Conducting Structural Analysis in ANSYS: A Comprehensive Guide for Students!
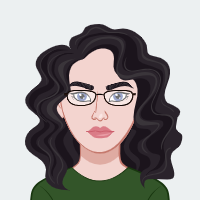
Structural analysis stands as a cornerstone in the realm of mechanical engineering, wielding profound significance in the design, development, and optimization of diverse structures and components. At its core, mechanical engineering revolves around the creation of products that span from towering bridges and industrial machinery to delicate aerospace systems. The pivotal role of structural analysis lies in its ability to unravel the intricate interactions within these entities, offering engineers a comprehensive understanding of how materials respond to various forces and conditions. If you need help with your ANSYS assignment, professionals in the field can provide the expertise and assistance required for successful completion.
In the multifaceted world of mechanical engineering, safety stands as a paramount concern. Structural analysis serves as the vanguard in ensuring the safety and reliability of engineered structures. By subjecting designs to rigorous simulations that replicate real-world conditions, engineers can discern potential vulnerabilities, stress concentrations, and failure modes. This foresight is instrumental in forestalling catastrophic failures, mitigating risks, and safeguarding both the structural integrity of the product and the well-being of its users. In essence, structural analysis acts as the sentinel, scrutinizing designs to guarantee they withstand the myriad forces encountered during their operational lifespan.
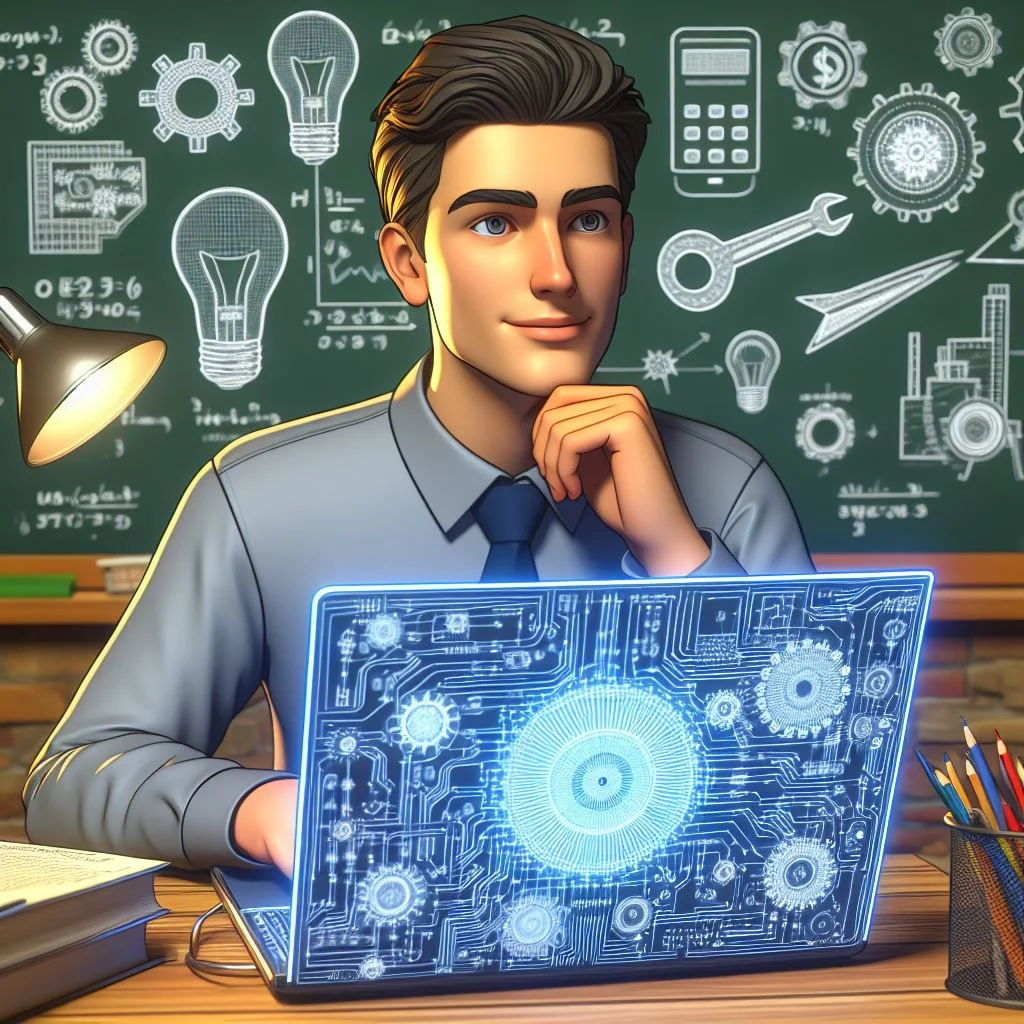
Moreover, the optimization of designs represents a key facet of structural analysis. Engineers utilize this tool to fine-tune and enhance designs, seeking the delicate balance between achieving optimal performance and minimizing material usage. This dual objective not only fosters efficiency but also underpins cost-effectiveness. Structural analysis empowers engineers to explore a spectrum of design possibilities, guiding them toward solutions that not only meet performance criteria but also economize resources—a critical consideration in an era where sustainability and resource efficiency are at the forefront of engineering practice.
