Advanced Meshing Techniques in ANSYS: Optimizing Models for Precision!
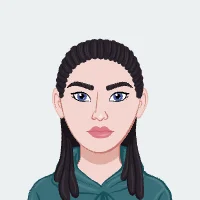
Meshing plays a pivotal role in the realm of Finite Element Analysis (FEA), serving as a foundational step that significantly influences the accuracy and reliability of engineering simulations. In the intricate landscape of FEA, where virtual models are subjected to complex stress, thermal, and fluid analyses, the mesh acts as a computational scaffold, discretizing the physical structure into smaller, manageable elements. This discretization is imperative because it enables the translation of continuous physical phenomena into a discrete numerical representation, allowing for the application of mathematical principles to simulate and analyze real-world scenarios. If you need help with your Ansys assignment, understanding the importance of meshing in FEA can provide valuable insights and support to tackle your assignments effectively.
Within this context, ANSYS emerges as a leading software solution that has garnered widespread acclaim for its prowess in conducting detailed and sophisticated engineering simulations. ANSYS provides engineers and researchers with a robust platform to simulate the behavior of structures and systems under various conditions. However, the efficacy of ANSYS simulations hinges significantly on the quality of the mesh employed in the analysis. In essence, the mesh serves as the bridge between the physical reality of an object and its digital representation, and the precision of this bridge is directly correlated with the reliability of the simulation outcomes.
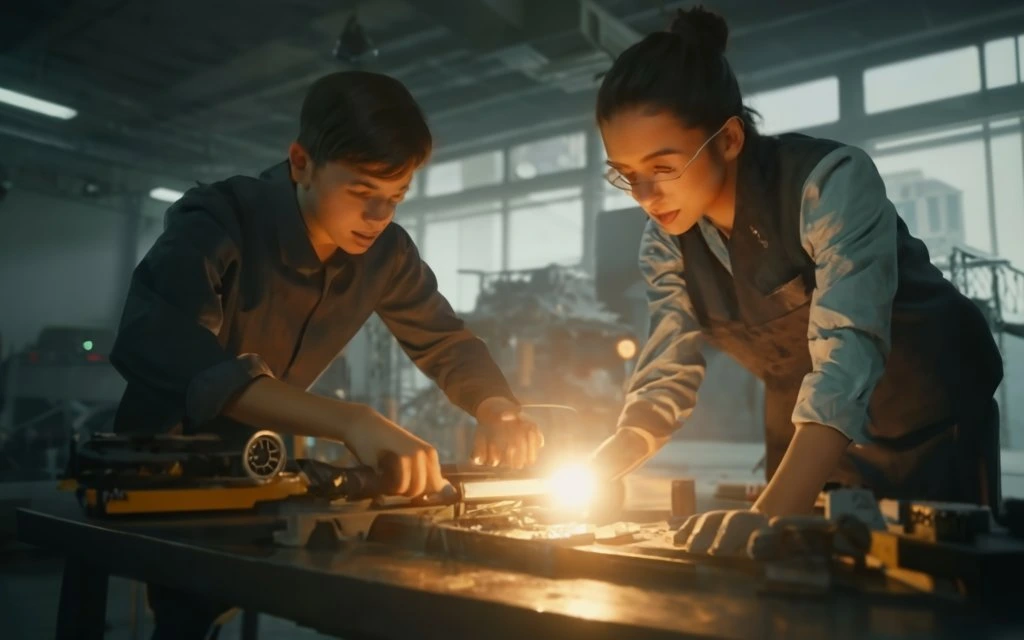
The role of meshing in ANSYS simulations extends beyond mere geometric discretization. It involves the subdivision of the model into finite elements, ensuring that each element captures the intricacies of the physical structure while facilitating efficient computational analysis. An inadequate mesh can lead to inaccuracies in predicting stress concentrations, deformation patterns, and other critical engineering parameters. On the contrary, a well-constructed mesh ensures that the simulation captures the nuances of the real-world behavior, providing engineers with actionable insights and facilitating informed decision-making.
The impact of meshing on model accuracy is particularly pronounced in scenarios involving structural mechanics, fluid dynamics, and thermal analyses. For instance, in structural simulations, a finely tuned mesh is crucial for capturing stress concentrations and accurately predicting failure points. In fluid dynamics simulations, an appropriately refined mesh is essential to capture fluid flow patterns and turbulence. Similarly, in thermal analyses, the mesh quality plays a decisive role in predicting temperature distributions and thermal stresses. In essence, the fidelity of the mesh directly translates to the fidelity of the simulation results, making meshing a cornerstone of accurate and reliable FEA.
