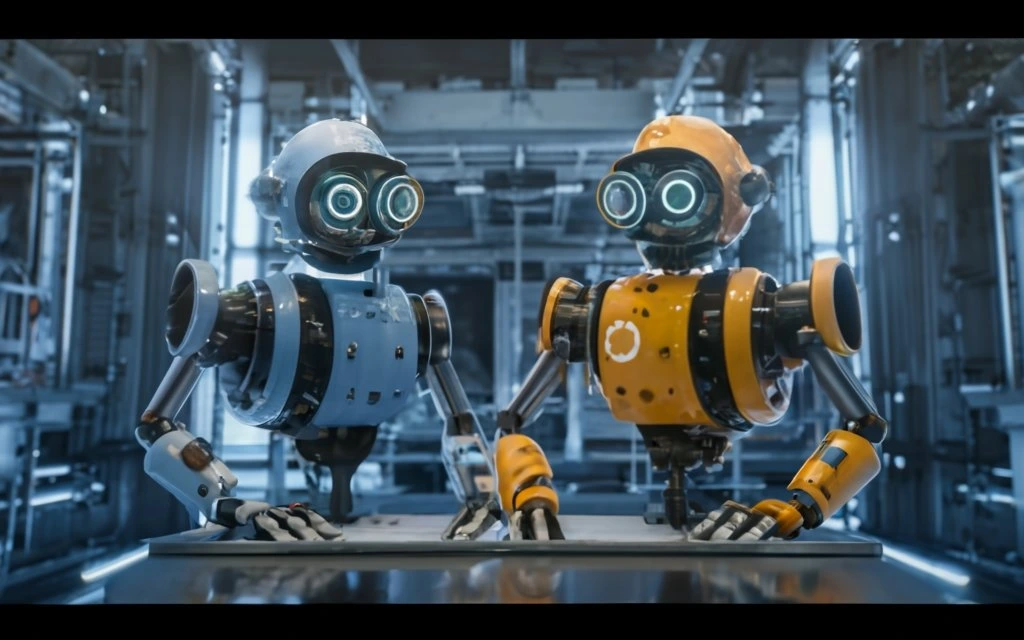
Staying abreast of advanced techniques in CREO is imperative for professionals in the field. The software continually evolves, introducing cutting-edge features and functionalities that can significantly enhance efficiency and productivity. Advanced modeling techniques within CREO, such as parametric design and feature-based modeling, empower engineers to create intricate designs with unparalleled precision. This not only streamlines the product development cycle but also ensures that the end result aligns with the highest standards of quality.
Furthermore, CREO's simulation and analysis capabilities play a pivotal role in validating designs before they reach the physical prototype stage. Professionals can employ CREO to subject their models to rigorous testing, evaluating factors like stress, strain, and thermal performance. This not only minimizes the risk of design flaws but also contributes to cost and time savings, as iterations can be made in the digital realm before physical prototypes are produced.
In the collaborative landscape of contemporary engineering projects, CREO excels. Its integration features facilitate seamless collaboration among team members, allowing for real-time sharing and modification of designs. This collaborative environment fosters innovation and ensures that the collective expertise of a team is harnessed to its full potential. Additionally, CREO's compatibility with other widely used tools and software in the industry enhances its utility, making it an integral part of the interconnected ecosystem of modern engineering workflows.
As technology advances and industries become more interconnected, the importance of continuous learning and skill development cannot be overstated. For professionals in mechanical engineering, embracing and mastering advanced techniques in CREO is not just a matter of staying competitive—it's a strategic imperative. By staying updated with the latest features and functionalities, engineers and designers can position themselves at the forefront of innovation, contributing to the creation of cutting-edge products and solutions.
In conclusion, CREO stands as a cornerstone in mechanical engineering, offering a comprehensive suite of tools that empower professionals to bring their design visions to life. The software's significance lies not only in its foundational capabilities but also in its commitment to evolving with the dynamic needs of the industry. For professionals, the journey of mastering CREO is a continuous one—a commitment to staying at the forefront of innovation and ensuring that their skills remain as dynamic as the designs they bring to fruition.
Overview of CREO:
CREO, developed by PTC, is a powerful parametric computer-aided design (CAD) software widely utilized in mechanical engineering for product design and development. At its core, CREO employs a parametric modeling approach, allowing engineers to create 3D models that are not only geometrically accurate but also driven by parameters, enabling swift modifications and adaptability to design changes.
