Cracking Mechanical Engineering Problems with Abaqus: A Student's Handbook
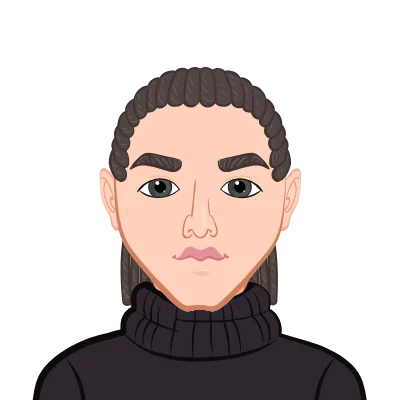
Abaqus, a powerful finite element analysis (FEA) software suite developed by Dassault Systèmes, stands as a cornerstone in the realm of mechanical engineering. Renowned for its versatility and robust simulation capabilities, Abaqus has become an indispensable tool for engineers and researchers alike. Its significance lies in its ability to simulate and analyze complex physical behaviors of structures, components, and materials under various conditions. This software is instrumental in predicting the performance and response of designs, aiding in the optimization of mechanical systems across industries.
In the dynamic landscape of mechanical engineering education, students encounter multifaceted challenges when confronted with real-world problems. One of the primary hurdles lies in bridging the gap between theoretical knowledge and practical application. While academic curricula provide a foundational understanding of engineering principles, students often find themselves grappling with the complexities of translating these concepts into viable solutions for actual engineering problems. This is where Abaqus emerges as a crucial ally, offering a virtual platform for students to apply their theoretical knowledge in a hands-on manner.
Another challenge faced by students is the inherent complexity of mechanical systems. Real-world engineering problems are seldom linear or straightforward, often involving intricate interactions between various components and forces. The sheer diversity and intricacy of these challenges can be overwhelming, requiring students to navigate through a maze of uncertainties. Abaqus, with its advanced simulation capabilities, empowers students to dissect and analyze these complex problems systematically. It allows them to model intricate geometries, apply various loads and boundary conditions, and predict the behavior of structures under diverse scenarios.
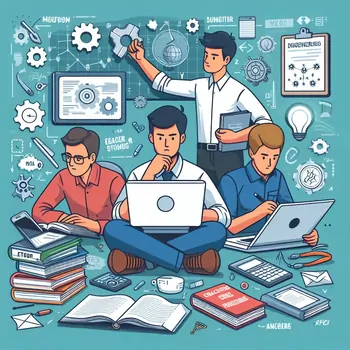
Moreover, the integration of interdisciplinary knowledge poses a significant challenge for students in solving mechanical engineering problems. Mechanical systems are inherently interdisciplinary, involving principles from materials science, physics, and mathematics. Students must synthesize knowledge from different domains to develop comprehensive solutions. Abaqus facilitates this integration by providing a unified platform where students can explore the interplay of various factors influencing the performance of a mechanical system.
Despite the potential benefits of Abaqus, there exists a learning curve that students must navigate. Mastering the intricacies of the software demands time, practice, and a solid understanding of the underlying engineering principles. Students often face challenges in transitioning from theory to application, understanding the nuances of simulation settings, and interpreting the results accurately. However, overcoming these challenges is not only a testament to the student's growth but also a testament to the indispensable nature of Abaqus in fostering a deeper understanding of mechanical engineering concepts.
In conclusion, Abaqus stands as a linchpin in the landscape of mechanical engineering education, providing students with a virtual laboratory to confront and conquer real-world challenges, including how to solve your Abaqus assignment. The software's significance lies in its capacity to bridge the gap between theoretical knowledge and practical application, offering a dynamic platform for students to explore, analyze, and optimize mechanical systems. While challenges persist, the mastery of Abaqus equips students with invaluable skills, preparing them for the complexities of modern engineering practices.
Understanding Abaqus
Abaqus, developed by Dassault Systèmes, is a comprehensive finite element analysis (FEA) software that has garnered widespread acclaim in the field of engineering simulation. Offering a sophisticated and versatile platform, Abaqus enables engineers and researchers to model, simulate, and analyze the behavior of complex mechanical systems under a diverse range of conditions. Its key features and capabilities distinguish it as a preferred choice for professionals engaged in structural, thermal, and multiphysics simulations.
One of the standout features of Abaqus is its robust modeling capabilities. The software allows users to create intricate three-dimensional models of structures, components, and materials, capturing the complexities of real-world systems with precision. Abaqus supports various element types, ensuring flexibility in modeling different geometries and materials. This versatility is particularly beneficial when dealing with diverse engineering applications, from aerospace components to biomedical devices.
Abaqus is renowned for its advanced material modeling capabilities. Engineers can simulate the behavior of materials under various loading conditions, including nonlinear and time-dependent responses. This feature is invaluable in predicting the performance of structures subjected to complex mechanical forces and thermal gradients. Furthermore, Abaqus excels in multiphysics simulations, enabling the coupling of different physical phenomena such as structural mechanics, heat transfer, and fluid dynamics. This holistic approach allows engineers to comprehensively analyze the interactions between various aspects of a system.