ANSYS, recognizing the pivotal role of meshing in achieving accurate simulations, provides users with a suite of advanced meshing tools. These tools enable engineers to create high-quality meshes that adapt to the complexities of diverse engineering scenarios. Whether it's refining the mesh in critical regions, adapting to changing geometric features, or accommodating for different physics, ANSYS meshing capabilities empower users to tailor the mesh to the specific requirements of their simulations.
In conclusion, meshing stands as a fundamental and indispensable facet of Finite Element Analysis, acting as the linchpin that connects the physical world with its virtual representation. ANSYS, with its sophisticated meshing capabilities, contributes significantly to the accuracy and reliability of engineering simulations. By ensuring a finely tuned mesh, ANSYS facilitates the translation of complex physical phenomena into actionable insights, empowering engineers to make informed decisions and advance the frontiers of engineering simulation.
Understanding Meshing Basics:
Meshing, in the context of Finite Element Analysis (FEA), is a critical computational process that involves dividing complex geometric structures into smaller, interconnected elements. This discretization is essential for numerical analysis, allowing engineers to simulate and analyze the behavior of structures under various conditions. The significance of meshing in FEA lies in its ability to translate continuous physical systems into a discrete, computationally manageable form. By breaking down a complex object or system into finite elements, meshing enables the application of mathematical principles to model the interactions and responses of these elements to external forces, temperatures, or fluid flows.
In the realm of FEA, where accuracy is paramount, the quality of the mesh directly influences the reliability of simulation results. A well-constructed mesh ensures that the simulated model adequately captures the nuances of the physical structure, providing engineers with insights into stress distributions, deformation patterns, and other critical parameters. Conversely, a poor mesh can lead to inaccuracies, hindering the ability to make informed decisions about the structural integrity, thermal performance, or fluid dynamics of a given design.
When delving into basic meshing concepts in ANSYS, it's crucial to understand the elements that constitute the mesh. The most fundamental unit is the finite element, a small geometric shape that represents a discrete portion of the overall structure. ANSYS employs various types of elements, such as triangles or quadrilaterals in 2D simulations and tetrahedra or hexahedra in 3D simulations. The distribution and arrangement of these elements define the mesh, and the key challenge lies in achieving an optimal balance between element size and overall mesh density.
ANSYS provides users with a range of meshing tools to facilitate this balance and achieve accurate simulations. The software allows engineers to control mesh parameters, refine elements in critical areas, and adapt the mesh to changing geometries. Automatic mesh generation features in ANSYS streamline the process, ensuring that users can focus on refining and optimizing the mesh for specific analysis requirements rather than spending excessive time on manual mesh generation.
In summary, meshing is a fundamental step in FEA, playing a pivotal role in translating complex physical structures into a numerical format for simulation and analysis. The significance of meshing lies in its impact on the accuracy and reliability of simulation results, with ANSYS providing engineers with tools and capabilities to efficiently create, refine, and optimize meshes for a wide range of engineering simulations.
Challenges in Meshing:
Mesh generation in Finite Element Analysis (FEA) is a crucial step that comes with its own set of challenges. One common challenge is the trade-off between mesh refinement and computational efficiency. Achieving a finely detailed mesh throughout the entire model can be computationally expensive and time-consuming, especially for large and complex geometries. Striking the right balance between mesh refinement and computational cost is a delicate task, as overly coarse meshes may fail to capture important features, while excessively fine meshes may strain computational resources.
Another challenge arises in dealing with complex geometries. Irregular shapes, sharp corners, or regions with drastic changes in geometry can pose difficulties in generating a well-behaved mesh. Ensuring that the mesh accurately represents these geometric intricacies is challenging, and manual intervention may be required to refine the mesh in critical areas. Automated meshing algorithms often struggle with such complexities, necessitating user expertise to ensure the fidelity of the mesh.
Inadequate mesh quality is a significant concern with far-reaching implications for simulation results. Poor mesh quality can lead to inaccurate predictions of stress concentrations, deformation patterns, and other engineering parameters. Common issues include element distortion, where elements become excessively elongated or skewed, and poorly shaped elements, such as elements with aspect ratios deviating from ideal shapes. These problems can compromise the convergence of the simulation, introduce errors, and result in unreliable predictions.
The impact of poor mesh quality on simulation results is profound. Inaccurate meshing can lead to the generation of spurious stresses, unrealistic deformation patterns, and erroneous thermal or fluid flow predictions. In structural analyses, for example, distorted elements might incorrectly predict failure points, compromising the safety assessment of a design. In fluid dynamics simulations, poor mesh quality can misrepresent flow patterns, affecting the assessment of aerodynamic performance or heat transfer.