The predictive prowess of structural analysis is another linchpin in its importance to mechanical engineering. Engineers rely on this analytical tool to anticipate how structures will respond under an array of scenarios, be it varying loads, environmental conditions, or dynamic forces. This predictive capability is indispensable in fine-tuning designs for peak performance, ensuring that engineered components fulfill their intended functions across a spectrum of real-world conditions. Whether it be a bridge enduring heavy traffic, a machine enduring cyclic loads, or an aircraft navigating turbulent skies, structural analysis empowers engineers to envision and account for the myriad challenges that may be encountered.
Furthermore, structural analysis catalyzes innovation within the field of mechanical engineering. By unraveling the complexities of structural behavior, engineers can explore novel design solutions that push the boundaries of conventional thinking. This capacity for innovation is particularly crucial in an ever-evolving technological landscape where demands for efficiency, sustainability, and performance continually drive the need for groundbreaking engineering solutions. Structural analysis acts as both a compass and a catalyst, guiding engineers toward inventive designs that address contemporary challenges and lay the groundwork for future advancements.
In the intricate tapestry of engineering, problem-solving emerges as an overarching theme, and structural analysis is a potent tool in the engineer's arsenal. When faced with design challenges or performance issues, engineers turn to structural analysis to dissect the intricacies of the problem at hand. This analytical approach enables systematic identification of issues, from stress concentrations to material weaknesses, facilitating targeted and effective problem-solving. In essence, structural analysis serves as a troubleshooter, aiding engineers in diagnosing and rectifying issues to ensure the optimal functionality and longevity of mechanical systems.
Understanding Structural Analysis.
Structural analysis stands as the bedrock of engineering design, an indispensable discipline that delves into the complex interplay of forces and materials to ensure the integrity, safety, and functionality of structures. At its essence, structural analysis can be defined as the systematic examination and evaluation of the behavior of structures and components under various conditions, encompassing factors such as loads, forces, and environmental influences. This analytical discipline employs mathematical models and computational tools to simulate the response of structures to applied forces, providing engineers with crucial insights into how materials deform, deflect, and bear loads. The significance of structural analysis in engineering design is multifaceted, playing a pivotal role in every stage of the design process.
First and foremost, structural analysis is the sentinel of safety in engineering design. The fundamental responsibility of any engineer is to create structures and components that can withstand the forces and conditions they will encounter during their operational life. By subjecting designs to rigorous analysis, engineers can identify potential weak points, stress concentrations, and failure modes. This proactive approach is essential for mitigating risks and preventing catastrophic failures, ensuring that structures meet not only functional requirements but also stringent safety standards. The predictive nature of structural analysis enables engineers to foresee how a structure will behave under diverse scenarios, providing a comprehensive understanding of its limitations and allowing for informed decision-making in design iterations.
In the intricate tapestry of engineering design, structural analysis acts as the cornerstone for optimizing structures. The goal is not merely to create structures that meet minimum safety requirements but to do so in the most efficient and cost-effective manner. Engineers employ structural analysis to fine-tune designs, striking a delicate balance between optimal performance and minimal material usage. This optimization process is integral to achieving efficiency, reducing waste, and adhering to economic constraints. By leveraging the insights gained through structural analysis, engineers can refine designs iteratively, ensuring that the final product represents the most effective use of resources without compromising safety or performance.
Moreover, structural analysis serves as a predictive tool that guides engineering decisions across a spectrum of applications. Whether designing a bridge, a building, a machine, or an aerospace component, engineers rely on structural analysis to anticipate how their creations will respond under different conditions. This foresight is critical for designing structures that can adapt to varying loads, environmental factors, and dynamic forces. From understanding the wind resistance of a skyscraper to predicting the stress distribution in an aircraft wing, structural analysis empowers engineers to make informed decisions that contribute to the overall success and reliability of their designs.
In addition to safety and optimization, structural analysis fosters innovation in engineering design. Engineers often face challenges that demand creative solutions, and structural analysis provides a systematic framework for exploring novel design possibilities. By comprehensively understanding the behavior of materials and structures, engineers can push the boundaries of conventional thinking, leading to innovative solutions that address contemporary challenges. This capacity for innovation is particularly crucial in a rapidly evolving technological landscape where demands for sustainability, efficiency, and performance drive the need for groundbreaking engineering solutions.