The software boasts a comprehensive set of features that cater to the diverse needs of mechanical engineers. CREO's 3D modeling capabilities are robust, encompassing both solid and surface modeling techniques. Engineers can leverage parametric design features, such as constraints and relationships, to establish and maintain design intent throughout the development process. Furthermore, CREO offers advanced simulation and analysis tools, enabling professionals to assess the structural integrity, thermal performance, and overall behavior of their designs before physical prototypes are produced.
One of CREO's distinguishing features is its versatility in handling complex assemblies. The software facilitates the creation and management of intricate assemblies with ease, allowing engineers to simulate the interactions between components and assess the overall functionality of a product. Additionally, CREO supports collaborative design with its integrated tools, enabling real-time collaboration among team members, which is crucial in multidisciplinary projects.
Mastering CREO is essential for professionals in the field of mechanical engineering due to several compelling reasons. Firstly, the parametric modeling approach in CREO allows engineers to create designs that are not only accurate but also easily modifiable. This adaptability is vital in an industry where design changes and iterations are common, ensuring that engineers can efficiently respond to evolving project requirements and challenges.
Secondly, the simulation and analysis capabilities of CREO contribute significantly to the reduction of design errors and the optimization of products. Professionals can conduct thorough virtual tests on their designs, identifying potential issues and refining their work before moving to the costly and time-consuming physical prototyping stage. This results in a more streamlined product development process and ultimately leads to higher-quality end products.
Moreover, the collaborative features of CREO enhance teamwork and communication among engineering professionals. In today's interconnected work environment, where projects often involve teams distributed across locations, CREO facilitates seamless collaboration, ensuring that the collective expertise of a team is effectively harnessed.
In conclusion, CREO stands as a comprehensive CAD solution with features tailored to the intricate demands of mechanical engineering. The software's ability to support parametric modeling, advanced simulation, and collaborative design makes it indispensable for professionals in the field. Mastering CREO equips engineers with the tools to navigate the complexities of modern product development, ensuring efficiency, accuracy, and innovation in their designs.
Advanced Modeling Techniques:
In CREO, advanced 3D modeling techniques go beyond the basics, offering engineers sophisticated tools to create complex and intricate designs with precision. One notable feature is parametric design, a cornerstone of CREO's modeling capabilities. Parametric design allows engineers to establish relationships and constraints between different elements of a model, ensuring that modifications automatically propagate throughout the design. This parametric approach enhances efficiency in product development by providing a streamlined and flexible workflow.
Parametric design in CREO enables engineers to set parameters for dimensions, angles, and relationships between components. For example, if the length of a specific feature is defined as a parameter, changing that parameter automatically adjusts the length throughout the entire model. This not only ensures consistency in the design but also expedites the modification process, allowing engineers to experiment with different iterations quickly.
To illustrate the impact of advanced modeling techniques in CREO, consider a case study in the automotive industry. An automotive design team, using parametric design in CREO, can create a 3D model of a vehicle where parameters such as wheelbase, overall length, and ground clearance are defined. If the team receives feedback to increase the wheelbase for better stability, they can easily modify the corresponding parameter in CREO. The software then automatically adjusts the entire model, ensuring that all components adapt accordingly. This rapid iteration process is crucial in meeting tight deadlines and responding swiftly to design changes without compromising accuracy.
In the aerospace sector, advanced 3D modeling in CREO plays a pivotal role in designing intricate components such as turbine blades. Engineers can employ parametric design to define the critical dimensions and relationships governing the blade's shape. If there's a need to optimize the blade for improved aerodynamics or structural integrity, parametric design allows for seamless adjustments, ensuring that the modifications ripple through the entire model. This capability is indispensable for achieving precision in manufacturing and meeting stringent performance requirements.
In summary, advanced 3D modeling techniques in CREO, particularly through the use of parametric design, empower engineers to efficiently navigate the complexities of product development. The ability to establish and modify parameters enhances flexibility, reduces design errors, and accelerates the iteration process. Real-world examples in industries like automotive and aerospace underscore the tangible benefits of these advanced modeling techniques, demonstrating how CREO facilitates innovation and efficiency in product design and development.
Simulation and Analysis:
CREO's role in simulation and analysis is integral to ensuring the structural integrity, performance, and reliability of mechanical designs. Simulation tools within CREO empower professionals to assess the behavior of their designs under various conditions, facilitating informed decision-making throughout the product development process.