Furthermore, convergence issues may arise, where the simulation fails to reach a stable solution due to the challenges introduced by a poorly constructed mesh. This not only hampers the reliability of the results but also increases computational time and resources expended on the analysis.
In conclusion, mesh generation in FEA is confronted with challenges related to balancing refinement and efficiency, handling complex geometries, and ensuring mesh quality. The impact of poor mesh quality on simulation results is profound, affecting the accuracy and reliability of predictions in structural, thermal, and fluid dynamics analyses. Addressing these challenges requires a careful consideration of the specific requirements of the simulation, manual intervention in critical areas, and the use of advanced meshing techniques to optimize the quality of the mesh.
Introduction to Advanced Meshing Techniques:
ANSYS, a leading software solution for engineering simulations, offers a suite of advanced meshing techniques that elevate the precision and accuracy of Finite Element Analysis (FEA). One notable technique is Automatic Mesh Refinement (AMR), which allows for adaptive refinement of the mesh based on the gradients of physical quantities, ensuring that regions with high variations receive finer meshes while less critical areas maintain a coarser resolution. This dynamic adaptation enhances the efficiency of simulations by concentrating computational resources where they are most needed, enabling a more accurate representation of complex phenomena.
Another powerful feature within ANSYS is the use of High-Order Meshing. This technique involves employing higher-order elements, such as quadratic or cubic elements, instead of traditional linear elements. By capturing more complex variations within elements, high-order meshing provides a more accurate representation of the physical behavior of the structure or system under analysis. This is particularly beneficial in simulations requiring a high level of precision, such as those involving intricate geometries, sharp gradients, or stress concentrations.
Advanced meshing techniques in ANSYS also encompass geometry-based meshing, where the mesh is tailored to match the underlying geometry more closely. This approach ensures that the mesh aligns with complex geometrical features, minimizing element distortion and improving the overall quality of the mesh. Additionally, techniques like swept meshing and hexahedral meshing are employed to generate structured meshes for improved efficiency and accuracy, especially in simulations involving fluid dynamics or thermal analyses.
The benefits of utilizing these advanced meshing techniques in ANSYS extend beyond mere convenience. Precision in engineering simulations is paramount, and advanced meshing plays a pivotal role in achieving this precision. By adapting the mesh dynamically based on the simulation's requirements, ANSYS allows for a more detailed representation of critical areas, enhancing the accuracy of stress, strain, temperature, and fluid flow predictions. High-order meshing ensures that the simulation captures subtle variations in the physical behavior of the system, leading to more reliable results in scenarios where precision is paramount.
Moreover, advanced meshing techniques contribute to convergence robustness, reducing the likelihood of convergence issues and ensuring that simulations reach stable and accurate solutions. The improved mesh quality leads to a more efficient use of computational resources, minimizing the time and effort required for simulations while enhancing the overall reliability of the analysis.
In conclusion, ANSYS offers a comprehensive array of advanced meshing techniques that go beyond conventional methods, providing engineers with powerful tools to enhance the precision and reliability of their simulations. The adaptive nature of these techniques, combined with the use of high-order elements and geometry-based meshing, contributes significantly to achieving accurate and detailed representations of complex engineering systems, making ANSYS a preferred choice for those seeking precision in their simulation endeavors.
Tips for Optimizing Mesh for Precision:
Optimizing mesh quality is crucial for achieving accurate and reliable results in finite element analysis (FEA). Several practical tips can enhance mesh quality and contribute to the overall success of engineering simulations. First and foremost, attention to mesh element size is paramount. Balancing element size throughout the model is crucial; too small elements may lead to computational inefficiency, while overly large elements can sacrifice accuracy. Establishing an optimal element size requires an understanding of the physical characteristics of the system under study, guiding the engineer to select a mesh that captures relevant details without excessive refinement.
Additionally, employing high-quality elements is vital for mesh optimization. In ANSYS, for instance, utilizing quadratic or cubic elements instead of linear elements enhances the accuracy of simulations by capturing more nuanced variations within each element. High-order elements contribute to improved representation of complex geometries and enable a more accurate assessment of stress, strain, and other critical parameters.
Geometry-based meshing offers another practical tip for optimizing mesh quality. Aligning the mesh with the underlying geometry helps reduce element distortion and ensures a smoother transition between different regions of the model. Techniques such as swept meshing, where elements are generated by sweeping through the geometry, or hexahedral meshing for structured grids, further contribute to improved mesh quality, especially in scenarios involving fluid dynamics or thermal analyses.
