CATIA V5 vs. CATIA V6: Which Version Is Right for Your Mechanical Engineering Assignments?
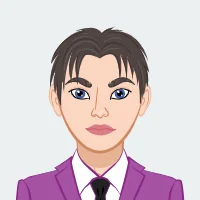
CATIA, a robust software suite extensively used in mechanical engineering, offers two prominent versions: CATIA V5 and CATIA V6. The decision between these versions significantly influences the efficiency of completing your CATIA assignments.
In the ever-evolving landscape of mechanical engineering, proficiency in Computer-Aided Design (CAD) software is paramount. Among the plethora of CAD tools, CATIA stands out as a comprehensive suite that has become synonymous with precision and innovation. As mechanical engineering students and professionals navigate the intricate realm of CATIA, a pivotal decision awaits them: CATIA V5 or CATIA V6? This blog seeks to unravel the intricacies of these two versions, guiding you through a nuanced exploration of their features, capabilities, and applicability to mechanical engineering assignments.
CATIA, an acronym for Computer-Aided Three-Dimensional Interactive Application, was initially developed by Dassault Systems in the late 1970s. Since its inception, CATIA has transformed the design and manufacturing processes across various industries, including automotive, aerospace, and consumer goods. Its robust capabilities have made it an indispensable tool for engineers, enabling them to conceptualize, design, and simulate complex mechanical systems with unparalleled precision.
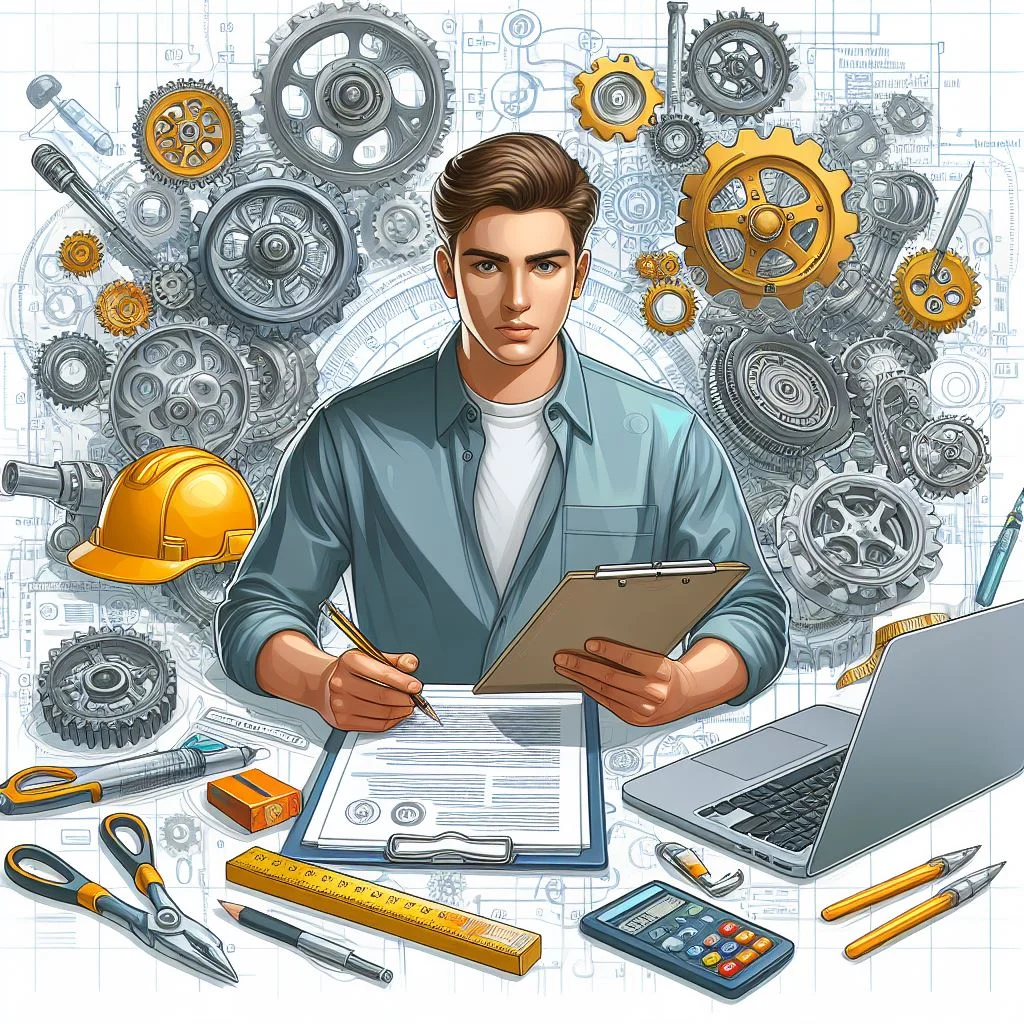
CATIA V5, the fifth iteration of this venerable software, has been a stalwart companion for mechanical engineers for over two decades. Its longevity in the industry speaks volumes about its reliability and effectiveness. CATIA V5 offers a user-friendly interface coupled with a rich feature set that caters to the diverse needs of mechanical design. From parametric modeling to assembly design and drafting, V5 has been the go-to choose for professionals and students alike.
