Real-World Applications of Abaqus in Mechanical Engineering!
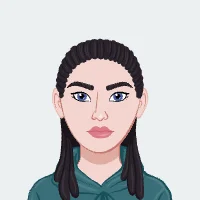
Abaqus, a cutting-edge finite element analysis (FEA) software, stands as an indomitable force in the realm of mechanical engineering, steering the course of simulation and analysis towards unparalleled precision and innovation. Developed by SIMULIA, a subsidiary of Dassault Systèmes, Abaqus has become the go-to solution for engineers and researchers navigating the complexities of mechanical systems. Its widespread utilization in academia and industry alike underscores its significance as an indispensable tool in the engineer's arsenal.
In the ever-evolving landscape of mechanical engineering, the ability to simulate and analyze complex systems is paramount. This is where Abaqus takes center stage, offering a robust platform for engineers to virtually dissect intricate mechanical structures, predict their behavior, and optimize designs before venturing into the physical realm. The software employs the finite element method (FEM), a numerical technique for solving complex physical problems, allowing engineers to break down real-world structures into smaller, more manageable elements. This approach enables a detailed analysis of structural, thermal, and fluid dynamics behaviors, offering insights that are otherwise challenging or impossible to obtain.
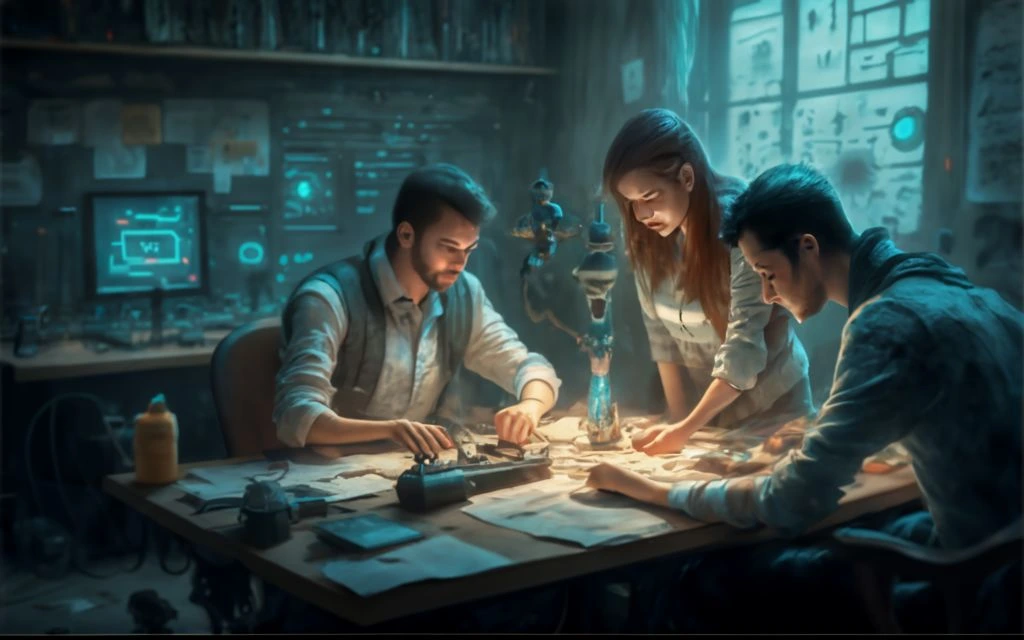
The significance of Abaqus lies in its capability to simulate a myriad of physical phenomena encountered in mechanical engineering. From structural analyses involving stress, strain, and deformation to thermal analyses encompassing heat transfer and thermal stresses, Abaqus excels in capturing the intricacies of mechanical systems. Its prowess extends to fluid-structure interaction (FSI) studies, where it becomes instrumental in modeling scenarios involving the simultaneous interaction of fluids and structures—a critical aspect in designing components for aerospace, automotive, and maritime applications.
One of the standout features of Abaqus is its ability to address the nonlinearities inherent in many mechanical systems. Whether dealing with material nonlinearity, geometric nonlinearity, or contact interactions, the software provides a sophisticated framework to tackle real-world complexities. This makes Abaqus particularly adept at handling scenarios where traditional analytical methods fall short, paving the way for more accurate predictions and optimizations in the design process.
The impact of Abaqus reverberates across various industries, including automotive, aerospace, civil engineering, and biomechanics. Engineers leverage the software to validate and refine their designs, ensuring structural integrity, thermal performance, and overall reliability. In automotive design, for instance, Abaqus aids in crash simulations, optimizing vehicle safety by assessing the impact behavior of structures. Similarly, in aerospace, the software plays a pivotal role in predicting the structural response of aircraft components to dynamic loads and environmental conditions.
In essence, Abaqus stands as a linchpin in the pursuit of excellence in mechanical engineering. Its ability to simulate the intricacies of complex systems not only accelerates the design process but also minimizes the risk of costly errors in the physical realization of projects. As the mechanical engineering landscape continues to evolve, Abaqus remains a steadfast companion, empowering engineers to push the boundaries of innovation and craft solutions that resonate with precision and reliability. In the journey towards mastering mechanical complexities, Abaqus emerges as a beacon of computational prowess, guiding engineers through the uncharted territories of simulation with unparalleled finesse.