Refining the mesh in critical areas is of paramount importance for achieving accurate simulation results. Critical areas typically include regions with high stress gradients, sharp geometric features, or areas where significant changes in material properties occur. Applying a finer mesh in these areas allows for a more detailed representation of the physical behavior, capturing localized effects that may be crucial for the accuracy of the analysis. Manual intervention or adaptive meshing techniques, like Automatic Mesh Refinement (AMR), can be employed to ensure that the mesh adapts dynamically to the simulation's specific requirements.
The importance of refining the mesh in critical areas becomes evident in scenarios where localized phenomena significantly impact the overall system behavior. For example, in structural analyses, stress concentrations around joints or points of contact may require a finer mesh to accurately capture the distribution of stresses. Similarly, in fluid dynamics simulations, refining the mesh near boundaries or areas of flow separation ensures a more precise prediction of fluid velocities and pressure distributions.
In conclusion, optimizing mesh quality involves careful consideration of element size, the use of high-quality elements, and geometry-based meshing techniques. Refining the mesh in critical areas is essential for capturing localized effects that significantly influence the accuracy of the simulation. By adhering to these practical tips, engineers can ensure that their finite element analyses produce results that are both reliable and representative of the real-world behavior of the systems under study.
Case Studies:
Advanced meshing techniques, when applied judiciously, have demonstrated remarkable improvements in simulation accuracy across various engineering disciplines. In the realm of structural analysis, consider a complex aerospace component subjected to high loading conditions. Traditional meshing methods might struggle to capture intricate stress distributions accurately. However, by employing high-order meshing techniques in ANSYS, such as quadratic or cubic elements, engineers can achieve a more faithful representation of stress gradients and deformation patterns. In this context, advanced meshing ensures that the simulation accurately predicts stress concentrations around critical areas, providing a nuanced understanding of structural behavior that is essential for optimizing design and ensuring component integrity.
In fluid dynamics simulations, the impact of advanced meshing is equally profound. Take the example of an aerodynamic analysis for an automotive body. Traditional meshing approaches may struggle to capture the intricate flow patterns around the vehicle accurately. Employing advanced meshing techniques, such as geometry-based meshing or hexahedral meshing for structured grids, can lead to a more refined representation of the flow field. This enhancement is critical for predicting drag coefficients, lift forces, and pressure distributions with precision. Improved mesh quality in fluid dynamics simulations not only refines the accuracy of the aerodynamic predictions but also facilitates informed decision-making in optimizing vehicle design for better fuel efficiency and performance.
In thermal analyses, advanced meshing techniques play a vital role in predicting temperature distributions accurately. Consider a scenario involving electronic components on a printed circuit board (PCB). Traditional meshing methods might struggle to capture localized heating effects around electronic components. By applying adaptive meshing in critical areas or utilizing high-order meshing techniques, engineers can obtain a more accurate representation of temperature gradients. This level of precision is crucial for assessing thermal management strategies, ensuring that electronic components operate within safe temperature limits, and making informed decisions on the design and layout of the PCB.
The impact of advanced meshing on final results goes beyond mere numerical accuracy; it extends to the reliability of predictions and, consequently, decision-making in engineering. By producing simulations that closely mimic real-world behavior, advanced meshing techniques empower engineers to make informed decisions about structural integrity, fluid dynamics, thermal performance, and other critical aspects of their designs. The enhanced accuracy in simulation results translates into increased confidence in the predictive capabilities of the simulations, enabling engineers to optimize designs, troubleshoot potential issues, and innovate with greater certainty. Overall, the application of advanced meshing techniques stands as a testament to their transformative impact on simulation accuracy and the consequential benefits they bring to the decision-making process in engineering design and analysis.
Best Practices in ANSYS Meshing:
Achieving optimal mesh quality in finite element analysis (FEA) is essential for obtaining accurate and reliable simulation results. Here are some best practices to enhance mesh quality and address common misconceptions and pitfalls:
- Understand the Physics: Before initiating meshing, thoroughly understand the physical behavior of the system under analysis. Identify critical areas, stress concentrations, and regions requiring higher detail. Tailor the meshing strategy to the specific physics involved.
- Balance Element Size: Striking a balance between element size and overall mesh density is crucial. Avoid excessively coarse meshes that may overlook important details and overly fine meshes that strain computational resources without significant benefits. The optimal element size varies based on the geometry and the physics of the problem.
- Use High-Quality Elements: Incorporate high-quality elements, such as quadratic or cubic elements, when possible. These higher-order elements provide more accurate representations of complex variations within elements, contributing to improved simulation accuracy.