Key features of CATIA V5 include parametric modeling, robust assembly capabilities, surface modeling, and a comprehensive set of drafting tools. The software's parametric capabilities allow engineers to create designs that can be easily modified by adjusting parameters, providing flexibility and efficiency in the design process. The assembly design features facilitate the creation and management of complex assemblies, a crucial aspect of mechanical engineering projects.
As technology continues to advance, so does the need for more sophisticated tools to meet the demands of modern engineering challenges. Enter CATIA V6, positioned as the next evolution in the CATIA lineage. V6 represents a paradigm shift from its predecessor, introducing a host of new features and improvements.
One of the standout features of CATIA V6 is its emphasis on collaborative and cloud-based design. V6 facilitates real-time collaboration among team members, enabling seamless communication and coordination in the design process. This collaborative approach is particularly advantageous for large-scale projects where multiple engineers contribute to the overall design.
V6 also introduces advancements in generative design, simulation, and analysis capabilities. The software's ability to leverage cloud computing resources enhances performance and enables engineers to tackle complex simulations with ease. These enhancements position CATIA V6 as a powerful tool for tackling intricate mechanical engineering challenges that demand cutting-edge simulation and analysis capabilities.
The choice between CATIA V5 and V6 is not a one-size-fits-all decision. It hinges on several factors, including the nature of the mechanical engineering assignments, the preferences of the design team, and the specific requirements of the industry. Each version has its strengths, and understanding these nuances is crucial for making an informed decision.
Overview of CATIA V5:
CATIA V5, a stalwart in the realm of Computer-Aided Design (CAD), has been a cornerstone for mechanical engineers and designers for over two decades. Its robust suite of tools and features has played a pivotal role in shaping the landscape of mechanical design, offering a comprehensive solution for conceptualization, modeling, and simulation. In this detailed overview, we will delve into the key facets of CATIA V5, exploring its user interface, core features, and real-world applications.
At the heart of CATIA V5 lies a user-friendly interface that strikes a balance between sophistication and accessibility. The interface is intuitively designed, allowing both novice users and seasoned professionals to navigate the software with ease. The modular layout enables users to access a plethora of tools organized into workbenches, each tailored for specific tasks such as Part Design, Assembly Design, and Drafting.
The Part Design workbench is the hub for 3D parametric modeling, empowering engineers to create intricate designs with precision. With a robust set of sketching, modeling, and analysis tools, CATIA V5 excels in facilitating the creation of complex geometries, from simple components to intricate assemblies.
Parametric modeling is a cornerstone feature of CATIA V5, providing engineers with the flexibility to make design changes seamlessly. The parametric capabilities enable the creation of designs driven by parameters, allowing for quick and efficient modifications. This feature proves invaluable in scenarios where design iterations are frequent, ensuring that changes are propagated throughout the model effortlessly.
The associativity in CATIA V5 ensures that modifications made in one part of the design are automatically reflected in related components and assemblies. This interconnectedness streamlines the design process, reducing errors and enhancing the overall efficiency of the engineering workflow.