Understanding Abaqus
Abaqus is a powerful finite element analysis (FEA) software that holds a pivotal role in the realm of mechanical engineering simulations. Developed by Dassault Systèmes, Abaqus is renowned for its versatility and capability to simulate complex mechanical systems with remarkable precision. At its core, Abaqus employs the finite element method (FEM), a numerical technique used to find approximate solutions to physical problems governed by differential equations.
One of the key features that distinguishes Abaqus is its ability to perform structural analysis, making it an indispensable tool for engineers and researchers. This software facilitates the modeling and simulation of various structures under different loading conditions, providing insights into their behavior and performance. Abaqus can simulate stress, strain, and deformation in materials, allowing engineers to predict and optimize the structural integrity of components in diverse applications.
In addition to structural analysis, Abaqus excels in thermal analysis, playing a crucial role in understanding the impact of temperature on mechanical systems. Through the software's capabilities, engineers can simulate heat transfer, thermal expansion, and thermal stress, enabling them to design components that can withstand extreme temperature conditions. This is particularly vital in industries such as electronics, aerospace, and automotive, where thermal management is critical to ensuring the reliability and longevity of components.
Moreover, Abaqus stands out for its proficiency in handling fluid-structure interaction (FSI) simulations. FSI is a complex phenomenon involving the interaction between fluids and solid structures, and Abaqus adeptly models this interplay. This capability finds applications in diverse fields, including offshore engineering, where the software can simulate the impact of waves on structures, and biomedical engineering, where fluid-structure interactions play a role in understanding blood flow dynamics.
The working principle of Abaqus revolves around dividing complex engineering structures into smaller, manageable elements. Each element is subjected to mathematical analysis, considering factors such as material properties, loading conditions, and boundary constraints. By iteratively solving these equations, Abaqus reconstructs the overall behavior of the entire system, providing engineers with a comprehensive understanding of how a structure or component will respond to different stimuli.
Furthermore, Abaqus incorporates advanced material models, allowing engineers to simulate a wide range of materials and their nonlinear behaviors. This includes plasticity, hyperelasticity, and viscoelasticity, enabling accurate representation of real-world materials and their responses under varying conditions.
Structural Analysis:
Structural analysis is a critical aspect of mechanical engineering, and Abaqus plays a pivotal role in providing accurate simulations for assessing the behavior and performance of structures in various real-world applications. One prominent application is stress analysis in bridges and buildings. Abaqus allows engineers to model complex structural systems, enabling a detailed examination of how forces and loads affect different components. For instance, when analyzing a bridge, engineers can simulate the impact of heavy traffic loads, seismic events, or environmental conditions. By utilizing Abaqus, they can evaluate stress distributions, identify potential weak points, and optimize the design for enhanced structural integrity.
In addition to bridges and buildings, Abaqus is extensively used for fatigue life prediction in automotive components. The automotive industry demands rigorous testing to ensure the durability and reliability of various parts subjected to cyclic loading conditions. Abaqus facilitates the modeling of these dynamic interactions, enabling engineers to predict and mitigate potential fatigue failures. For example, when assessing a car's suspension system, Abaqus allows for a detailed analysis of how repeated loading from driving conditions may impact the fatigue life of critical components. This level of simulation helps engineers optimize designs, select appropriate materials, and ultimately enhance the longevity and safety of automotive structures.
The capability of Abaqus in structural analysis extends beyond traditional static scenarios, encompassing dynamic and nonlinear behavior. Engineers can simulate the response of structures to time-varying loads, ensuring a comprehensive understanding of their performance under diverse conditions. The software's versatility is particularly beneficial when dealing with intricate structural geometries or complex loading scenarios commonly encountered in real-world applications.
By employing Abaqus for structural analysis, mechanical engineers gain a powerful tool that not only aids in understanding and predicting the behavior of structures but also contributes to the development of safer, more efficient designs. The ability to model stress distribution in bridges and buildings and predict fatigue life in automotive components exemplifies how Abaqus has become an indispensable asset in the field, fostering innovation and advancements in mechanical engineering practices.
Thermal Analysis:
Thermal analysis plays a pivotal role in the field of mechanical engineering, and Abaqus stands out as a versatile tool for simulating and understanding heat-related phenomena. In the realm of electronic devices, where compactness and efficiency are paramount, Abaqus proves indispensable for modeling heat dissipation. For instance, in the design of smartphones or laptops, where a myriad of components coexists in tight spaces, predicting and optimizing heat transfer is crucial. Abaqus enables engineers to simulate the thermal behavior of these devices, ensuring that temperatures remain within safe operating limits. This not only enhances the reliability of electronic components but also contributes to the longevity of the devices.
In the aerospace industry, thermal management is a critical aspect of ensuring the structural integrity and optimal performance of components subjected to extreme environmental conditions. Abaqus facilitates detailed thermal analysis in aerospace applications, such as the design of aircraft components exposed to high temperatures during flight. For instance, in the development of turbine blades or spacecraft components, engineers employ Abaqus to model and analyze heat distribution, ensuring that materials can withstand the thermal stresses associated with rapid temperature changes. This capability is paramount for enhancing the overall efficiency, safety, and durability of aerospace systems.