- Geometry-Based Meshing: Align the mesh with the underlying geometry to reduce element distortion. Techniques like swept meshing and hexahedral meshing for structured grids enhance mesh quality, especially in scenarios involving fluid dynamics or thermal analyses.
- Refine Mesh in Critical Areas: Focus on refining the mesh in critical areas where stress gradients, sharp geometrical features, or significant changes in material properties occur. Adaptive meshing techniques, like Automatic Mesh Refinement (AMR), can dynamically adjust the mesh based on simulation requirements.
Common Misconceptions and Pitfalls:
- More Elements Always Mean Better Accuracy: While a finer mesh can capture more details, it doesn't necessarily guarantee better accuracy. Excessively fine meshes can lead to increased computational costs and convergence issues without substantial improvements in accuracy. It's crucial to strike a balance based on the problem at hand.
- Automatic Meshing Solves Everything: While automatic meshing tools can be powerful, relying solely on them without manual intervention may lead to suboptimal results. Engineers should actively review and refine the automatically generated mesh to ensure it aligns with the simulation's accuracy requirements.
- Uniform Mesh Works for All Scenarios: Assuming that a uniform mesh is suitable for all parts of a model is a common misconception. Critical areas may require higher mesh density for accurate results. Neglecting mesh refinement in such regions can compromise simulation accuracy.
- Mesh Quality Is Only About Element Shape: Mesh quality is not solely determined by element shape; element size, aspect ratio, and skewness are equally important. Ignoring these factors can lead to distorted elements, affecting the accuracy of the simulation.
In summary, achieving optimal mesh quality involves a combination of understanding the physics, balancing element size, using high-quality elements, geometry-based meshing, and refining the mesh in critical areas. Addressing common misconceptions and pitfalls requires a nuanced approach, emphasizing the importance of thoughtful manual intervention, adaptive techniques, and a balanced meshing strategy tailored to the specific characteristics of the simulation.
Conclusion:
In the blog post, "Advanced Meshing Techniques in ANSYS: Optimizing Models for Precision," several key points were highlighted to underscore the significance of advanced meshing techniques in achieving precision in ANSYS simulations.
The post began by emphasizing the fundamental role of meshing in Finite Element Analysis (FEA), elucidating how it acts as a computational scaffold by discretizing complex physical structures into smaller elements. ANSYS, a renowned software solution for engineering simulations, was introduced as a powerful tool for conducting detailed analyses, with a focus on how meshing quality directly impacts the accuracy of simulation results.
The challenges in mesh generation were discussed, including the delicate balance between mesh refinement and computational efficiency, difficulties in handling complex geometries, and the repercussions of poor mesh quality. These challenges set the stage for introducing advanced meshing techniques as solutions to elevate the precision of ANSYS simulations.
Sections on understanding meshing basics and the introduction to advanced meshing techniques in ANSYS followed. Techniques such as Automatic Mesh Refinement (AMR) for adaptive refinement, High-Order Meshing for employing quadratic or cubic elements, and geometry-based meshing were explained. The post highlighted that these techniques provide users with the capability to dynamically adapt the mesh based on simulation requirements, resulting in a more accurate representation of physical systems.
Practical tips for optimizing mesh quality were shared, focusing on balancing element size, utilizing high-quality elements, and employing geometry-based meshing. Refining the mesh in critical areas was underscored as a crucial practice, emphasizing that critical regions, such as those with stress concentrations or complex geometries, demand special attention to achieve precision.
Real-world examples were showcased, illustrating how advanced meshing techniques have significantly improved simulation accuracy. Examples included structural analyses of aerospace components, fluid dynamics simulations for automotive aerodynamics, and thermal analyses for electronic components on printed circuit boards. These instances demonstrated that advanced meshing led to more accurate predictions of stress, deformation, fluid flow, and temperature distributions, providing a more reliable basis for decision-making in engineering design.
The blog post addressed common misconceptions and pitfalls in mesh generation, dispelling myths such as the notion that more elements always mean better accuracy and the idea that automatic meshing solves everything. It emphasized the importance of understanding the physics of the problem and actively refining the mesh, debunking common misconceptions that may compromise simulation accuracy.
In conclusion, the blog reiterated the paramount importance of advanced meshing techniques in achieving precision in ANSYS simulations. By dynamically adapting the mesh, utilizing high-quality elements, and refining critical areas, engineers can enhance the accuracy and reliability of their simulations, ultimately empowering them to make informed decisions in engineering design and analysis. The precision achieved through advanced meshing techniques not only refines simulation results but also contributes to the robustness of decision-making processes, ensuring that ANSYS simulations serve as reliable tools for optimizing engineering solutions.