CATIA V5's Assembly Design workbench empowers engineers to create and manage complex assemblies with precision. The software offers a range of assembly constraints and tools for collision detection, ensuring that components fit seamlessly within the overall design. The capability to simulate and analyze assembly kinematics provides engineers with insights into the functionality and performance of the designed systems.
The kinematics capabilities allow engineers to explore how parts within an assembly move relative to each other. This is crucial for validating the functionality of mechanisms, detecting interferences, and ensuring that the designed systems operate as intended. CATIA V5's assembly tools are indispensable for industries where the intricate interplay of components is a critical aspect of the overall design.
CATIA V5's surface modeling capabilities extend its design capabilities to the creation of complex, aesthetically pleasing surfaces. Engineers can craft freeform surfaces, ideal for designing products with sleek and ergonomic shapes. From automotive exteriors to consumer electronics, the surface modeling tools in CATIA V5 cater to a diverse array of design requirements.
The software's ability to seamlessly integrate surface and solid modeling allows engineers to create holistic designs that marry form and function. This is particularly beneficial in industries where the visual appeal of a product is as crucial as its performance.
In the realm of mechanical design, effective communication is paramount. CATIA V5 addresses this need with a robust set of drafting tools that facilitate the creation of detailed and accurate engineering drawings. The drafting workbench allows engineers to generate 2D drawings with annotations, dimensions, and other essential details.
CATIA V5's drafting capabilities are not merely a supplementary feature but an integral part of the design process. The seamless transition from 3D modeling to 2D documentation ensures that engineers can communicate their design intent effectively. Whether creating assembly instructions or collaborating with other stakeholders, the drafting tools in CATIA V5 enhance the clarity and precision of design documentation.
The versatility of CATIA V5 is evident in its widespread adoption across various industries. In the automotive sector, CATIA V5 is the tool of choice for designing complex automotive components and systems. In the aerospace and defense sector, CATIA V5 plays a pivotal role in designing aircraft components and systems. Its ability to handle large assemblies and complex geometry makes it an indispensable tool for engineers working on projects with stringent safety and performance standards.
Overview of CATIA V6:
In the dynamic realm of mechanical engineering, staying at the forefront of technological advancements is paramount. CATIA V6, the latest iteration of the renowned Computer-Aided Design (CAD) software, represents a paradigm shift in how engineers approach design, collaboration, and innovation. In this comprehensive overview, we will explore the key features, capabilities, and real-world applications of CATIA V6, shedding light on its transformative impact on the field of mechanical design.
CATIA V6 builds upon the legacy of its predecessor, V5, introducing a host of new features and capabilities that respond to the evolving needs of modern engineering challenges. The transition from V5 to V6 signifies a shift towards a more collaborative, cloud-based, and data-centric design approach. This evolution is not merely an incremental update; it represents a holistic reimagining of how engineers conceptualize, design, and bring ideas to life.
One of the standout features of CATIA V6 is its emphasis on collaborative design, leveraging the power of the cloud to enhance teamwork and communication. In the traditional design workflow, collaboration often involves exchanging files and managing version control, leading to potential inefficiencies and errors. CATIA V6 addresses this challenge by providing a platform where multiple users can work on a design simultaneously, fostering real-time collaboration.
The cloud-based design environment in CATIA V6 enables engineers to access and work on projects from anywhere in the world, breaking down geographical barriers. This is particularly advantageous in today's globalized and interconnected engineering landscape, where design teams may be distributed across different locations.
CATIA V6 introduces advancements in generative design, a cutting-edge approach that leverages algorithms and artificial intelligence to explore a multitude of design possibilities. Generative design goes beyond traditional methods, allowing engineers to define design parameters and constraints while the software iteratively generates and evaluates numerous design alternatives.
The simulation capabilities in CATIA V6 are also enhanced, providing engineers with a powerful toolset to analyze and validate their designs. From structural analysis to fluid dynamics, CATIA V6 enables engineers to simulate real-world conditions, ensuring that designs meet performance and safety standards.