The software's simulation capabilities extend to dynamic analyses, offering insights into the transient behavior of structures subjected to impact, vibration, or other time-dependent forces. Abaqus also supports fatigue analysis, aiding in the assessment of a structure's durability under cyclic loading. The inclusion of pre-processing and post-processing tools enhances the overall user experience, allowing for efficient model setup and detailed visualization of simulation results.
For those embarking on the journey of learning Abaqus, an array of resources is available to facilitate the process. Dassault Systèmes provides comprehensive documentation, including user manuals and guides, offering in-depth insights into the software's functionalities. Additionally, an extensive collection of tutorials caters to users at different proficiency levels, guiding them through the steps of creating models, defining boundary conditions, and interpreting results. Online forums and communities provide a platform for users to exchange knowledge, seek assistance, and stay updated on best practices.
In conclusion, Abaqus stands as a pinnacle in the realm of engineering simulation, offering a rich set of features and capabilities that empower users to tackle complex mechanical challenges. Its modeling prowess, material simulation capabilities, and support for multiphysics analyses make it a versatile tool for a wide range of applications. With ample learning resources available, Abaqus not only facilitates efficient simulations but also nurtures a community of practitioners dedicated to advancing their understanding of engineering through the power of simulation.
Common Mechanical Engineering Problems
Mechanical engineering assignments often present students with a spectrum of challenges that mirror the diverse and intricate nature of the field. One common problem revolves around structural analysis and design. Students may grapple with the task of optimizing a structure for maximum strength while adhering to constraints such as material limitations and budgetary considerations. For instance, designing a bridge that can withstand varying loads, environmental conditions, and dynamic forces requires a deep understanding of structural mechanics.
Another prevalent challenge is thermal analysis, where students need to predict how a mechanical system will respond to heat and thermal gradients. This could involve designing a cooling system for electronic components or assessing the thermal stability of an engine. The complexity arises from the need to consider material properties, heat transfer mechanisms, and the impact of temperature on various components.
Fluid dynamics poses another set of common challenges. Whether it's designing an efficient pump system, analyzing airflow around an aircraft wing, or optimizing the performance of a hydraulic system, students often encounter difficulties in predicting fluid behavior accurately. The intricacies of fluid flow, turbulence, and pressure distribution make these assignments demanding.
Mechanical vibrations and dynamics represent a perpetual challenge in the field. Students may need to analyze and mitigate vibrations in structures or mechanical systems to prevent failure and ensure optimal performance. For example, designing a stable foundation for a rotating machine to minimize vibrations requires a nuanced understanding of structural dynamics.
Material selection and optimization constitute a fundamental yet challenging aspect of mechanical engineering assignments. Students must choose materials that meet specific criteria, such as strength, durability, and cost-effectiveness. Optimizing the material for a given application, like selecting the appropriate alloy for an aerospace component to balance weight and strength, demands a meticulous approach.
Simulation and modeling using tools like Abaqus, as previously discussed, introduce their own set of challenges. Translating real-world scenarios into accurate simulations requires a deep understanding of both the engineering principles and the software's functionalities. Ensuring that simulation results align with physical reality and making informed design decisions based on these simulations are ongoing challenges in the field.
In conclusion, common mechanical engineering problems in assignments span structural analysis, thermal considerations, fluid dynamics, vibrations, material selection, and simulation. Tackling these challenges requires a holistic understanding of engineering principles, interdisciplinary knowledge, and the ability to apply theoretical concepts to practical scenarios. Providing students with illustrative examples and guiding them through these multifaceted problems is crucial in fostering their problem-solving skills and preparing them for the complexities of the mechanical engineering profession.
Tips and Tricks
Efficiently solving mechanical engineering problems using Abaqus requires a thoughtful and systematic approach, blending technical proficiency with strategic application. To begin, it is crucial to have a thorough understanding of the engineering problem at hand, delineating objectives, constraints, and expected outcomes. This foundational clarity serves as a guide throughout the simulation process. A recommended strategy is to commence with simpler models, progressively advancing to more complex ones. This incremental approach facilitates the assimilation of fundamental concepts and fosters confidence in navigating the intricacies of the software.
Mesh optimization stands as a pivotal aspect of effective problem-solving with Abaqus. Striking a balance between mesh density and computational efficiency is imperative. Initiating with a coarse mesh and refining it strategically in areas of interest—such as stress concentrations or regions with high deformation—ensures a judicious use of computational resources while maintaining simulation accuracy. Convergence monitoring holds equal significance; staying vigilant and addressing convergence issues promptly is essential. These issues often arise from improper settings or inadequate mesh refinement, necessitating a nuanced troubleshooting approach.
Accurate representation of boundary conditions is a cornerstone of successful simulations. Incorrectly applied constraints or loads can lead to unrealistic results, underscoring the need for regular validation and adjustment. Leveraging the wealth of resources provided by Dassault Systèmes, including Abaqus documentation and tutorials, proves invaluable for users seeking self-guided learning and troubleshooting. These resources offer comprehensive insights into Abaqus functionalities and guide users through diverse simulations.