Moreover, Abaqus plays a crucial role in predicting and mitigating thermal issues associated with the friction and heat generated during the operation of various mechanical systems. For example, in automotive engineering, where efficient thermal management is essential for the performance of engines and braking systems, Abaqus aids in simulating and optimizing heat dissipation. This allows engineers to design cooling systems that prevent overheating and maintain the optimal functioning of critical components.
In summary, Abaqus's contribution to thermal analysis extends across diverse domains, with real-world applications ranging from electronic devices to aerospace components. By leveraging its capabilities, engineers can precisely model and predict thermal behavior, enabling them to design systems that are not only efficient but also resilient to the challenges posed by heat. As technology continues to advance, Abaqus remains at the forefront, empowering engineers to address the ever-evolving thermal management needs in the field of mechanical engineering.
Fluid-Structure Interaction (FSI):
Fluid-Structure Interaction (FSI) is a critical aspect of mechanical engineering, and Abaqus stands as a cornerstone in effectively modeling the dynamic interplay between fluids and structures. This capability has profound significance in various applications, showcasing the versatility of Abaqus in addressing complex challenges in the field.
One prominent application of Abaqus in FSI is the seismic analysis of submerged structures. In regions prone to seismic activity, understanding the impact of earthquakes on submerged infrastructure is crucial for ensuring safety and resilience. Abaqus allows engineers to simulate and analyze the intricate interactions between fluid and structure during seismic events. This includes evaluating the response of submerged foundations, pipelines, and underwater installations to seismic forces. Through this, engineers can optimize the design and placement of structures, ensuring they can withstand seismic forces without compromising functionality or safety.
Another compelling application is the wind load analysis on offshore platforms. Offshore structures, such as oil platforms and wind turbines, are subjected to dynamic wind forces in marine environments. Abaqus facilitates a comprehensive analysis of the impact of wind loads on these structures, considering the complex interaction between the fluid (wind) and the structure. Engineers can simulate different wind conditions, assess the structural response, and optimize the design to enhance stability and performance. This application is particularly crucial in the offshore industry, where the reliability and safety of structures in challenging environmental conditions are paramount.
In both seismic analysis of submerged structures and wind load analysis on offshore platforms, Abaqus proves invaluable by providing a realistic and accurate representation of fluid-structure interactions. The software's advanced computational capabilities enable engineers to predict the behavior of structures under varying conditions, leading to informed decision-making in design, construction, and maintenance.
Abaqus empowers engineers to conduct in-depth FSI analyses, considering factors like buoyancy, drag, and structural deformation. The software's ability to capture these intricate interactions ensures a more reliable and realistic representation of real-world scenarios. As the demand for robust and resilient engineering solutions continues to rise, Abaqus remains at the forefront, aiding engineers in overcoming the challenges posed by fluid-structure interactions and contributing to the advancement of safe and efficient engineering practices.
Conclusion:
In conclusion, this blog post has delved into the real-world applications of Abaqus in the realm of mechanical engineering, highlighting its significance as a powerful finite element analysis (FEA) software. We began by introducing Abaqus, shedding light on its features and capabilities, and establishing its crucial role in simulating complex mechanical systems. Throughout the exploration of structural analysis, it became evident that Abaqus plays a pivotal role in stress analysis for structures such as bridges and buildings, as well as in predicting fatigue life in automotive components.
Moving on to thermal analysis, we uncovered the applications of Abaqus in scenarios like heat dissipation in electronic devices and thermal management in aerospace components. The discussion further extended to the domain of fluid-structure interaction (FSI), where Abaqus proves instrumental in modeling intricate interactions, such as seismic analysis of submerged structures and wind load analysis on offshore platforms.
The inclusion of compelling case studies provided tangible evidence of Abaqus' efficacy in solving real-world mechanical engineering challenges. These cases illustrated its transformative impact on projects, emphasizing its capability to optimize designs and enhance overall performance.
Looking towards the future, we touched upon emerging trends and innovations in Abaqus, highlighting its continuous evolution and adaptation to meet the evolving needs of the mechanical engineering field. As technology advances, Abaqus remains at the forefront, promising further breakthroughs and solutions for intricate engineering problems.
In the spirit of empowerment, we encourage our readers to explore Abaqus for their own mechanical engineering projects. Whether grappling with structural complexities, thermal dynamics, or fluid-structure interactions, Abaqus emerges as a reliable ally in the pursuit of engineering excellence. Harnessing its capabilities can lead to more accurate simulations, improved designs, and ultimately, project success.
To take the next step in your mechanical engineering journey, we invite you to connect with our website, MechanicalEngineeringAssignmentHelp.com. Our team of experienced professionals stands ready to provide further assistance, offering expertise and support tailored to your unique needs. Don't hesitate to reach out and unlock the full potential of Abaqus in your mechanical engineering endeavors. Your success is our priority, and we look forward to being a valuable partner on your academic and professional journey.