CATIA V6 features a unified user interface that streamlines the design process and enhances user experience. The interface is designed to be intuitive, allowing both seasoned professionals and newcomers to navigate the software seamlessly. The unified environment brings together various workbenches and tools under a cohesive umbrella, promoting a more integrated and efficient design workflow.
The interface in CATIA V6 is optimized for touch-enabled devices, catering to the changing dynamics of modern work environments. This adaptability ensures that engineers can work seamlessly across different devices, from traditional desktops to mobile tablets, enhancing flexibility and accessibility.
In CATIA V6, a fundamental shift occurs towards a data-centric design philosophy. The software manages design data in a more structured and organized manner, facilitating better version control, collaboration, and data reuse. This approach is particularly beneficial in large-scale engineering projects where the volume of data and the need for collaboration are significant.
CATIA V6's data-centric design also enhances traceability, allowing engineers to track changes and understand the evolution of a design over time. This feature is crucial for maintaining the integrity of the design process and ensuring that decisions are well-informed.
The applications of CATIA V6 span a wide spectrum of industries, from automotive and aerospace to consumer goods and beyond. In the automotive sector, CATIA V6 is embraced for its ability to handle the complexity of designing modern vehicles. From the chassis to the interior components, CATIA V6 facilitates the creation of designs that meet the stringent safety and performance requirements of the automotive industry.
In aerospace and defense, CATIA V6 plays a pivotal role in designing aircraft and spacecraft components. The software's generative design capabilities are particularly valuable in this sector, where lightweight yet structurally robust designs are essential for fuel efficiency and overall performance.
Comparison:
The user interface (UI) is the gateway to any software, shaping the user experience and influencing the efficiency of design workflows. In the realm of Computer-Aided Design (CAD), where precision and usability are paramount, understanding the nuances of user interfaces is crucial. CATIA, a stalwart in the CAD landscape, has seen significant changes in its UI as it transitioned from V5 to V6. In this comprehensive comparison, we will delve into the user interfaces of CATIA V5 and V6, exploring their design philosophies, functionalities, and how they impact the overall user experience.
CATIA V5, with its longstanding presence in the CAD community, has a UI that reflects years of refinement and optimization. The UI is organized into workbenches, each dedicated to specific tasks such as Part Design, Assembly Design, Drafting, and more. This modular approach allows users to access tools relevant to their current tasks, promoting an organized and focused design environment.
Workbenches in CATIA V5 are grouped based on the type of tasks they cater to. For example, the Part Design workbench is tailored for 3D parametric modeling, while the Assembly Design workbench focuses on managing complex assemblies. This segmentation ensures that users can seamlessly transition between different aspects of the design process without unnecessary clutter.
CATIA V5 employs task-based toolbars that change dynamically based on the selected workbench and task. This context-sensitive approach streamlines the UI, presenting users with only the tools relevant to their current activities. It contributes to a more intuitive and user-friendly experience, especially for those new to the software.
CATIA V5 allows users to customize the UI to a certain extent, enabling them to create personalized toolbars and layouts. This flexibility is advantageous for users who prefer a tailored workspace based on their specific workflows and frequently used tools.
Icons play a significant role in the CATIA V5 UI, providing a visual representation of tools and commands. The use of icons aids in quick recognition, contributing to the overall speed and efficiency of the design process. However, it may pose a slight learning curve for new users unfamiliar with the icons' meanings.
CATIA V6 represents a departure from the traditional file-centric approach of V5, embracing a more collaborative and data-centric design philosophy. The UI in V6 undergoes a significant transformation to accommodate new functionalities, emphasizing a unified and streamlined design experience.
CATIA V6 introduces a unified user interface that consolidates various workbenches and tools under a cohesive umbrella. This unified environment aims to simplify the design process, presenting users with a consistent and integrated workspace. The toolbar and command layout remain consistent across different tasks, contributing to a more cohesive and efficient design workflow.
V6 introduces the concept of role-based dashboards, tailoring the UI to the specific needs of different users or roles within a design team. For example, a design engineer might have a dashboard optimized for parametric modeling, while a project manager's dashboard could focus on collaboration and project management tools. This role-based approach enhances the adaptability of the UI to diverse user needs.