Interpreting simulation results is the final, critical step in the process. Utilizing Abaqus' visualization tools to analyze stress patterns, deformation, and other relevant parameters is essential. However, a discerning eye is necessary to discern realistic outcomes from anomalies. Validation against fundamental engineering principles ensures that simulation results align with the physical behavior expected in real-world scenarios.
Incorporating these tips into the workflow not only enhances the efficiency of problem-solving with Abaqus but also addresses common challenges faced by students and practitioners. It fosters a more profound understanding of the intricacies of mechanical engineering simulations, empowering users to tackle complex problems with confidence and precision.
Case Studies
In the realm of mechanical engineering problem-solving, Abaqus has been instrumental in addressing complex challenges across various industries. One notable case study involves the aerospace sector, where engineers utilized Abaqus to simulate and analyze the structural integrity of an innovative aircraft wing design. The methodology involved creating a detailed three-dimensional model of the wing, incorporating materials with nonlinear properties to simulate realistic conditions. Challenges were multifaceted, including the need to accurately represent aerodynamic loads, turbulence effects, and dynamic forces. The simulation process demanded a careful calibration of the finite element model and meticulous meshing to capture intricate geometries. The outcome was a comprehensive understanding of the wing's structural behavior under diverse flight scenarios, enabling engineers to refine the design for optimal strength and weight distribution.
In the automotive industry, Abaqus played a pivotal role in a case study focused on crashworthiness analysis for a new vehicle model. The methodology entailed creating a virtual prototype of the vehicle and subjecting it to various crash scenarios, simulating impacts from different angles and speeds. Challenges encompassed modeling complex interactions between vehicle components, accurately representing material properties, and predicting the behavior of safety systems. The simulation results provided crucial insights into areas of potential vulnerability and allowed engineers to enhance the vehicle's crash resistance, contributing to improved safety standards.
In the field of renewable energy, a case study demonstrated how Abaqus was employed to optimize the design of a wind turbine blade. The methodology involved modeling the composite materials used in the blade and simulating the response to varying wind conditions. Challenges included capturing the nonlinearity of materials, predicting fatigue life, and optimizing the blade's shape for maximum energy extraction. Through iterative simulations, engineers were able to refine the blade design, improving its structural integrity and overall performance in real-world wind conditions.
These case studies underscore the versatility of Abaqus in tackling diverse challenges within mechanical engineering. The methodology consistently involves creating detailed finite element models, addressing complex interactions, and refining designs through iterative simulations. Challenges often revolve around accurately representing real-world conditions and optimizing models for computational efficiency. The outcomes, however, are transformative—enhanced structural designs, improved safety standards, and optimized performance in critical applications across industries. The success stories highlight Abaqus as a go-to solution for engineers navigating the complexities of mechanical engineering problems in diverse and demanding real-world scenarios.
Conclusion:
In the exploration of the blog post, "Cracking Mechanical Engineering Problems with Abaqus: A Student's Handbook," several key takeaways emerge as pivotal for students embarking on the journey of mechanical engineering problem-solving. Abaqus, the finite element analysis (FEA) software, stands as a versatile ally, offering a virtual laboratory for students to apply theoretical knowledge to practical scenarios. It empowers students to tackle common challenges in mechanical engineering assignments, from structural and thermal analyses to fluid dynamics and material optimization. The software's capabilities span diverse simulations, providing a holistic approach to problem-solving in the field. The step-by-step guidance outlined in the blog post elucidates the process of utilizing Abaqus for various types of problems, emphasizing the importance of understanding the problem thoroughly, starting with simple models, optimizing mesh density, and monitoring convergence. Furthermore, the post underscores the significance of accurate boundary conditions, effective material modeling, and the interpretation of results for a comprehensive understanding of simulated scenarios. Real-life case studies showcase Abaqus in action, addressing complex challenges in aerospace, automotive, and renewable energy industries. The methodologies employed in these case studies involve creating detailed finite element models, addressing intricate interactions, and refining designs through iterative simulations. Challenges faced range from accurately representing real-world conditions to optimizing models for computational efficiency. However, the outcomes are transformative—enhanced structural designs, improved safety standards, and optimized performance in critical applications across industries. The blog post concludes with a call to action, encouraging students to not only absorb the theoretical insights but to actively apply the knowledge gained in their assignments. This application serves as a crucial bridge between academic learning and practical problem-solving, fostering a deeper understanding of engineering principles. By engaging with Abaqus and navigating through simulated scenarios, students can hone their analytical skills, develop a proficiency in using simulation tools, and cultivate a problem-solving mindset crucial for success in the dynamic field of mechanical engineering. The journey from theory to application, guided by the insights provided in the blog, empowers students to crack mechanical engineering problems effectively and prepares them for the multifaceted challenges of the engineering profession.