Professionals can leverage CREO's simulation capabilities to optimize designs by subjecting them to virtual testing scenarios. For instance, in the automotive industry, engineers can simulate the impact of different forces and loads on vehicle components, ensuring that they meet safety standards and perform optimally. This process allows for the identification of potential weaknesses or areas for improvement before physical prototypes are produced, significantly reducing the likelihood of design flaws.
The optimization process in CREO involves fine-tuning designs based on simulation results. For example, in the aerospace sector, engineers can use simulation tools to analyze the stress distribution on aircraft components during flight. By identifying areas of high stress or potential failure, adjustments can be made to the design, such as altering material thickness or redistributing loads. This iterative optimization ensures that designs meet performance requirements while minimizing unnecessary weight or material usage.
Real-world examples underscore the efficacy of simulation in CREO. Consider a case where a robotics company used CREO's simulation tools to analyze the stress and strain on a robotic arm's joints. By simulating the range of motion and external forces the arm would encounter in various tasks, engineers were able to identify and address potential issues before manufacturing. The result was a more robust and reliable robotic arm, demonstrating how simulation in CREO contributed to the successful development of a high-performance product.
In the realm of consumer electronics, a smartphone manufacturer utilized CREO's simulation capabilities to analyze the thermal performance of a new device. Simulating heat dissipation under different usage scenarios allowed engineers to optimize the placement of components and the design of the device's casing to prevent overheating. This preemptive optimization not only ensured the reliability of the product but also enhanced its overall user experience.
In conclusion, CREO's simulation and analysis tools play a pivotal role in the mechanical design process, enabling professionals to optimize their designs for performance, reliability, and efficiency. Through virtual testing and iterative refinement, engineers can identify and address potential issues early in the development cycle, resulting in successful outcomes and the creation of high-quality, innovative products. The real-world examples underscore the practical impact of CREO's simulation capabilities, showcasing how the software contributes to the success of projects across diverse industries.
Collaboration and Integration:
CREO excels in fostering collaboration among team members, offering a suite of features that streamline communication and enhance teamwork in mechanical design projects. One of the key collaborative features is real-time co-editing, allowing multiple team members to work on the same design simultaneously. This fosters a dynamic and iterative workflow, where changes made by one team member are instantly visible to others, promoting a seamless exchange of ideas and rapid decision-making.
Additionally, CREO provides version control and change tracking mechanisms. These features allow team members to track modifications made to the design, understand the evolution of the project, and revert to previous versions if necessary. This ensures that the collaborative process remains organized and transparent, preventing misunderstandings and facilitating a smoother workflow.
CREO's integration capabilities further enhance collaboration by allowing seamless interaction with other tools and software commonly used in the industry. For instance, the software integrates smoothly with Product Lifecycle Management (PLM) systems, enabling efficient data exchange and centralized management of design information. This integration ensures that all team members have access to the latest design data, fostering a cohesive and synchronized development process.
Furthermore, CREO supports interoperability with Computer-Aided Engineering (CAE) and Computer-Aided Manufacturing (CAM) tools. This interconnectedness enables a more comprehensive approach to product development, where design, analysis, and manufacturing processes are seamlessly linked. For instance, a design engineer using CREO can collaborate seamlessly with a simulation engineer using a CAE tool, ensuring that design modifications are made in consideration of simulation results, leading to more robust and optimized products.
To maximize efficiency through collaborative features in CREO, teams can adopt several best practices. Establishing clear communication channels within the software, such as commenting on specific features or using built-in messaging tools, enhances real-time collaboration. Utilizing the software's notification system ensures that team members are alerted to changes or updates promptly. Regularly conducting design reviews and collaborative sessions within CREO can foster a shared understanding of project goals and requirements.
In conclusion, CREO's collaborative features and integration capabilities are instrumental in promoting teamwork and efficiency in mechanical design projects. The software's real-time co-editing, version control, and integration with industry-standard tools facilitate a collaborative environment where team members can work seamlessly together, leading to more innovative and successful outcomes. Implementing best practices and leveraging these collaborative features allows teams to unlock the full potential of CREO in driving collaborative excellence in mechanical engineering projects.