Recognizing the evolving nature of work environments, CATIA V6 is optimized for touch-enabled devices. The UI is designed to be responsive and intuitive on tablets and other touch-enabled devices, fostering flexibility in how and where users interact with the software.
A significant departure from V5 is CATIA V6's integration with cloud-based platforms. The UI seamlessly incorporates cloud collaboration features, allowing multiple users to work on a design simultaneously. This cloud-centric approach aligns with the demands of modern design teams that may be geographically dispersed.
In CATIA V6, the UI reflects a shift towards a data-centric design philosophy. Design data is managed in a structured manner, contributing to better version control and collaboration. This approach is particularly advantageous in large-scale engineering projects where data organization and traceability are critical.
Comparative Analysis:
CATIA V5's UI, with its task-based organization and iconic representation, may offer a more familiar and approachable experience for users transitioning from other CAD software. The contextual toolbars contribute to a streamlined learning curve, helping users quickly adapt to the software.
On the other hand, CATIA V6's unified UI and role-based dashboards may initially present a steeper learning curve for users accustomed to the V5 environment. However, the consistent layout across different tasks and the adaptability of role-based dashboards can enhance efficiency once users become familiar with the system.
CATIA V5 provides a reasonable degree of customization, allowing users to create personalized toolbars and adapt the UI to their preferences. This flexibility is beneficial for users who prefer a tailored workspace based on their specific workflows.
CATIA V6, while introducing a more unified interface, might offer less flexibility for users seeking extensive customization. The emphasis on role-based dashboards, while enhancing the UI's adaptability, may limit the extent to which individual users can personalize their workspace.
CATIA V6 shines in terms of collaboration and accessibility. The cloud integration and touch-enabled interface in V6 cater to the needs of a modern, globally dispersed workforce. The unified UI and data-centric design philosophy contribute to a collaborative environment where multiple users can seamlessly work on a design in real-time.
CATIA V5, while offering collaboration features, may not match the level of real-time, cloud-based collaboration that V6 provides. Its traditional file-centric approach might pose challenges in scenarios where instantaneous collaboration and data accessibility are crucial.
The performance of CATIA V5 and V6 can depend on various factors, including the complexity of the design, system specifications, and network conditions. CATIA V5, being a mature software, is optimized for traditional desktop environments and may exhibit robust performance for many design scenarios.
CATIA V6's cloud-centric approach introduces dependencies on network speed and cloud infrastructure. While the cloud can enhance collaboration, users in regions with slower internet connections may experience delays. However, the performance of V6 can be competitive, especially in scenarios where its cloud-based features are leveraged effectively.
Conclusion:
In the intricate domain of mechanical engineering, choosing between CATIA V5 and V6 is akin to selecting the right tool for a precise task. CATIA V5, with its trusted legacy, provides a familiar and reliable desktop-centric environment. Its user-friendly interface and customizable features make it an accessible choice for those transitioning from other CAD tools. Parametric modeling, assembly design, and drafting functionalities in CATIA V5 have been the backbone of countless projects, offering a solid foundation for intricate designs.
On the horizon of design evolution, CATIA V6 emerges as a dynamic solution, redefining collaboration and adaptability. Its unified interface, role-based dashboards, and cloud integration signify a departure from tradition. While the learning curve may be steeper initially, the rewards lie in real-time collaboration and a touch-enabled interface. For those embracing innovation, CATIA V6 offers a platform optimized for the demands of a modern, globally dispersed workforce.
Choosing between V5 and V6 is a nuanced evaluation of project needs and technological context. Some projects may thrive in V5's reliability, while others benefit from V6's collaborative features. The decision is not static; it demands adaptability. Staying informed about updates and considering specific assignment needs ensures the chosen CATIA version aligns seamlessly with project goals.
In conclusion, the CATIA V5 vs. V6 dilemma reflects the evolving nature of mechanical engineering. Whether traversing familiar V5 terrains or venturing into V6 possibilities, the key lies in making an informed decision that resonates with project demands. Each version offers a pathway for engineers to carve their mark in the ever-evolving landscape of mechanical engineering, where precision meets boundless innovation.