Furthermore, structural analysis is integral to effective problem-solving in engineering design. When faced with issues such as unexpected deformations, material failures, or performance discrepancies, engineers turn to structural analysis to diagnose and rectify problems systematically. This analytical approach enables the identification of root causes, guiding engineers in devising targeted solutions that enhance the overall functionality and longevity of the designed structures.
In conclusion, structural analysis is the linchpin of engineering design, defining the contours of safety, optimization, prediction, innovation, and problem-solving. Its systematic examination of structural behavior empowers engineers to create designs that not only meet functional requirements but also stand resilient against the diverse challenges posed by the real-world environment. As a discipline that continues to evolve alongside technological advancements, structural analysis remains a cornerstone in shaping the future of engineering design, ensuring that structures are not only safe and efficient but also at the forefront of innovation.
Introduction to ANSYS.
ANSYS stands as a preeminent and comprehensive Finite Element Analysis (FEA) software, wielding transformative capabilities that have made it an indispensable tool in the arsenal of engineers and designers across various disciplines. Renowned for its robust simulation capabilities, ANSYS enables users to model, simulate, and analyze complex physical phenomena, providing invaluable insights into the behavior of structures and systems under diverse conditions. At its core, finite element analysis involves breaking down complex structures into smaller, more manageable elements, allowing for a detailed examination of the interactions between different components. ANSYS excels in this realm, offering a user-friendly yet powerful platform that caters to a broad spectrum of engineering applications.
One of the standout features of ANSYS is its versatility, making it applicable across a myriad of engineering domains. Whether it be structural mechanics, fluid dynamics, heat transfer, electromagnetics, or a combination of these, ANSYS provides a unified platform for conducting simulations and analyses. This versatility is particularly advantageous in industries where interdisciplinary considerations are paramount, such as aerospace, automotive, energy, and civil engineering. The software's ability to seamlessly transition between different physics domains makes it a go-to solution for engineers dealing with multifaceted challenges in their designs.
The strength of ANSYS lies in its finite element analysis capabilities, allowing users to discretize complex geometries into smaller, more manageable elements for analysis. This process enables engineers to capture the intricacies of real-world structures, accounting for factors like material properties, boundary conditions, and loading scenarios with a high degree of precision. The finite element method implemented in ANSYS provides a systematic approach to solving partial differential equations that govern the behavior of physical systems. Through this method, ANSYS facilitates the accurate prediction of how structures will respond to various stimuli, offering insights into stress distribution, deformation, and other critical performance metrics.
Another hallmark of ANSYS is its extensive library of material models, enabling users to simulate a wide range of materials with diverse mechanical, thermal, and electromagnetic properties. This comprehensive material library empowers engineers to accurately represent the behavior of real-world materials, enhancing the accuracy of simulations and the reliability of analysis results. Whether dealing with metals, polymers, composites, or specialized materials, ANSYS provides the tools to capture the nuanced behavior of these materials under different conditions.
The software's user-friendly interface is designed to cater to both novice users and seasoned professionals, with features that facilitate efficient workflow and easy navigation. ANSYS Workbench, the graphical user interface for ANSYS, provides a unified environment where users can seamlessly transition between different simulation tasks. This streamlined approach enhances collaboration among multidisciplinary teams, as it allows engineers to work cohesively on various aspects of a project within a single interface.
Furthermore, ANSYS doesn't merely stop at static structural analysis; it excels in dynamic simulations as well. Engineers can employ ANSYS to study the response of structures to dynamic loading conditions, including vibrations, impact, and transient forces. This capability is invaluable in industries where the dynamic behavior of structures is of paramount importance, such as automotive crash simulations, seismic analysis for civil structures, or machinery subjected to cyclic loading.
In addition to its prowess in structural analysis, ANSYS is renowned for its capabilities in fluid dynamics analysis. The software facilitates the simulation of fluid flow, heat transfer, and related phenomena, enabling engineers to optimize designs for efficiency and performance. Whether analyzing aerodynamics for aircraft, thermal management in electronic devices, or fluid flow in pipelines, ANSYS provides a comprehensive suite of tools for fluid dynamics simulations.
Furthermore, ANSYS incorporates electromagnetics analysis capabilities, allowing engineers to study electromagnetic fields and their impact on designs. This is particularly crucial in industries such as electronics, where the interaction of electromagnetic fields with components must be thoroughly understood to ensure the proper functioning of devices.
In conclusion, ANSYS stands as a pinnacle in the realm of finite element analysis software, offering a versatile and powerful platform that caters to the diverse needs of engineers across various disciplines. Its finite element analysis capabilities, extensive material library, dynamic simulation tools, and user-friendly interface position it as a go-to solution for professionals seeking accurate and reliable insights into the behavior of complex systems. ANSYS's impact extends beyond traditional structural analysis, encompassing fluid dynamics, electromagnetics, and other crucial engineering domains, making it a cornerstone in the quest for innovation and optimization in engineering design.