Tips and Tricks for Efficiency:
Efficient utilization of CREO involves mastering a range of tips, tricks, and lesser-known features that can significantly enhance productivity for professionals in mechanical engineering. One of the quickest ways to boost efficiency is by incorporating keyboard shortcuts into your workflow. CREO offers a plethora of keyboard shortcuts that expedite common actions. For instance, 'Ctrl + E' in sketch mode brings up the extrude dialog, while 'Ctrl + Q' regenerates the model, saving valuable time over navigating through menus.
Exploring lesser-known features within CREO can uncover powerful tools that streamline tasks. The "Flexible Modeling" feature, for example, allows engineers to make modifications to imported geometry with ease, adapting to changes in project requirements swiftly. Additionally, the "Family Tables" feature enables the creation of multiple variations of a part within a single model, minimizing redundancy and simplifying design management.
Workflow optimizations play a crucial role in efficiency gains. Utilizing the "ModelCHECK" tool helps maintain consistency in designs by automatically checking for adherence to company standards and best practices. Moreover, employing "Skeleton Models" for complex assemblies can serve as a foundation, providing a skeletal structure that ensures components fit together seamlessly, minimizing errors during the assembly process.
Continuous learning and exploration of new functionalities within CREO are paramount for professionals seeking to stay at the forefront of their field. Regularly attending training sessions, webinars, or pursuing advanced courses can uncover hidden gems within CREO's toolset. For instance, the "Style" feature, often overlooked, enables engineers to create aesthetically pleasing and ergonomically efficient designs. Additionally, staying informed about software updates ensures access to the latest enhancements and features, offering new ways to approach design challenges.
Encouraging a mindset of exploration and curiosity is essential. Engineers should actively experiment with different functionalities, attempting to solve problems in innovative ways. CREO's extensive online community and forums provide a valuable resource for learning from others, sharing tips, and addressing challenges collaboratively.
In conclusion, professionals can significantly enhance their efficiency with CREO by incorporating keyboard shortcuts, exploring lesser-known features, and optimizing their workflows. The software's vast array of tools offers ample opportunities for creativity and problem-solving. Continuous learning and a commitment to staying informed about new functionalities ensure that engineers harness the full potential of CREO in their mechanical engineering endeavors. Embracing these tips and fostering a culture of ongoing exploration not only boosts individual efficiency but contributes to the collective innovation within the mechanical engineering community.
Conclusion:
In summary, the blog post delves into the significance of advanced techniques in CREO for professionals in the field of mechanical engineering. It highlights CREO's role in 3D modeling, simulation, and collaboration, emphasizing its crucial impact on product development. The discussion extends to the importance of parametric design, showcasing its efficiency in adapting to changes and optimizing designs. The integration capabilities of CREO with other industry-standard tools further enhance collaboration, ensuring a cohesive approach to mechanical design projects. Practical tips, such as keyboard shortcuts and lesser-known features, are provided to boost efficiency. The narrative underscores that continuous learning and skill development are paramount in the ever-evolving landscape of mechanical engineering.
Emphasizing the importance of continuous learning and skill development is crucial for professionals in mechanical engineering. In a dynamic field where technological advancements are rapid, staying ahead requires a proactive approach to acquiring new knowledge and honing existing skills. CREO, being a versatile and evolving tool, serves as a prime example. Continuous learning not only enhances proficiency in using CREO's features but also enables professionals to adapt to emerging technologies and methodologies. This commitment to learning is not just a career strategy but a necessity for remaining competitive and contributing meaningfully to the innovative landscape of mechanical engineering.
The blog encourages readers to explore advanced techniques in CREO as a means to stay ahead in their professional careers. Acknowledging the software's pivotal role in mechanical design, professionals are urged to delve into its intricacies, from advanced 3D modeling to simulation and collaboration features. The narrative reinforces that embracing these advanced techniques is not merely an option but a strategic move to differentiate oneself in a competitive industry. By actively seeking out and mastering new functionalities within CREO, professionals position themselves as valuable assets, capable of tackling complex challenges and driving innovation in mechanical engineering.
In conclusion, the blog post serves as a comprehensive guide for professionals in mechanical engineering, highlighting the indispensable role of CREO's advanced techniques. The emphasis on continuous learning underscores its pivotal role in staying relevant and competitive. The call to explore advanced techniques in CREO is a rallying cry for professionals to invest in their skills, ensuring they not only keep pace with industry trends but also lead the way in shaping the future of mechanical engineering.