Meshing.
Meshing is a pivotal step in structural analysis, playing a crucial role in the accuracy, reliability, and computational efficiency of finite element simulations. At its core, meshing involves dividing complex geometric structures into smaller, finite-sized elements to numerically represent the physical model. The significance of meshing can be understood through several key aspects.
Firstly, the accuracy of simulation results hinges on the quality of the mesh. A finer mesh, composed of smaller elements, allows for a more precise representation of the structure's behavior. It enables the capture of localized stress concentrations, subtle deformation patterns, and other intricacies that impact the structural response. However, finding the right balance is paramount, as excessively fine meshes can lead to computational inefficiencies and increased processing times.
Moreover, the convergence and stability of the analysis are deeply influenced by the mesh. A well-structured mesh facilitates the convergence of numerical solutions and ensures stability throughout the analysis process. In contrast, a poorly designed mesh may lead to numerical instability, causing the analysis to diverge or fail to converge to a solution. Achieving a mesh that converges reliably is essential for obtaining accurate and trustworthy simulation results, especially when dealing with complex mechanical systems.
Furthermore, computational efficiency is a critical consideration in structural analysis, and meshing plays a pivotal role in this aspect. The choice of mesh density directly impacts the computational resources required for simulations. An optimal mesh strikes a balance between accuracy and computational efficiency, ensuring that the analysis is both reliable and manageable in terms of time and resources. This consideration is particularly relevant in engineering contexts where timely decision-making is crucial.
When using ANSYS for meshing in structural analysis, several guidelines can be followed to ensure the creation of a high-quality mesh. Firstly, it is essential to pay attention to the element type selection. ANSYS provides various element types, each suited for specific types of analyses. Choosing the appropriate element type based on the geometry and loading conditions is vital for accurate results.
Additionally, mesh refinement should be strategically applied in regions of interest. Critical areas with high stress gradients, complex geometry, or where structural behavior changes abruptly should have a finer mesh to capture localized effects accurately. ANSYS allows for local mesh refinement, enabling users to focus computational resources where they matter most.
The aspect ratio of elements is another crucial consideration. Ideally, elements should be as close to equilateral as possible to avoid distorted shapes that can compromise solution accuracy. ANSYS provides tools to assess and improve element quality, allowing users to identify and address issues related to skewed or highly stretched elements.
Regularly inspecting the mesh for quality indicators, such as element skewness and aspect ratio, is a good practice. ANSYS provides visualization tools to assess mesh quality and diagnose potential problems before running the analysis. Additionally, conducting sensitivity analyses by refining the mesh iteratively allows for the identification of the optimal balance between accuracy and computational efficiency.
In conclusion, meshing stands as a cornerstone in structural analysis, impacting the accuracy, reliability, and computational efficiency of finite element simulations. The judicious application of meshing guidelines in ANSYS ensures that the numerical representation of complex structures aligns with the physical reality, providing engineers with trustworthy insights into the behavior of mechanical components and systems.
Conclusion:
In conclusion, navigating the intricacies of conducting structural analysis in ANSYS represents a transformative journey for students entering the dynamic realm of mechanical engineering. This comprehensive guide has aimed to demystify the process, emphasizing the pivotal role of ANSYS as a powerful finite element analysis tool. From the importance of structural analysis in ensuring safety and optimization in engineering designs to the versatile capabilities of ANSYS across various domains like fluid dynamics and electromagnetics, students are now equipped with a robust understanding of how to harness this tool for their academic and professional pursuits.
The step-by-step approach outlined—from the installation of ANSYS and setting up licensing to the intricacies of meshing and iterative refinement—provides a roadmap for students to seamlessly transition from theoretical concepts to hands-on application. The significance of meshing, highlighted in this guide, underscores its role in determining the accuracy and reliability of simulation results. As students embark on creating finite element models, assigning materials, defining boundary conditions, and interpreting results, they are encouraged to embrace the iterative nature of structural analysis. This iterative mindset, coupled with a keen eye for mesh quality, ensures that the analytical journey is not just a linear process but a dynamic exploration where each refinement brings them closer to a robust and reliable solution.
In the rapidly evolving landscape of engineering, where innovation and problem-solving are paramount, the proficiency gained in conducting structural analysis using ANSYS opens doors to limitless possibilities. The ability to predict and optimize the behavior of structures is not just a theoretical exercise; it is a practical skill set that empowers students to contribute meaningfully to real-world engineering challenges. As they embark on their academic and professional endeavors, the knowledge gleaned from this comprehensive guide serves as a sturdy foundation, enabling students to tackle complex problems with confidence and precision.